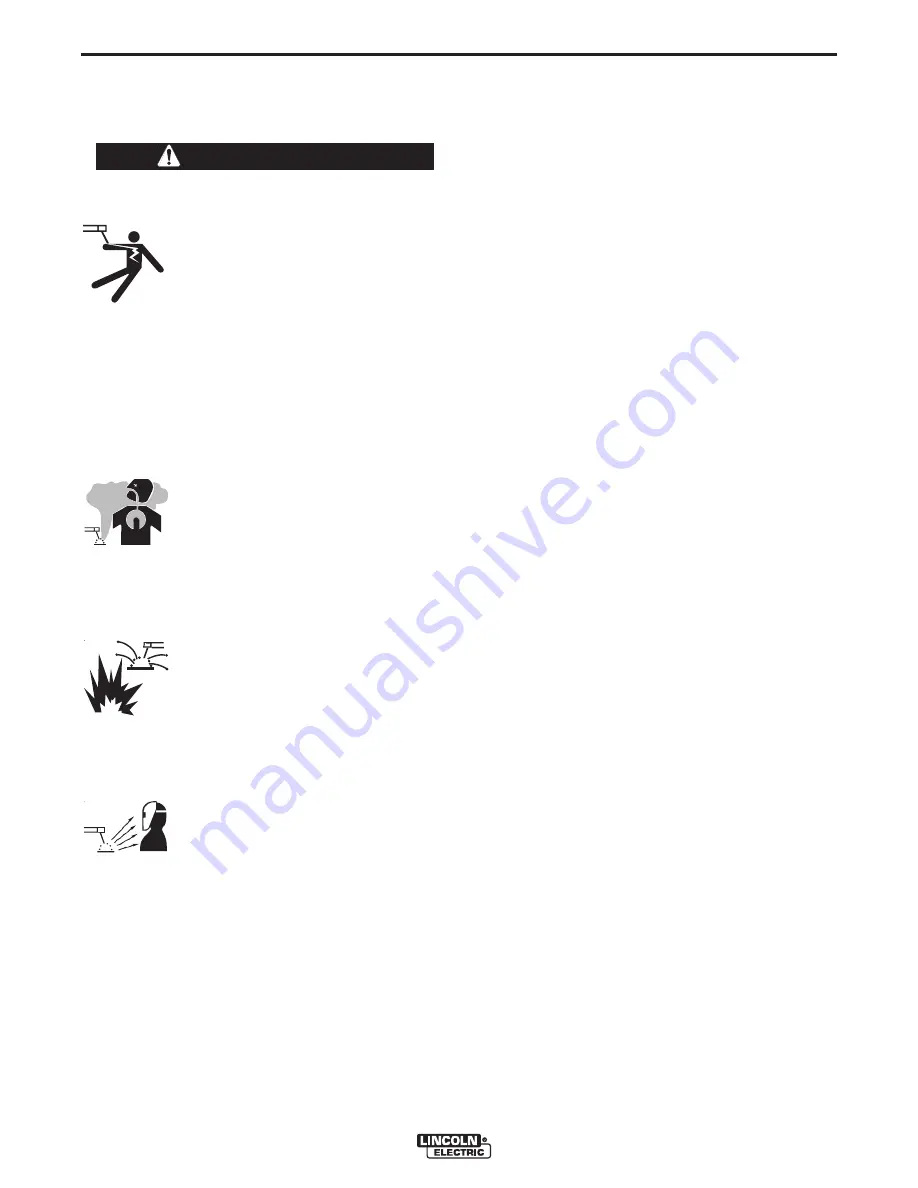
GENERAL DESCRIPTION
The Power Wave 405M semi-automatic power source
is designed to be a part of a modular, multi-process
welding system. Depending on configuration, it can
support constant current, constant voltage, and pulse
welding modes.
The Power Wave 405M power source is designed to
be used with the semi automatic family of Power Feed
wire feeders, operating as a system. Each component
in the system has special circuitry to "talk with" the
other system components, so each component (power
source, wire feeder, user interface) knows what the
other is doing at all times. These components commu-
nicate with Arclink.
The POWER WAVE 405M is a high performance, dig-
itally controlled inverter welding power source capable
of complex, high-speed waveform control. Properly
equipped, it can support the GMAW, GMAW-P,
FCAW, SMAW, GTAW, and CAC-A processes. It car-
ries an output rating of 350 Amps, 34 Volts at 60%
duty cycle and 300 Amps, 32 volts at 100% duty
cycle.
RECOMMENDED PROCESSES AND
EQUIPMENT
RECOMMENDED PROCESSES
The POWER WAVE 405M can be set up in a number
of configurations, some requiring optional equipment
or welding programs. Each machine is factory prepro-
grammed with multiple welding procedures, typically
including GMAW, GMAW-P, FCAW, GTAW, and
CAC-A for a variety of materials, including mild steel,
stainless steel, cored wires, and aluminum.
The POWER WAVE 405M is recommended for semi-
automatic welding, and may also be suitable for basic
hard automation applications.
• This Power Wave is not recommended for processes
other than those listed.
b-1
OPERATION
b-1
POWER WAVE 405M
SAFETY PRECAUTIONS
Read this entire section of operating instructions
before operating the machine.
ELECTRIC SHOCK can kill.
• Unless using cold feed feature, when
feeding with gun trigger, the elec-
trode and drive mechanism are
always electrically energized and
could remain energized several sec-
onds after the welding ceases.
• Do not touch electrically live parts or electrodes
with your skin or wet clothing.
• Insulate yourself from the work and ground.
• Always wear dry insulating gloves.
-----------------------------------------------------------------------
FUMES AND GASES can be dangerous.
• Keep your head out of fumes.
• Use ventilation or exhaust to remove
fumes from breathing zone.
-----------------------------------------------------------------------
WELDING SPARKS can cause fire or
explosion.
• Keep flammable material away.
• Do not weld on containers that have
held combustibles.
-----------------------------------------------------------------------
ARC RAYS can burn.
• Wear eye, ear, and body protection.
Observe additional guidelines detailed in the
beginning.
-----------------------------------------------------------------------
WARNING
Summary of Contents for POWER WAVE 405M
Page 39: ...NOTES POWER WAVE 405M ...