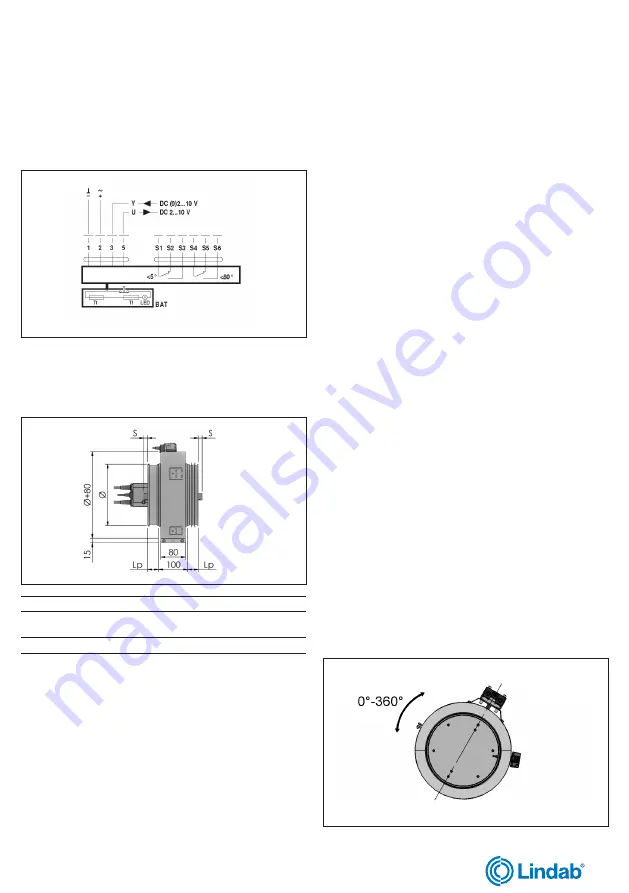
5
/14
Electrical wiring for Belimo BFL24-SR-T modulating motorized version
24V AC/DC power supply
/- Negative (DC) or neutral (AC) black wire
~/+ Positive (DC) or phase (AC) red wire
3 Positioning signal Y
5 Positioning feedback U (max 0,5mA)
Microswitches position contacts
S1 Common closed damper microswitch
S2 Normally closed, closed damper microswitch
S3 Normally opened, closed damper microswitch
S4 Common open damper microswitch
S5 Normally closed, open damper microswitch
S6 Normally opened, open damper microswitch
Tf Thermal fuse
TECHNICAL DATA
The sizes shown are in mm.
Dimension
Ø
mm
100
125
160
200
250
315
400
S blade
exposition
mm
0
0
0
30
40
80
157
Lp
mm
40
40
40
40
60
60
80
Lp
Overlap length between fire damper and duct
MAINTENANCE AND
INSPEC TIONS
Fire dampers and control mechanisms do not require routine main-
tenance.
Extraordinary maintenance (repairs) and periodic inspection opera-
tions are the responsibility of the ventilation system operator.
It is recommended to keep enough space (about 200mm) for using
or replacing the control mechanism or for maintenance. Also provide
the necessary space to remove the ventilation duct from the damper
whenever necessary.
It is recommended to provide inspection hatches on both sides of
the ducts connected to the fire damper.
The implementation of a periodic inspection plan allows to guaran-
tee the efficiency and functionality of the fire dampers for the fire
safety of the building.
Periodic inspection and cleaning
Periodic inspection shall be performed in accordance with the re-
quirements of the law or by the building regulations or other local
regulations.
In the absence of specific regulations (or to their complement), in ac-
cordance with point 8.3 of the EN 1560 standard, it is recommended
to carry out the following control activities at intervals of no more
than 12 months:
• Check the servomotor electrical wiring for damage (where appli-
cable);
• Check end-switch wiring for damage (where applicable);
• Check damper cleanliness and clean where necessary;
• Check the condition of blades and seals, rectify and report where
necessary;
• Check the correct opening and closing of the fire damper by ma-
nual operation according to the instructions in the technical ma-
nual of the fire damper;
• Check the opening and closing operation of the damper control-
led by the fire alarm system (if present);
• Check the operation of the end switches in open and closed state,
adjust and report if necessary;
• Confirm that the damper fulfils its function as part of the control
system (where necessary);
• Check that the damper is left in its normal operating position, whi-
ch usually corresponds to the open position.
Repair
For safety reasons, repair activities involving fire-fighting componen-
ts must be carried out only by qualified personnel.
Only original spare parts supplied by the fire damper manufacturer
must be used.
A functional test must be performed after each repair.
.
At the end of the inspection, cleaning or repair operations, check that
the fire damper is in the normal operating position.
Keep records of all inspections, repair activities, any problems en-
countered and their resolution.
This practice, even when not mandatory, is very useful in practice.
Disposal
Disposal in case of destruction must be carried out in accordance
with national legislation. For electrical and electronic parts also refer
to EU Directive 2011/65.
INSTALLATION
The sizes shown are in mm.
It is recommended to perform a functional test before Installation to
exclude possible damage during transport and another test imme-
diately after installation to exclude accidental damage to the product
and interference with mounting components.
Blade rotation axis positioning
The fire damper can be installed with the blade axis positioned verti-
cally or horizontally or tilted at any angle.
rev 20-12
5
We reserve the right to make changes without prior notice