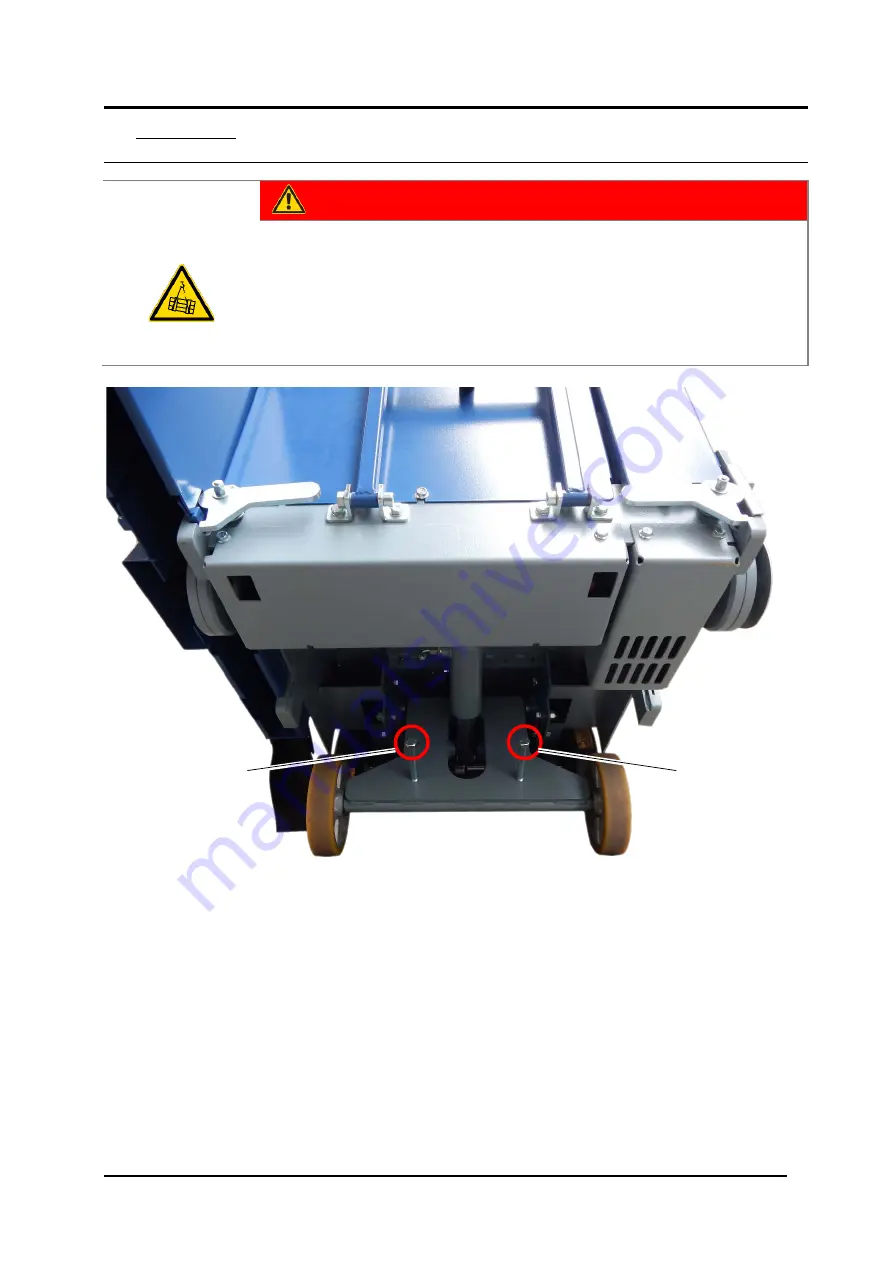
40/56
6.3.
Set the depth stop
DANGER
Suspended loads
Injury from falling parts.
Do not stand under suspended machines or parts.
Only use undamaged lifting gear and loading equipment with sufficient lifting capacity and
length.
The centre of mass of the machine is off-centre.
The depth stop for the immersion depth of the saw blade can be adjusted on the underside of the Floor saw
via the two hexagonal screws (Pos. 1).
1
1
Summary of Contents for Compactcut 900
Page 2: ...2 56 ...
Page 7: ...7 56 Notes ...
Page 51: ...51 56 9 CIRCUIT DIAGRAM ...
Page 52: ...52 56 ...
Page 53: ...53 56 ...
Page 54: ...54 56 ...
Page 55: ...55 56 ...
Page 56: ...56 56 ...