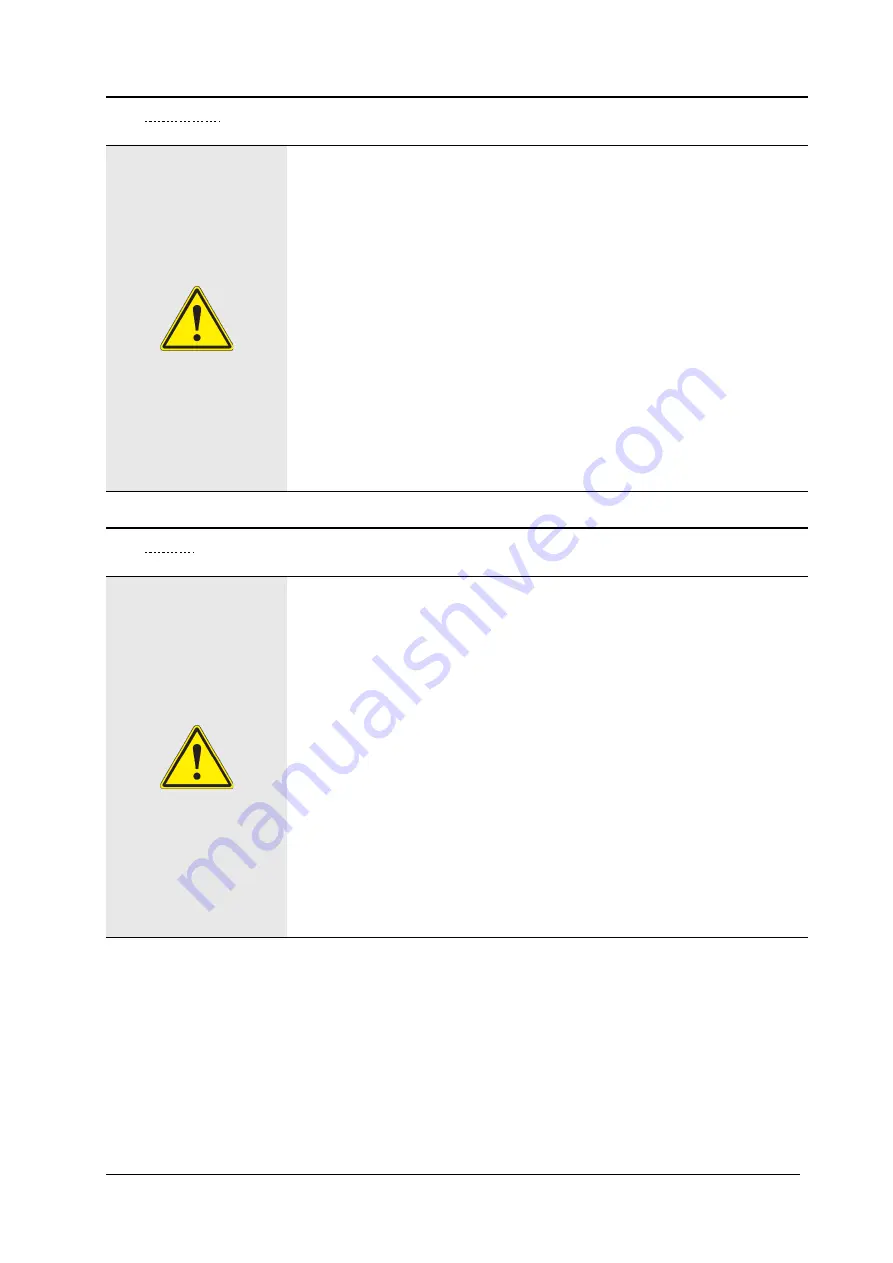
15/107
2.4.2.
Commissioning
When fitting the saw blade, protect your hands from sharp edges.
Make sure the aggregate surface has the required load-bearing capacity. All obstacles must be
removed from the cutting area and good lighting must be provided.
Visual check of the entire floor saw for any damage and defects. Separate check of the protective
devices.
Supply water for saw blade cooling.
Smoking is prohibited when refueling the internal combustion engine.
Particular care should be taken during refueling. Engine parts that became hot during operation pose a
fire hazard.
Fuel must only be stored in approved containers.
No rotating tool, whose maximum speed is lower than the rated speed of the machine, must be used.
Defective or broken tools must be replaced immediately.
2.4.3.
Operation
Do not use any unsafe method of working.
Take measures to ensure that the floor saw is only used if it is safe and in functional condition.
Check the floor saw at least once per shift for external signs of damage and defects. Notify the
responsible place/person immediately when changes have occurred (including the operational
behavior). If necessary, shut down the machine immediately and secure it to prevent it being switched
on again.
If the floor saw malfunctions, shut it down immediately and secure it. Have faults corrected
immediately. Electrical installation work may only be carried out by trained electrical personnel.
Only use suitable and checked tools.
To protect against acceleration, the depth adjustment of the saw blade must be moved slowly and in
steps into the ground. Any contact with the rotating tool must be avoided. Keep a safety distance of
1.5m to the saw blade.
Cutting without the blade guard or drive belt cover is prohibited.
The operator must be protected from rotating parts.
Summary of Contents for MULTICUT 605 SG
Page 2: ...2 107 ...
Page 8: ...8 107 Notes ...
Page 72: ...72 107 11 CIRCUIT DIAGRAM ...
Page 73: ...73 107 ...
Page 74: ...74 107 ...
Page 75: ...75 107 ...
Page 76: ...76 107 12 APPENDIX A ERROR CODE LISTE HATZ ...
Page 77: ...77 107 ...
Page 78: ...78 107 ...
Page 79: ...79 107 ...
Page 80: ...80 107 ...
Page 81: ...81 107 ...
Page 82: ...82 107 ...
Page 83: ...83 107 ...
Page 84: ...84 107 ...
Page 85: ...85 107 ...
Page 86: ...86 107 ...
Page 87: ...87 107 ...
Page 88: ...88 107 ...
Page 89: ...89 107 ...
Page 90: ...90 107 ...
Page 91: ...91 107 ...
Page 92: ...92 107 ...
Page 93: ...93 107 ...
Page 94: ...94 107 ...
Page 95: ...95 107 ...
Page 96: ...96 107 ...
Page 97: ...97 107 ...
Page 98: ...98 107 ...
Page 99: ...99 107 ...
Page 100: ...100 107 ...
Page 101: ...101 107 ...
Page 102: ...102 107 ...
Page 103: ...103 107 ...
Page 104: ...104 107 ...
Page 105: ...105 107 ...
Page 106: ...106 107 ...
Page 107: ...107 107 ...