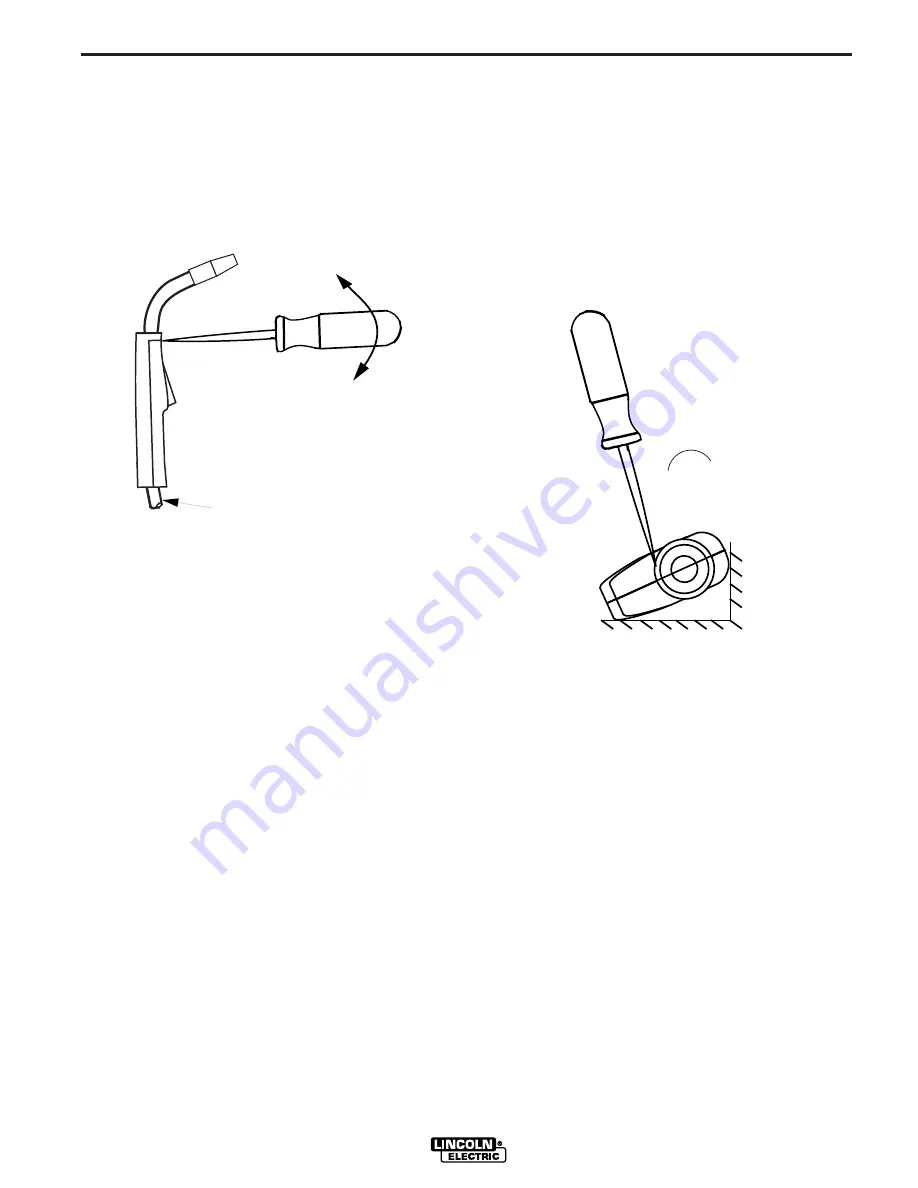
D-5
D-5
MAINTENANCE
SP 170-I
GUN HANDLE PARTS (Lincoln Electric)
The gun handle consists of two halves that are held
together with four screws. To open up the gun handle
assembly, remove the four screws and pry down the
trigger handle half with a screwdriver. See Figure D.3.
FIGURE D.3
Screwdriver
Cable
GUN HANDLE PARTS (Magnum 100L)
The gun handle consists of two halves that are held
together with a collar on each end. To open up the
handle, turn the collars approximately 60 degrees
counter-clockwise until the collar reaches a stop. Then
pull the collar off the gun handle. If the collars are diffi-
cult to turn, position the gun handle against a corner,
place a screwdriver against the tab on the collar and
give the screwdriver a sharp blow to turn the collar
past an internal locking rib. See Figure D-4.
FIGURE D.4
➣
Counter-clockwise
Summary of Contents for SP 170-I
Page 6: ...v SAFETY v ...
Page 7: ...vi SAFETY vi ...
Page 35: ...NOTES SP 170 I ...
Page 36: ...NOTES SP 170 I ...