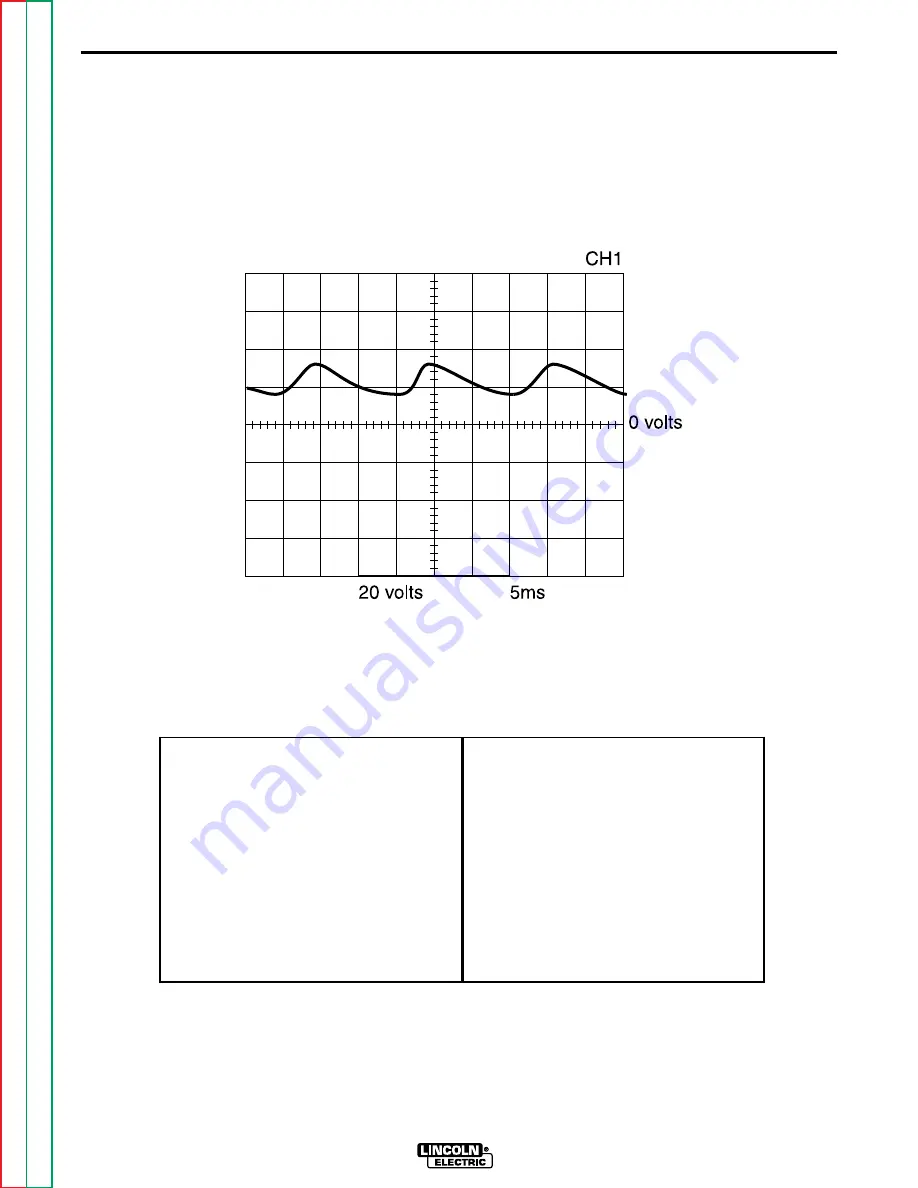
Retur
n to Section TOC
Retur
n to Section TOC
Retur
n to Section TOC
Retur
n to Section TOC
Retur
n to Master TOC
Retur
n to Master TOC
Retur
n to Master TOC
Retur
n to Master TOC
F-24
TROUBLESHOOTING & REPAIR
F-24
WIRE-MATIC 250
This is NOT a typical DC output voltage
waveform. One output SCR is not function-
ing. Note the increased ripple content. One
SCR gate was disconnected to simulate an
open or non-functioning output SCR. Each
vertical division represents 20 volts and
each horizontal division represents 5 mil-
liseconds in time. The machine was loaded
with a resistance grid bank.
Note: Scope probes connected at machine
output terminals: (+) probe to electrode, (-)
probe to work.
Volts/Div . . . . . . . . . . . . . . . . .20 V/Div.
Horizontal Sweep . . . . . . . . . .5 ms/Div.
Coupling . . . . . . . . . . . . . . . . . . . . .DC.
Trigger . . . . . . . . . . . . . . . . . . .Internal.
SCOPE SETTINGS
MACHINE LOADED TO 220 AMPS AT 22 VDC
ABNORMAL OUTPUT VOLTAGE WAVEFORM - MACHINE LOADED
ONE OUTPUT SCR NOT FUNCTIONING