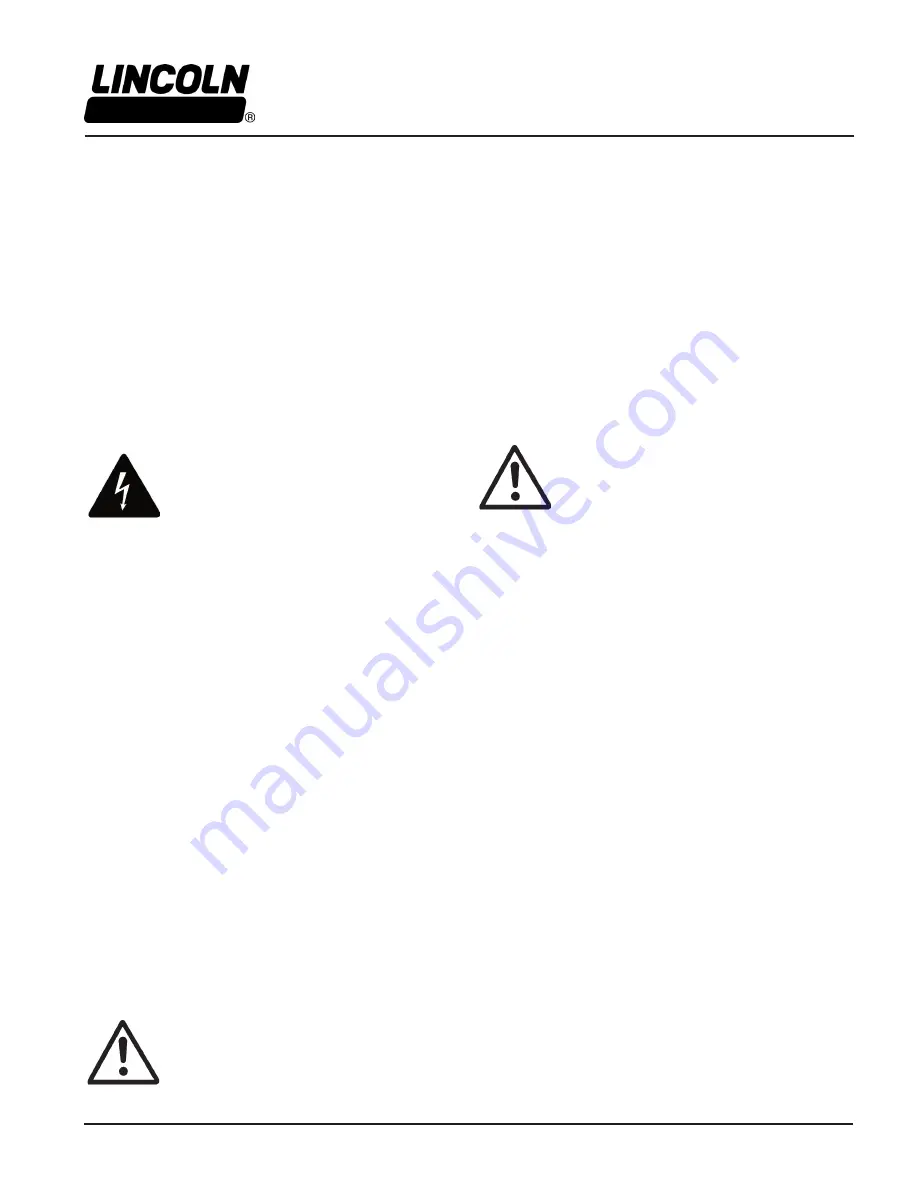
Page Number - 7
CENTRO-MATIC
®
4.1A-68020-E05
Form 403569
5. Remove nut (36) from the top of the reservoir cap (38) using a
1-3/8 wrench.
6. Remove reservoir cap (38) from top of reservoir.
7. Slide the reservoir tube off the pump over the center post.
8. Remove gasket (41) if necessary.
9. Reassemble in reverse of the above procedure.
10. Tighten nut (36) to 10 to 15 ft.-lbs. [13.5 to 20.3 n-m].
Grease Reservoir Service
(See Illustration 11)
(Note: Replacement of the reservoir tube does not require removal of
the pump assembly from the mounting surface.)
1. Turn off the air supply to the pump assembly.
2. Turn off the power supply to the pump unit.
3. Remove lubricant from the lubricant reservoir. Grease pumps may
be emptied by carefully removing the filler fitting (52) from the unit
with a 7/8 wrench. (Depending on how full the reservoir is, the
grease may flow out of the reservoir very rapidly.)
Warning!
Failure to
remove all lubricant from reservoir could result in a
high spring force from the follower spring (47) and/or
a rapid discharge of grease when nut (36) is loosened
or removed.
4. Clean off reservoir tube and area around reservoir to prevent
getting dirt into lubrication system.
5. Remove nut (36) from top of reservoir cap (38) using a 1-3/8
wrench. Carefully hold reservoir cap against any residual spring
force while removing nut (36).
6. Remove reservoir cap (38) from top of reservoir.
7. Holding the follower down with the follower spring (47), carefully
work the reservoir tube (40) off of the follower, leaving the follower
and spring in place on the pump assembly.
8. Remove the follower spring (47).
9. Remove follower assembly by sliding up to the threads in the center
rod (42), and then threading the follower assembly counter-clock-
wise over the threaded portion of the center rod. Do not force or
pull the follower off of the center rod or damage will result to the
o- ring (46) inside of follower bushing (35).
10. Remove gasket (41) if necessary.
11. Disassemble the follower assembly by removing retaining ring
(48), using external ring pliers, from bushing (35). Washers (49)
and follower packing (50) can now be removed from bushing (35).
Remove o-ring (46) from the internal groove in the inner hole of the
bushing (35); use a pointed tool, such as a pick.
12. Reassemble in reverse of the above procedure with the following
hints:
13. When reinstalling the follower assembly onto the center rod (42)
lubricate the center tube liberally with grease. Lubricate the o-ring
(46) and the inside of bushing (35) with grease. Thread, turning
clockwise, the follower assembly down over the center rod
treads. Do not force or drive with hammer, or o-ring damage will
result in leakage of lubricant around follower. Slide the follower
assembly down to the bottom of the center rod (42).
14. When installing the reservoir tube, lubricate the follower packing
lips (50) and the inside of the reservoir tube (40) with grease.
The reservoir tube will have two vent holes in the side wall of the
tube close to one end of the tube. The reservoir tube (40) must
be placed on the pump with the vent holes near the upper side of
the pump assembly. Place the reservoir tube down over the
follower packing (50), working the packing lips up into the
reservoir tube with your fingers until the entire follower assembly
is inside the reservoir.
15. Tighten nut (36) to 10 to 15 ft.-lbs. [13.5 to 20.3 n-m].
4. Disconnect the wire connections from the wire terminals on the
timer/controller board (32). Note where each wire is connected on
the terminal strips.
5. Remove the timer/controller board (32) by removing the four Phillips
head screws (33).
6. Reassembly is the reverse of the above procedure.
7. Be sure that all wires are connected to the correct locations on the
terminal strips.
8. Connect the ribbon cable plug from the keypad (34) to the mating
plug on the timer/controller board (32). The plug should be plugged
into the timer/controller board (32) so that the ribbon cable has no twist
in it; it must be parallel to the face of the enclosure when the keypad
(34) is installed.
9. When reinstalling the keypad (34), be sure that the ribbon cable is
gently folded into the enclosure behind the keypad (34), and not
pinched between the keypad (34) and enclosure.
Solenoid Valve Replacement
(See Illustration 8)
Warning!
Electrical shock hazard. Disconnect and
lock out all power to the pump unit before removing
the keypad of the timer compartment.
(Note: Replacement of the solenoid valve does not
require removal of the pump assembly from the mounting surface.)
1. Turn off air supply to pump assembly.
2. Turn off the power supply to the pump unit.
3. See Timer/Controller Replacement, above, to remove the keypad (34)
and timer/controller board (32).
4. Remove the enclosure (30) by removing two Phillips head screws
(29) from the side of the enclosure.
5. As the enclosure (30) is removed from the assembly, gently pull the
solenoid and green ground wires through the grommet (31) in the
enclosure back towards the solenoid valve (25).
6. Remove the solenoid valve (25) using a 3/32 Allen wrench to remove
the two cap screws (27) holding it to the bottom of the cylinder head
(23). Do not lose the gasket (24) that is placed between the valve
and cylinder head (23).
7. When replacing the solenoid valve, make sure the solenoid valve is
the correct part number and voltage as the valve to be replaced.
8. Reassemble in reverse of the above procedure. Take care in pulling
the solenoid and green ground wires through the grommet (31).
Oil Reservoir Service
(See Illustration 9)
(Note: Replacement of the reservoir tube does not require removal of the
pump assembly from the mounting surface).
1. Turn off the air supply to the pump assembly.
2. Turn off the power supply to the pump unit.
3. Remove lubricant from the lubricant reservoir. Oil pump reservoirs
may be drained by removing the drain plug (51) from the right side of
the pump unit with a 9/16 wrench.
4. Clean off reservoir tube and area around reservoir to prevent
getting dirt into the lubrication system.
Warning!
Failure to drain reservoir will result in lubricant
leakage out of reservoir when the nut (36) securing the
reservoir in place is removed.