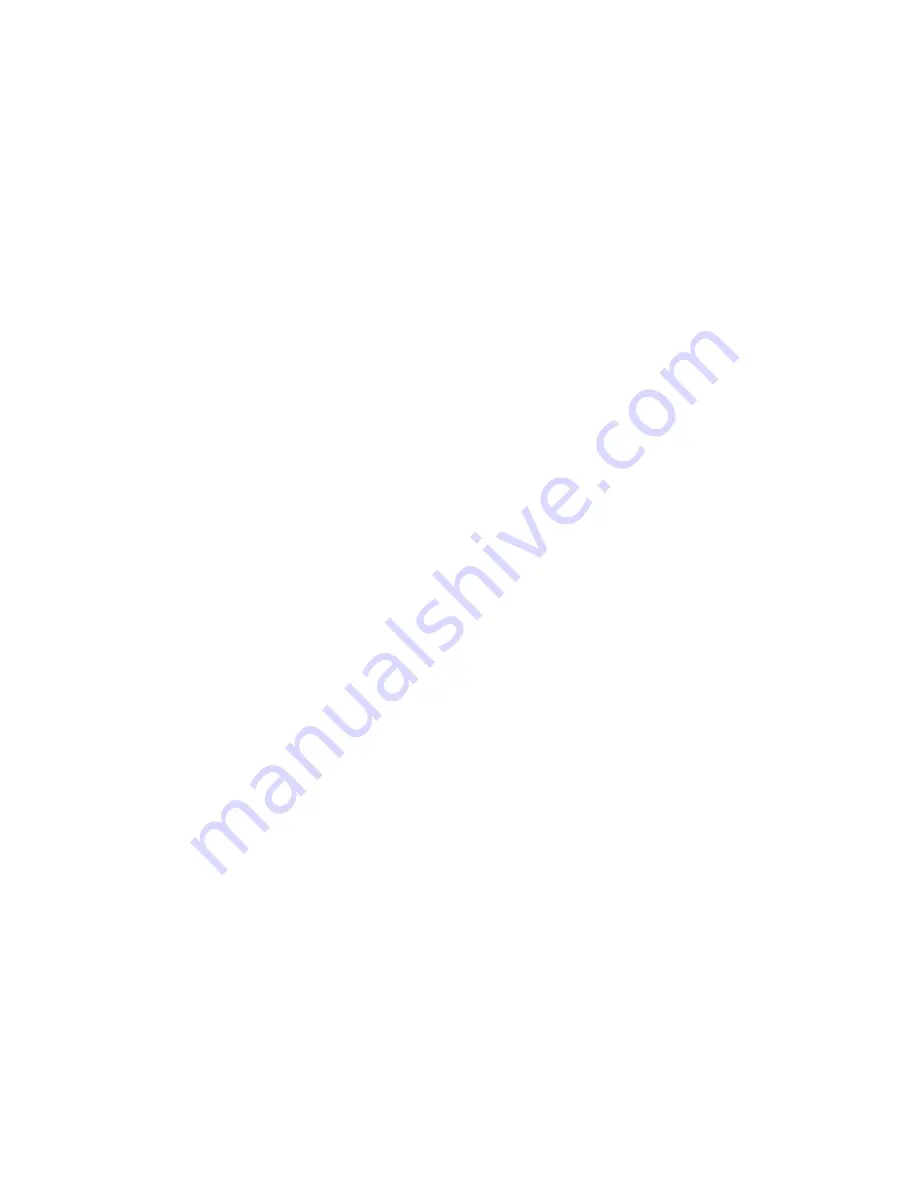
35
Cleaning
The maintenance you perform most often is cleaning. Keeping swarf (chips,
shavings, and debris) off of wearing surfaces is the most important thing you
can do to prolong the life of your mini lathe.
Use a 1” paintbrush to remove swarf from the ways as you work.
Clean the lead screw before each use.
Clean swarf from the lathe, from top down after each use.
Motor Brushes
The motor brushes can be replaced without removing the motor. Follow these
steps.
1.
Unplug the power cord.
2.
Unscrew the motor brush retainer from the front side of the motor through
the hole in the frame of the lathe.
3.
Replace the front motor brush.
4.
Replace the front motor brush retainer.
5.
Remove the motor cover from the back of the lathe.
6.
Unscrew the motor brush retainer from the back of the motor.
7.
Replace the back motor brush.
8.
Replace the back motor brush retainer.
9.
Replace the motor cover.