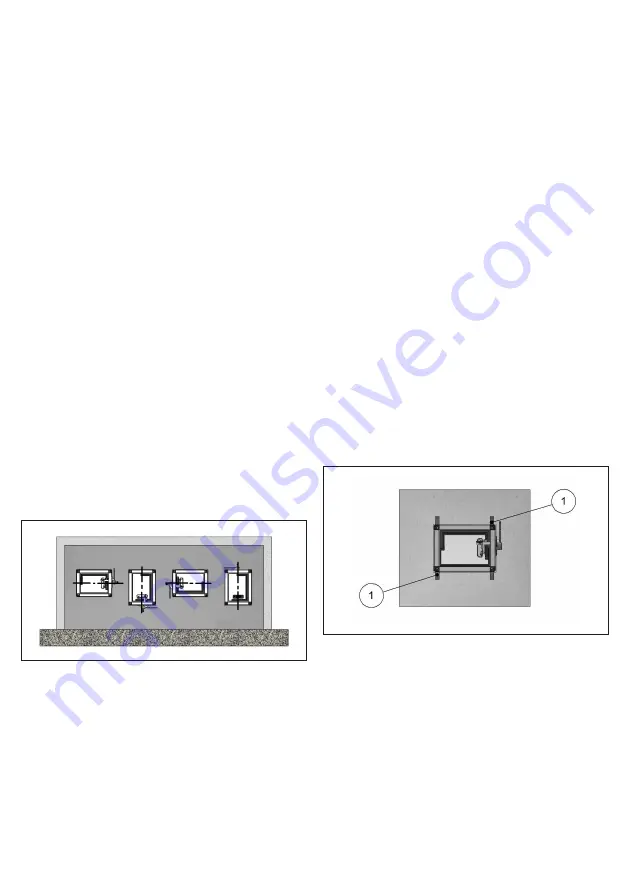
8
/17
The implementation of a periodic inspection plan allows to guaran-
tee the efficiency and functionality of the fire dampers for the fire
safety of the building.
Periodic inspection and cleaning
Periodic inspection shall be performed in accordance with the re-
quirements of the law or by the building regulations or other local
regulations.
In the absence of specific regulations (or to their complement), in ac-
cordance with point 8.3 of the EN 1560 standard, it is recommended
to carry out the following control activities at intervals of no more
than 6 months:
• If the damper is connected to a remote control or command sys-
tem (eg BMS or alarm or fire detection), that responds correctly to
commands by performing at least one opening and closing test
and verifying the correct movement of the blade and the correct
functioning of the microswitches (limit switches).
• If the damper is not connected to a remote control or command
system, manually execute an opening and closing test and check
the correct movement of the blade and the correct functioning of
the microswitches (limit switches) if present.
Together with the control activities, it is recommended to visually
verify the absence of corrosion, the integrity of the electrical wiring
and the sealing of the construction support.
Damper cleaning is included in the ordinary maintenance activities
of the ventilation ducts.
Fire dampers can be cleaned with a dry or wet cloth.
In the case of resistant dirt, it is possible to use normal household
detergents.
If prescribed for the type of building, it is possible to use disinfectant
detergents.
The use of detergents or mechanical abrasive cleaning systems is not
permitted.
These indications comply with the standards EN 15650 annex D and
EN 15423 annex C.
Repair
For safety reasons, repair activities involving fire-fighting compo-
nents must be carried out only by qualified personnel.
Only original spare parts supplied by the fire damper manufacturer
must be used.
A functional test must be performed after each repair.
.
At the end of the inspection, cleaning or repair operations, check that
the fire damper is in the normal operating position.
Keep records of all inspections, repair activities, any problems en-
countered and their resolution.
This practice, even when not mandatory, is very useful in practice.
Disposal
Disposal in case of destruction must be carried out in accordance
with national legislation. For electrical and electronic parts also refer
to EU Directive 2011/65.
INSTALLATION
The sizes shown are in mm.
It is recommended to perform a functional test before Installation to
exclude possible damage during transport and another test immedi-
ately after installation to exclude accidental damage to the product
and interference with mounting components.
Blade rotation axis positioning
The fire damper can be installed both with the blade axis positioned
vertically or horizontally.
Positioning brackets before fixing
1. WKGY100 fixing brackets (accessory to order separately, one size valid for all
fire dampers kind)
WKGY100 fixing brackets are obligatory for intallations within plaster-
board walls and suggested for walls with 100 mm thickness.
They are not usable for installations with Fire Batt (Weichschott) seal-
ing.
Installation of flexible connectors in order to balance out the
ventilation ducts expansion
CAUTION: Refer anyway to law and national standardization.
Flexible connectors compensate any duct thermal expansion and
wall bending in case of fire.
Flexible connectors are used to limit fire damper stresses due to ex-
ternal forces in case of fire and to preserve fire resistance class.
In general it is always appropriate the use of flexible connectors for
the followings installations:
– light walls;
– Plasterboard and rock wool or Fire Batt (Weichschott) sealing;
– Applique fixing system.