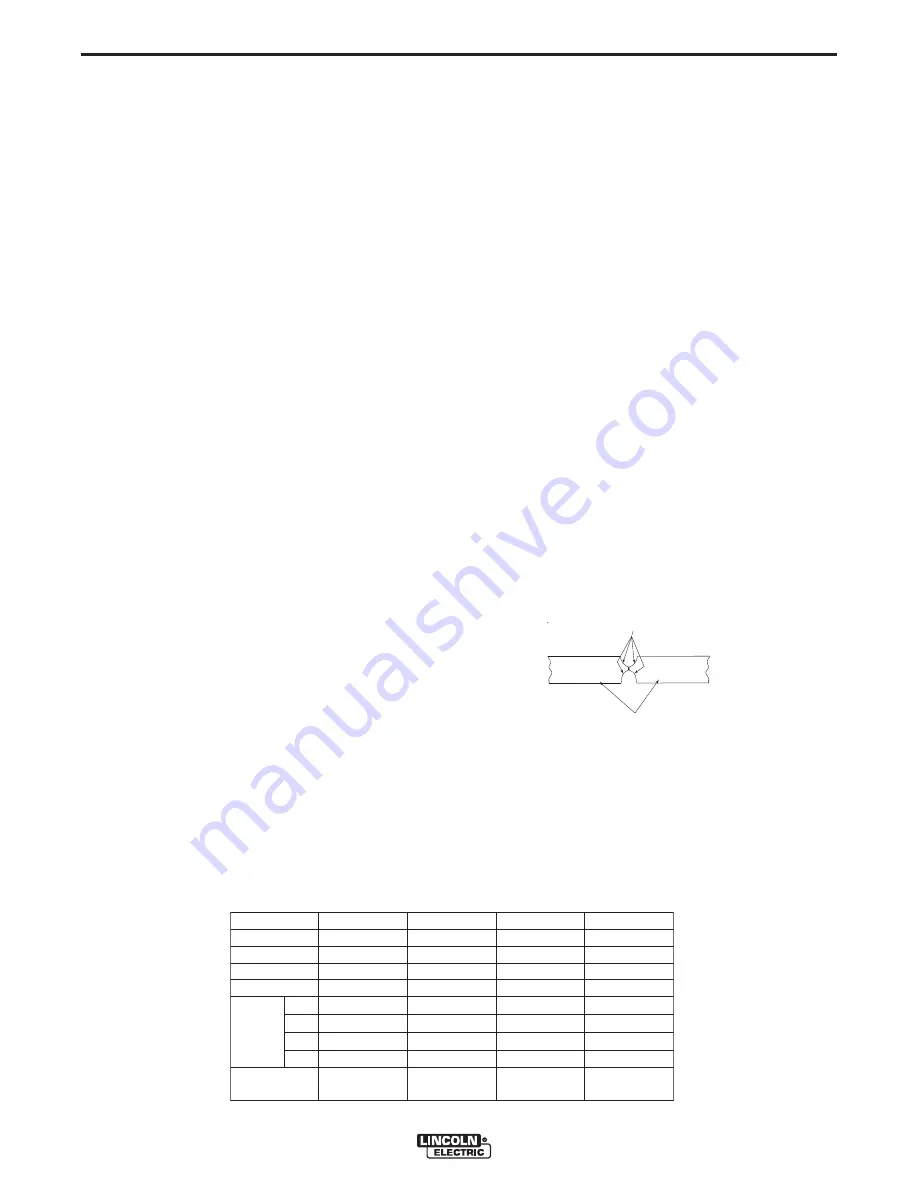
b-6
OPERATION
b-6
bENEFITS OF PULSE ON PULSE FROM
LINCOLN ELECTRIC
• Excellent appearance of the weld bead
• Improved cleaning action
• Reduced porosity
Table B.2 shows WFS and Trim settings for common
aluminum types and wire sizes when welding with
Pulse-on-Pulse. The welds made to obtain the values
in the table were fillet welds in the flat position. The
values in the table can be helpful as a starting point to
establish a welding procedure. From there, adjust-
ments need to be made to set the proper procedure
for each specific application (out-of-position, other
types of joints, etc.).
The comments on Table B.3 show values of WFS
below which it is not recommended to weld. The rea-
son is, that below these values the weld transfer will
change from a spray arc to a short-arc, which is not
advisable when welding aluminum.
TIG GTAW
The TIG mode features continuous control from 5 to
425 amps. The TIG mode can be run in either the
Touch Start TIG or Scratch start mode.
The Arc Control level selects the starting mode.
Between –10 and 0, the Touch Start TIG mode is
selected. The OCV is controlled below 10V and the
short circuit "TIG touch" current is maintained at
approximately 25 amps, independent of the preset
current. When the tungsten is lifted, an arc is initiated
and the output is regulated at the preset value. A set-
ting of 0, results in the most positive arc initiation. A
setting of -10 reduces hot start.
Between 0 and 10, the Scratch starting TIG mode is
selected. In this range, the OCV of the machine is
controlled between 50 and 70 volts.
SMAW
In
SMAW (STICK mode),
arc control adjusts the arc
force. It can be set to the lower range for a soft and
less penetrating arc characteristic (negative numeric
values) or to the higher range (positive numeric val-
ues) for a crisp and more penetrating arc. Normally,
when welding with cellulosic types of electrodes
(E6010, E7010, E6011), a higher energy arc is
required to maintain arc stability. This is usually indi-
cated when the electrode sticks to the work-piece or
when the arc pops-out during manipulative technique.
For low hydrogen types of electrodes (E7018, E8018,
E9018, etc.) a softer arc is usually desirable and the
lower end of the Arc Control suits these types of elec-
trodes. In either case the arc control is available to
increase or decrease the energy level delivered to the
arc.
ARC GOUGING
Gouging is basically removing metal to form a bevel or
groove in a piece of steel with controlled forced air
and a carbon rod.
The common procedures for Arc Gouging metal are:
• Removing poor welds from a weldment so that new
welds can be made.
• Creating a welding groove or grooves in two pieces
of steel butted together. (See Example below)
Mode 9 in the POWER WAVE 405M is specifically for
gouging. Gouging can also be done in the stick soft
and crisp modes. Setting the output of the Stick Soft
mode to 425 amps will enable the arc-gouging mode.
The actual output current will depend on the size of
carbon used. The recommended maximum size car-
bon is 5/16".
POWER WAVE 405M
STEEL BUTTED TOGTHER
WELD GROOVES CREATED BY ARC GOUGING
STEEL BUTTED TOGTHER
WELD GROOVES CREATED BY ARC GOUGING
Aluminum 4043
Aluminum 4043
Aluminum 5356
Aluminum 5356
100% Ar.
100% Ar.
100% Ar.
100% Ar.
E4043
E4043
E5356
E5356
0.035
3/64
0.035
3/64
98
99
101
102
14 ga.
250 / 1.0
200 / 1.0
230 / 1.0
225 / 1.0
10 ga.
400 /1.0
280 / 1.0
425 / 1.0
400 / 1.0
3/16
550 / 1.0
340 / 1.0
670 / 1.0
500 / 1.0
1/4
600 / 1.0
400 / 1.0
700 / 1.0
550 / 0.9
W
F
S
/
T
R
I
M
M
A
T
E
R
I
A
L
T
H
I
C
K
N
E
S
S
MATERIAL
GAS
WIRE
WIRE SIZE
WELD MODE
Not Recommended
below 200 WFS
COMMENTS
Not Recommended
below 200 WFS
Not Recommended
below 100 WFS
Not Recommended
below 200 WFS
Aluminum 4043
Aluminum 4043
Aluminum 5356
Aluminum 5356
100% Ar.
100% Ar.
100% Ar.
100% Ar.
E4043
E4043
E5356
E5356
0.035
3/64
0.035
3/64
98
99
101
102
14 ga.
250 / 1.0
200 / 1.0
230 / 1.0
225 / 1.0
10 ga.
400 /1.0
280 / 1.0
425 / 1.0
400 / 1.0
3/16
550 / 1.0
340 / 1.0
670 / 1.0
500 / 1.0
1/4
600 / 1.0
400 / 1.0
700 / 1.0
550 / 0.9
W
F
S
/
T
R
IM
M
A
T
E
R
IA
L
T
H
IC
K
N
E
S
S
MATERIAL
GAS
WIRE
WIRE SIZE
WELD MODE
Not Recommended
below 200 WFS
COMMENTS
Not Recommended
below 200 WFS
Not Recommended
below 100 WFS
Not Recommended
below 200 WFS
WELDING PROCEDURES FOR PULSE-ON-PULSE (TAbLE b.2)
Summary of Contents for POWER WAVE 405M
Page 39: ...NOTES POWER WAVE 405M ...