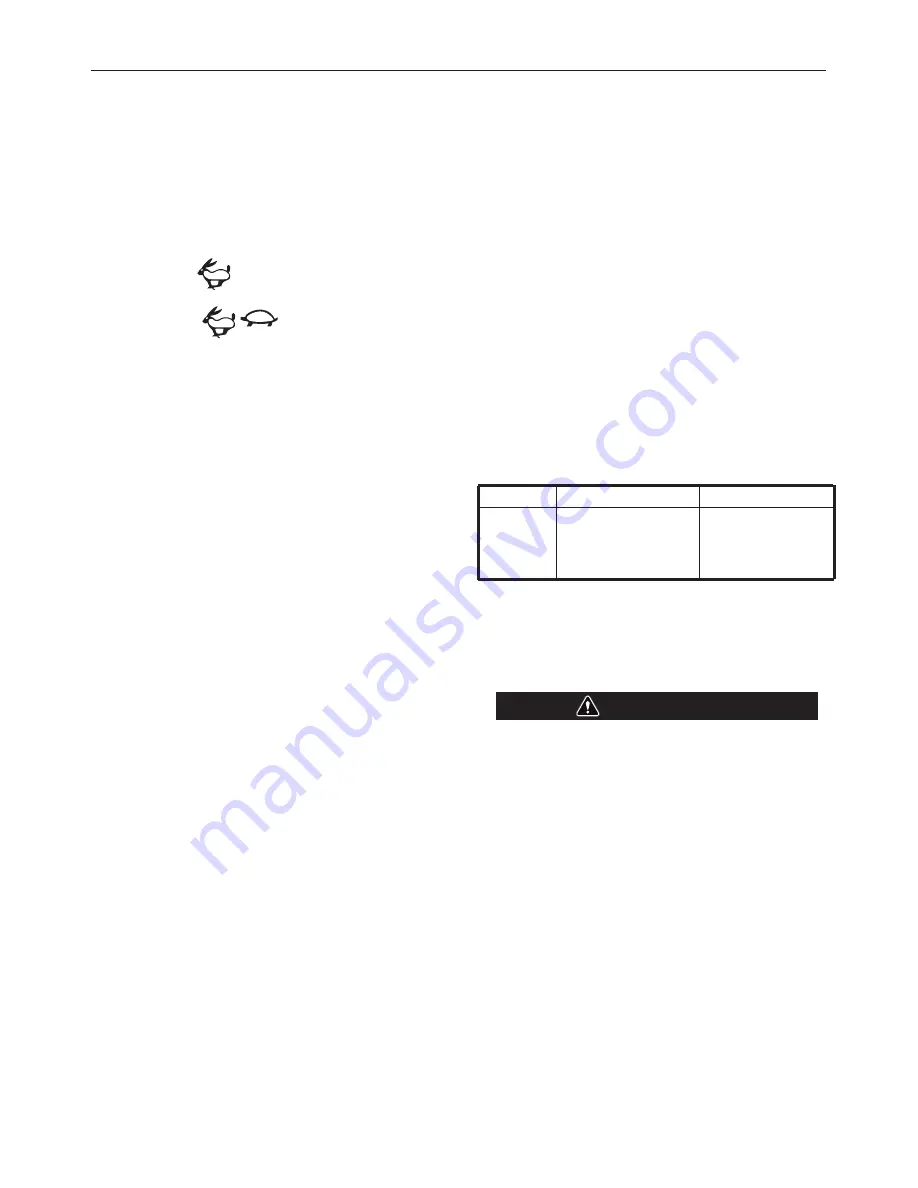
B-2
OPERATION
ENGINE CONTROLS
IGNITION SWITCH
When placed in the “ON” position, this switch energizes the fuel
solenoid. When placed in the “OFF” position, the flow of fuel to the
injection pump is stopped to shut down the engine.
“IDLER” SWITCH
The idler switch has two positions, “HIGH” and “AUTO”.
When in “HIGH” ( ) position, the engine will run continuously
at high idle.
When in “AUTO” ( / ) idle position, the idler operates as
follows:
a. Welding
When the electrode touches the work, the welding arc is initiat-
ed and the engine accelerates to full speed.
After welding ceases (and no auxiliary power is being drawn),
the engine will return to low idle after approximately 10 to 14
seconds.
b. Auxiliary Power
With the engine running at low idle and auxiliary power for
lights or tools is drawn (approximately 100-150 watts or
greater) from the receptacles, the engine will accelerate to high
speed. If no power is being drawn from the receptacles ( and
not welding) for 10-14 seconds, the idler reduces the engine
speed to low idle.
ENGINE TEMPERATURE GAUGE
Displays the coolant temperature in the engine block.
ENGINE OIL PRESSURE GAUGE
Displays the oil pressure to the engine. When the engine starts
running, watch for the oil pressure to build up. If no pressure
shows within 30 seconds, stop the engine and consult the engine
instruction manual.
BATTERY CHARGING AMMETER
Displays the current going from the charging alternator into the
batteries. It is normal for charging current to be high (above 15
amps) after starting or when the batteries are ‘low’ on charge.
ENGINE HOUR METER
The engine hour meter records the total running time on the
engine in hours. It can be used to keep a record of maintenance
on the engine and or welder.
ENGINE PROTECTION SYSTEM
The engine protection system shuts down the engine under high
coolant temperature or low engine oil pressure conditions by
allowing the fuel solenoid valve to close.
WELDER CONTROLS
POLARITY SWITCH
Turn the Arc Polarity switch to electrode positive or electrode neg-
ative as required for each particular application.
CONTROL OF WELDING CURRENT
Purpose of Controls
The continuous “Current Control” is the main current adjuster. The
“Job Selector” is both a fine current adjuster and the continuous
Open Circuit Voltage adjuster. Open Circuit Voltage (OCV) controls
the arc characteristics.
“Job Selector”
The “Job Selector” dial is divided into four colored sections pro-
viding OCV ranges as follows:
Color
Title
OCV Range
White
Large Electrodes
High OCV
Black
Normal Welding
Medium OCV
Red
Overhead & Vertical
Low OCV
Grey
Special Applications
Extra-Low OCV
The “Job Selector” is usually set in the black range because it
provides a soft “Buttering “ arc desired for most welding. Some
operators prefer to set the “Job Selector” in the red range for a
snappy “Digging” arc when welding vertical up or overhead.
“Current Control”
Do not adjust the “Current Control” while welding because
this can damage the control.
------------------------------------------------------------------
The “Current Control” dial is calibrated in amperes on three sepa-
rate colored dials corresponding to the white, black and red
ranges of the “Job Selector” dial. For example: when the “Job
Selector” is set on the black range, the approximate welding cur-
rent is indicated on the black scale of the “Current Control” dial.
SAE-400™
CAUTION