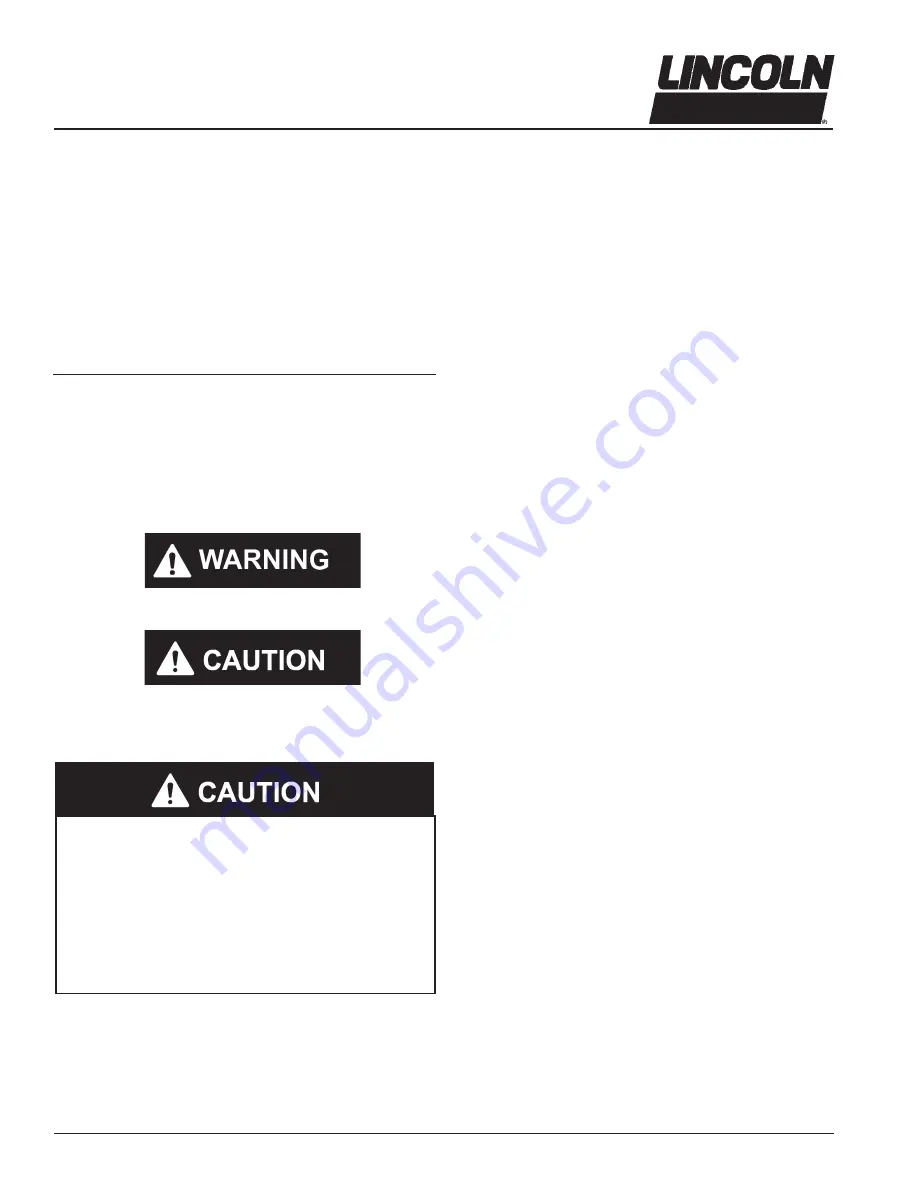
Page Number - 2
FlowMaster
®
Rotary Driven Electric Pump
Form 404059
Description
A newer version of the FlowMaster pump was introduced in July of
2008. These units incorporate the following improvements:
* Bushing & plunger seals used along with elastomer cup seals for
longer life and better high temperature operation.
* A crankcase oil dipstick
* Hardened and ground section on the reciprocating tube for longer
life and better crankcase oil control.
* Hardened and ground pivot pin bushings with a tighter fit into the
pivot pin anchor.
* Improved pivot pin fastener with deeper Allen hex socket.
All of the improved parts can be used with the older model pumps,
so the upgraded parts and subassemblies will now be supplied to re-
pair older model pumps. Please see the “Maintenance and Repair”
section for a list of the new repair kits and their proper application.
85851 - 400 pound pump, 360RPM maximum, 5,000 psi
max. pressure rating
85850 - 120 pound pump, 360 RPM maximum, 5,000 psi
maxpressure rating
General Description
The Lincoln Industrial rotary A/C electric pump uses a 50 Hz, 3
Phase 380-420 VAC dual voltage motor and a single stage planetary
gear drive. Grease output is proportional to the pump RPM. The
pump is primarily designed for centralized lubrication systems such
as the Single Line Parallel, Single Line Progressive and Two Line
systems.
The pump is driven by the rotary motion of the electric motor. Rotary
motion is converted to reciprocating motion through an eccentric
crank mechanism. The reciprocating action causes the pump
cylinder to move up and down. The unit is a positive displacement
double-acting pump as grease output occurs during both the up and
down stroke.
During the down stroke, the pump cylinder is extended into the
grease. Through the combination of shovel action and vacuum
generated in the pump cylinder chamber, the grease is forced into
the pump cylinder. Simultaneously, grease is discharged through the
outlet of the pump. The volume of grease during intake is twice the
amount of grease output during one cycle. During the upstroke, the
inlet check closes, and one half of the grease taken in during the pre-
vious stroke is transferred through the outlet check and discharged
to the outlet port. Typical output of the pump is shown on page 3.
center nearest you for repair or adjustments other than mainte-
nance specified in this manual.
Annual inspection by the factory authorized warranty and service
center nearest you is recommended.
A list of factory authorized warranty and service centers is available
upon request.
Damaged Pumps
Any pump that appears to be damaged in any way, is badly worn
or operates abnormally, shall be removed from use until repairs are
made. Contact the factory authorized warranty and service center
nearest to you for repairs.
Table of Contents
Page
Safety …..….……………................................................................2
Description....................................................................................2
Appropriate Use................................................................3
Pump Performance and Specifications..............................3
Installing the Pump.....................................................................3
Operation.....................................................................................4
Crankcase Oil...............................................................................4
Pump Dimensions.............................................................5
Troubleshooting.........................................................................6
Required Tools...............................................................................7
Maintenance and Repair...........................................................7
Repair Parts List.......................................................................23
Safety
Read and carefully observe these operating instructions before
unpacking and operating the pump! The pump must be oper-
ated, maintained and repaired exclusively by persons familiar
with the operating instructions. Local safety regulations regard-
ing installation, operation and maintenance must be followed.
Operate this pump only after safety instructions and this service
manual are fully understood.
Indicates a potentially hazardous situation which, if not avoided,
could result in death or serious injury.
Indicates a potentially hazardous situation which, if not avoided,
may result in minor or moderate injury.
Safety Instructions
Inspection
If overpressurizing of the equipment is believed to have oc-
curred, contact the factory authorized warranty and service
center nearest you for inspection of the pump.
Specialized equipment and knowledge is required for repair of
this pump. Contact the factory authorized warranty and service
This equipment generates very high grease pressure.
Extreme caution should be used when operating this equip-
ment as material leaks from loose or ruptured
components can inject fluid through the skin and into the
body causing serious bodily injury. Adequate protection is
recommended to prevent splashing of material onto the skin
or into the eyes.
If any fluid appears to penetrate the skin, get emergency
medical care immediately. Do not treat as a simple cut. Tell
attending physician exactly what fluid was injected.