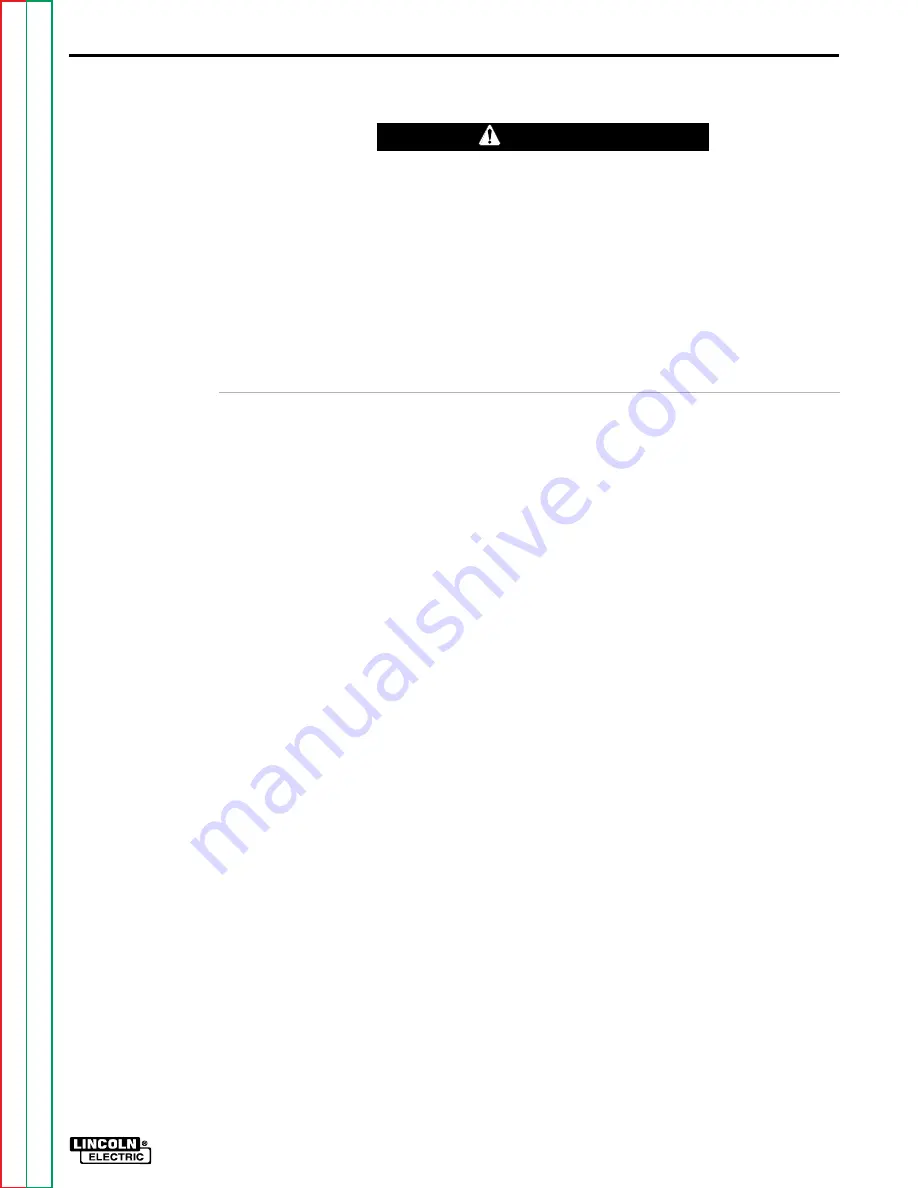
Retur
n to Section TOC
Retur
n to Section TOC
Retur
n to Section TOC
Retur
n to Section TOC
Retur
n to Master TOC
Retur
n to Master TOC
Retur
n to Master TOC
Retur
n to Master TOC
TROUBLESHOOTING & REPAIR
PRO-CUT 60
F-24
MAIN TRANSFORMER TEST
TEST DESCRIPTION
This test will identify any problems or faults in the Main Transformer’s primary and
secondary windings. These tests require that the machine be connected to the input
power supply and turned ON.
MATERIALS NEEDED
Volt/Ohmmeter (Multimeter)
PRO-CUT 60 Wiring Diagrams
Service and repair should be performed only by Lincoln Electric factory trained per-
sonnel. Unauthorized repairs performed on this equipment could result in danger to
the technician or the machine operator and will invalidate your factory warranty. For
your safety and to avoid electrical shock, please observe all safety notes and pre-
cautions detailed throughout this manual.
If for any reason you do not understand the test procedures or are unable to perform
the tests/repairs safely, contact the Lincoln Electric service department for technical
troubleshooting assistance before you proceed.
Call (216) 383-2531 or (800) 833-9353 (WELD).
WARNING