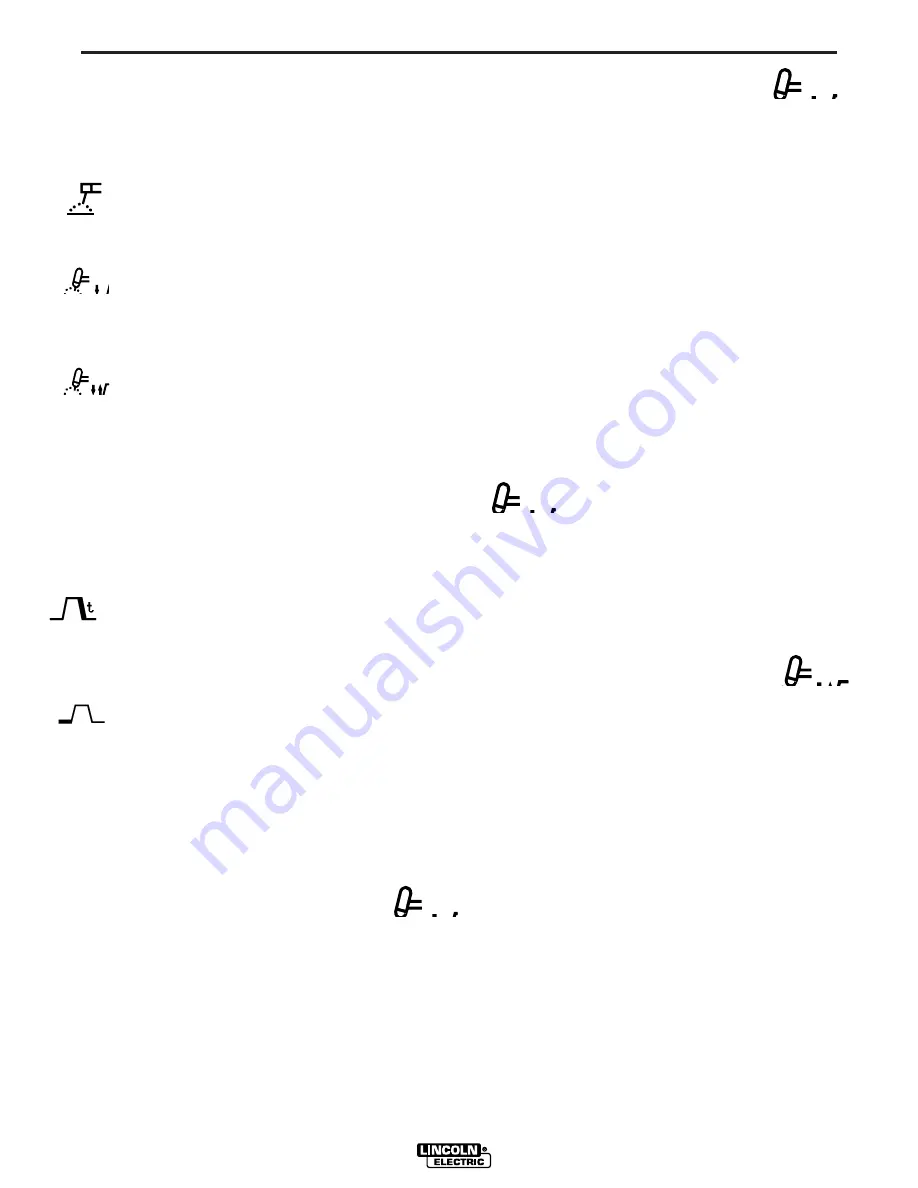
8
OPERATION
8
7. MODE SWITCH - A three position toggle switch
used to select the welding mode. Refer to WELD-
ING IN THE STICK MODE, and WELDING IN THE
TIG MODE(2-STEP AND 4-STEP) later in this sec-
tion for information on how the machine functions in
each of these modes.
STICK: This mode is used for the stick electrode
(SMAW) welding process. In this position the only
active control is the output current control. The out-
put terminals are continuously energized.
2-STEP TIG: This mode is used for the TIG
(GTAW) welding process. An Arc Start switch or
Amptrol must be used to weld. The Down slope
Time and Start/Crater Current controls have no
effect in this mode.
4-STEP TIG: This mode is used for the TIG
(GTAW) welding process. An Arc Start switch or
Amptrol must be used. All controls are active in
this mode.
8. CURRENT CONTROL - This control is active in both
TIG and Stick modes. In Stick mode the current con-
trol sets the welding current. In TIG mode this con-
trol sets the maximum current. The Amptrol
tm
will
adjust the welding current from the machine mini-
mum to this maximum setting.
9. DOWN SLOPE TIME - This control is active in the 4-
STEP TIG mode only.
It is used to set the amount
of time the output takes to go from the preset level to
the Crater current level. The adjustable range is
approximately 0.5 to 10 seconds.
10. START/CRATER CURRENT - This control is active
in the 4-STEP TIG mode only. It sets the Start and
Crater currents of the weld as a percentage of the
peak current set with the Current control knob. If
the Start current set is not above the minimum
starting current of the machine or electrode the
weld will not start. If this occurs increase the per-
centage and try again.
OPERATING STEPS
WELDING IN TIG MODE (2 STEP)
In 2-STEP mode an Arc Start switch or Amptrol must be
used. The switch or Amptrol is pressed to start the weld.
(Step 1) Output continues at the level set with the Current
control until the switch or Amptrol is released. (Step 2)
1. If connecting a Lincoln LA-9 or LA-17 TIG torch simply
connect the Twistmate plug to the receptacle located
on the front of the machine. See INPUT SUPPLY
CONNECTIONS if another TIG torch is used.
2. Set the MODE switch to
“
2 STEP TIG
”
.
3. Set the Polarity Switch to DC- for weld-
ing steel or stainless steel; or to AC for welding alu-
minum.
4. Connect an Arc Start Switch or Amptrol to the
Remote Control Connector.
5. Turn on the cylinder gas valve and adjust the flow
regulator to obtain desired flow.
6. Turn the power switch to
“
ON - I
”
. NOTE: There will
be a 15 second gas flow when the power is turned
on.
7. Set the Current Control on the control panel to the
maximum desired amps.
8. Depress the Arc Start Switch or amptrol to energize
the torch and establish an an arc with the work
piece.
NOTE: When the MODE switch is set to
“
2 STEP TIG
”
,
depressing the remote control will start a 0.5
second gas pre-flow before energizing the
TIG torch. When the remote control is released the TIG
torch is de-energized and gas flow will continue for a 15
second post flow. When the polarity switch is set to DC, the
TIG Arc Starter will turn on and off automatically to start
and stabilize the arc. In AC the TIG Arc Starter will turn on
with the output and remain on continuously until the remote
control is released.
WELDING IN TIG MODE (4-STEP)
In 4-STEP mode an Arc Start switch or Amptrol must
be used. The switch or Amptrol is pressed and then
released to start the weld cycle. Pressing and releas-
ing the switch or Amptrol a second time ends the weld
cycle. This eliminates the need to continuously hold
down the switch or Amptrol during the weld. The
process works as follows:
(STEP 1) First Press: Initiates a 0.5 second preflow
of shielding gas and starts the weld at the Start cur-
rent level set with the Start/Crater Current control.
(Note: The Start current is determined by setting a
peak current with the output control knob and then
setting a percentage of that current with the
Start/Crater Current control. IMPORTANT! THE
WELD WILL NOT START IF THE START CURRENT
IS SET BELOW THE MACHINES MINIMUM WELD-
ING CURRENT. (Approx 10 Amps))
(STEP 2) First Release: The output ramps up to the
preset level in 0.5 seconds.
SQUARE WAVE TIG 175
A
Summary of Contents for SQUARE WAVE IM607
Page 29: ...NOTES SQUARE WAVE TIG 175 ...
Page 30: ...NOTES SQUARE WAVE TIG 175 ...