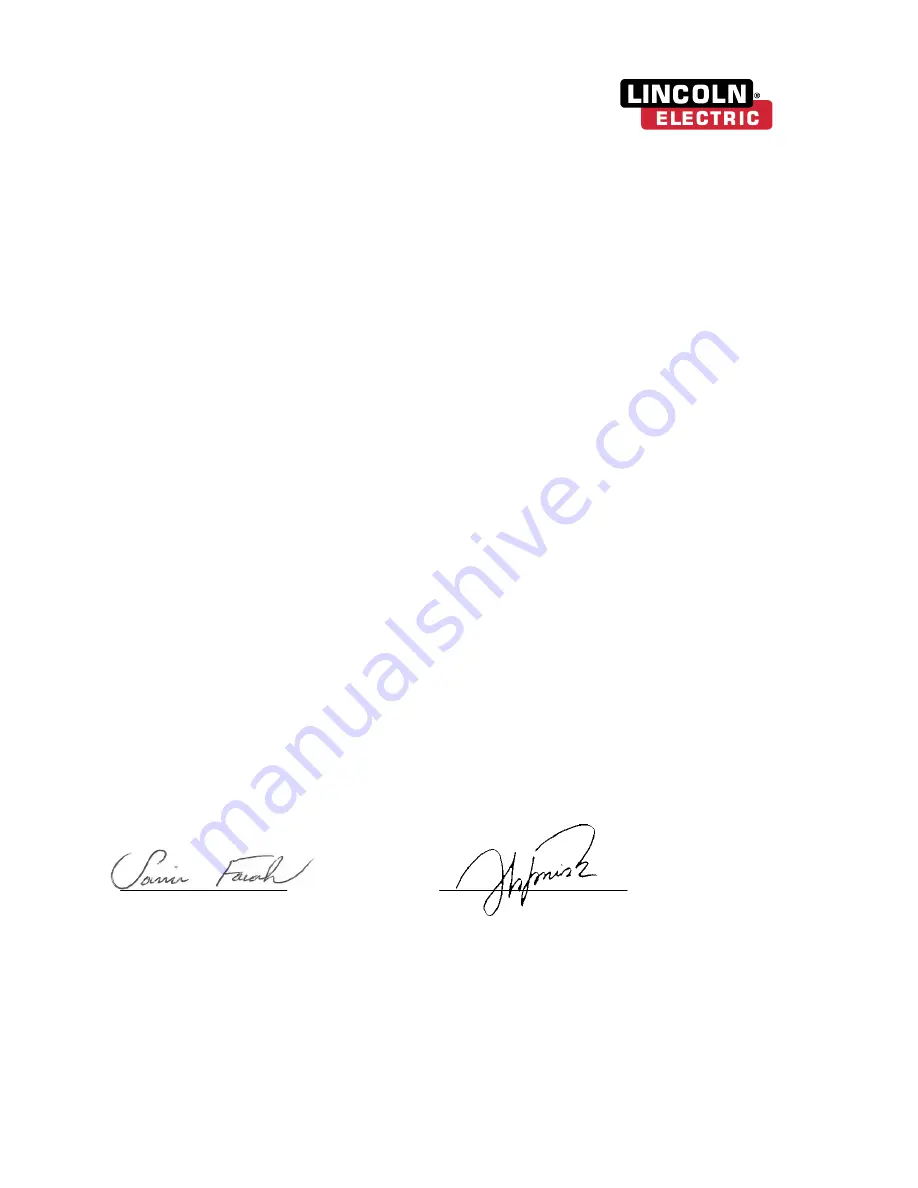
English
English
II
THE LINCOLN ELECTRIC COMPANY
EC DECLARATION OF CONFORMITY
Manufacturer
and
technical
documentation
holder:
The
Lincoln
Electric
Company
22801
St.
Clair
Ave.
Cleveland
Ohio
44117
‐
1199
USA
EC
Company:
Lincoln
Electric
Europe
S.L.
c/o
Balmes,
89
‐
80
2a
08008
Barcelona
SPAIN
Hereby
declare
that
welding
equipment:
Product
number:
Ranger
305D
with
CE
marking
K2279
(may
contain
prefixes
and
suffixes)
Is
in
conformity
with
Council
Directives
and
amendments:
Machinery
Directive
2006/42/EC;
Low
Voltage
Directive
2014/35/EU
Electromagnetic
Compatibility
(EMC)
Directive
2014/30/EU
Noise
emission
in
the
environment
by
equipment
for
use
outdoors
2000/14/EC.
EN
60974
‐
1:2012,
Safety
requirements
for
arc
welding
equipment,
power
sources;
EN
60974
‐
10:2014,
Arc
Welding
Equipment
‐
Part
10:
Electromagnetic
compatibility
(EMC)
requirements;
EN
ISO
3744:2010,
Acoustics
–
Determination
of
sound
power
levels
of
noise
sources
using
sound
pressure
…
reflecting
plane;
EN
60204
‐
1:2006,
Safety
of
machinery
–
Electrical
equipment
of
machines,
Part
1:
General
requirements;
EN
12100:2010,
Safety
of
machinery
–
General
principles
for
design
risk
assessment
and
risk
reduction.
Notified
body
(for
2000/14/EC
Conformity):
LNE
– Number:
0071
ZA
de
Trappes
‐
Élancourt
29,
avenue
Roger
Hennequin
78197
TRAPPES
Cedex
Guaranteed
sound
power
level:
LWA
97
dB
(net
power
Pel
=
7.5
kW)
Measured
sound
power
level:
LWA
96
dB
(net
power
Pel
=
7.5 kW)
CE
marking
affixed
in
‘15
Samir
Farah,
Manufacturer
Compliance
Engineering
Manager
Jacek
Stefaniak,
European
Community
Representative
European
Product
Manager
Equipment
7
September
2017
8
September
2017
MCD40e