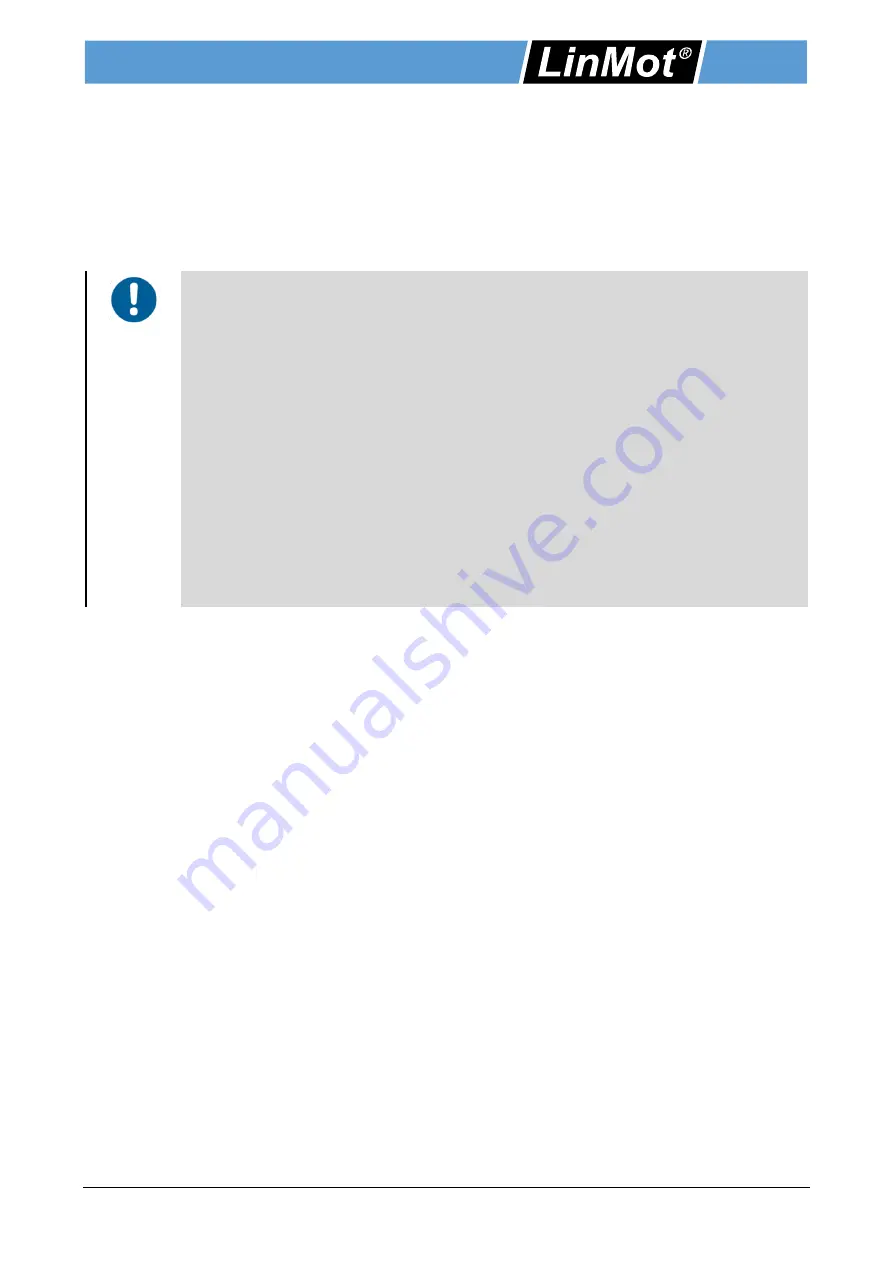
Installation Guide Linear Rotary Motors
ENG
NTI AG / LinMot
PR02-88
Page 9 / 34
process data (e.g. tightening torque). This makes it easy to implement high-precision, reproducible and
recordable closing & assembly processes in accordance with Industry 4.0 requirements.
Torque sensors are based on the measuring principle of strain gauges and transmit the measuring signal
and the supply voltage without contact. This enables low-wear and maintenance-free continuous operation.
With this option, a suitable, galvanically isolated measuring amplifier is automatically integrated in the linear
rotary motor and provides a measuring signal of +-10 VDC suitable for the LinMot drive.
Factory calibrations of integrated torque sensors are always carried out in the installed state. This has the
advantage that the influences of the mechanics and the linear rotary motor are included.
•
The torque measuring shaft is used to measure static as well as dynamic torques. The
sensor can measure both right-hand and left-hand loads. The measured variable is
suitable for control, regulation and monitoring tasks.
•
Torque peaks exceeding the permissible overload (see specifications in the PR02 data
sheet) can lead to destruction of the torque measuring shaft. Where such peaks cannot
be safely excluded, they must be mitigated.
•
When changing between right and left load, the torque sensor may show a small
hysteresis. This may cause the sensor to exceed the specified accuracy at the
changeover point.
•
Simultaneously turning and measuring the force can falsify the measurement (e.g. due
to increased friction of the linear rotary shaft).
•
The operating temperature range of the sensors is 5 - 45 °C. Above or below the limits,
there is a measurement error which influences the measurement results. It is
recommended to set the offset to zero before each measurement.
•
The max. operating range is between 0 - 80 °C.
•
For continuously precise measuring results, it is recommended to calibrate the torque
measuring shaft annually according to section 8.3.
•
Recalibration is also strongly recommended after improper handling of the force
sensors (e.g. impacts on the linear rotary shaft or large overloads).