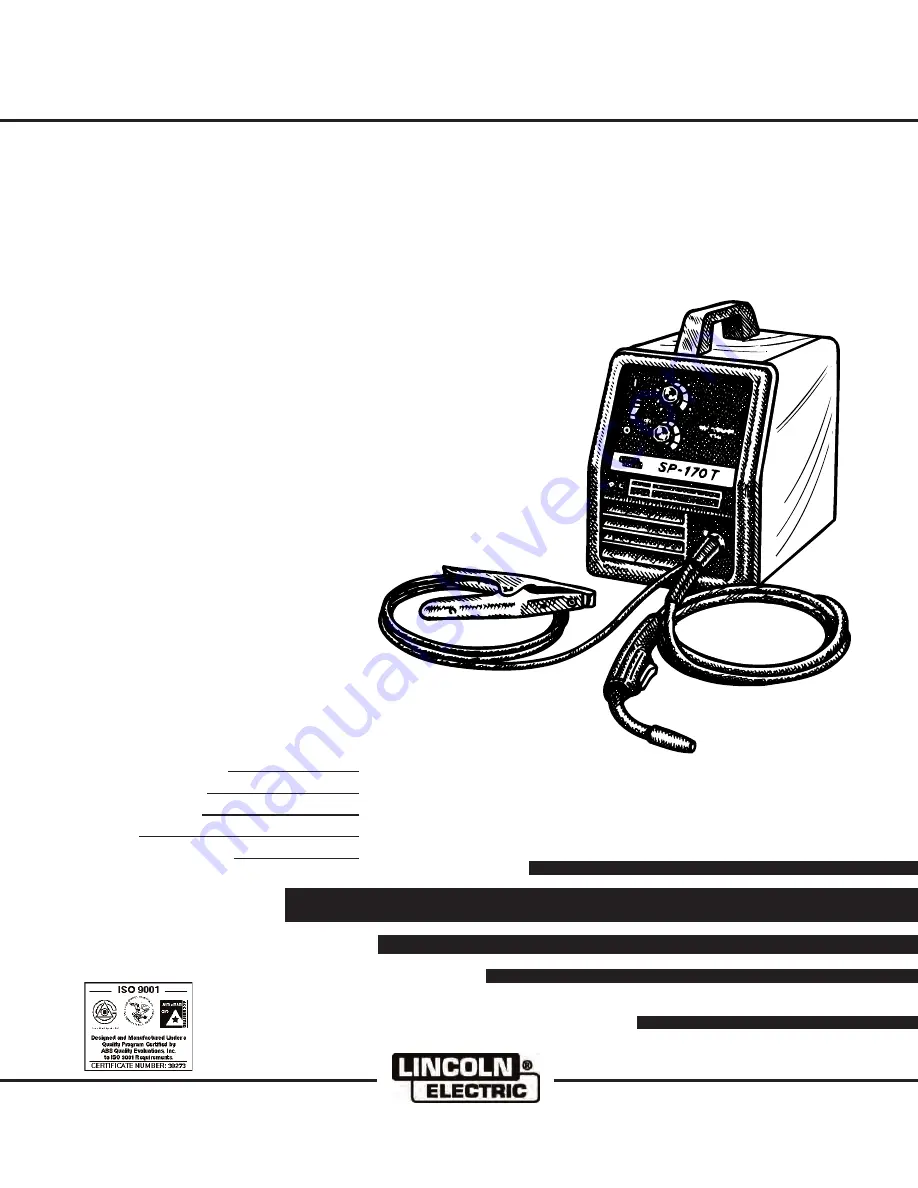
SP-170T
OPERATOR’S MANUAL
IM537-D
March, 2001
Safety Depends on You
Lincoln arc welding and cutting
equipment is designed and built
with safety in mind. However,
your overall safety can be
increased by proper installation ...
and thoughtful operation on your
part.
DO NOT INSTALL, OPER-
ATE OR REPAIR THIS EQUIP-
MENT WITHOUT READING
THIS MANUAL AND THE SAFE-
TY PRECAUTIONS CONTAINED
THROUGHOUT.
And, most
importantly, think before you act
and be careful.
For use with machine Code Numbers
10023 thru 10026,10134,10162,
10163,10261,10264,10272,10482,10691,10692,10741,10842 and 10848
• Sales and Service through Subsidiaries and Distributors Worldwide •
Cleveland, Ohio 44117-1199 U.S.A. TEL: 216.481.8100 FAX: 216.486.1751 WEB SITE: www.lincolnelectric.com
• World's Leader in Welding and Cutting Products •
Date of Purchase:
Serial Number:
Code Number:
Model:
Where Purchased:
Summary of Contents for SP-170T
Page 31: ...B 18 SP 170T B 18 APPLICATION CHART ...
Page 44: ...SP 170T NOTES ...