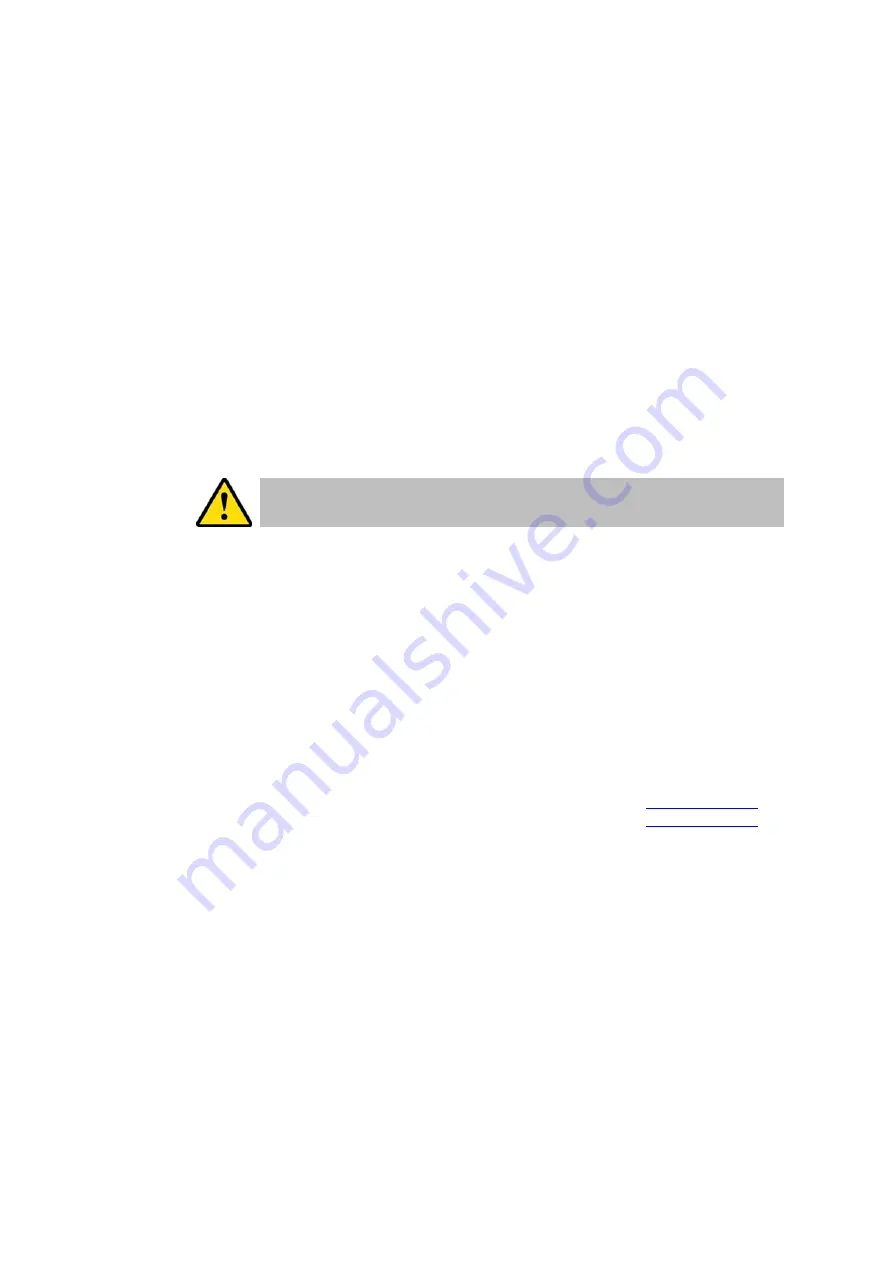
4
1.0
INTRODUCTION
The Lochinvar EcoKnight™ range is a floor standing direct gas fired circulating type condensing water heater.
The equipment comprises of stainless steel radial burner assembly and heat exchanger that permits fully
condensing operation. EcoKnight™ water heaters must be used in conjunction with an appropriately sized
LST direct storage vessel (available from Lochinvar Limited as an ancillary option)
The burner is initiated by a full electronic ignition sequence control that incorporates a spark ignition and a
flame rectification device for supervision of the flame.
The output from the water heater is regulated by a variable speed combustion fan and gas/air ratio controls to
maintain the correct combustion at all levels of modulation. This configuration allows modulation down to 20%
of the rated output.
For the correct operation of the water heater, it is essential that a suitably sized pump is utilised to maintain a
constant water flow rate through the heat exchanger. A suitable shunt pump is supplied as an ancillary with
the water heater.
This equipment is intended for use on Group H Natural Gas (2
nd
Family) and LPG propane (3
rd
Family). The
information relating to propane firing is to be found in Section 18.0 LPG FUEL.
This equipment MUST NOT use gas other than that for which it has been designed and
adjusted.
This equipment must be installed by a competent person, registered with a H.S.E. approved body. All
installations must conform to the relevant Gas Safety and Building Regulations. Health & Safety requirements
must also be taken into account when installing any equipment. Failure to comply with the above may lead to
prosecution.
If the equipment is to be connected to an unvented (pressurised) system, care must be taken to ensure all
extra safety requirements are satisfied should a high or low-pressure condition occur in the system.
The equipment is designed for direct connection to a flue system.
Ancillary Options:
Primary Circulating Pump (EKW46CE & EKW61CE)
LM900151A
Primary Circulating Pump (EKW86CE)
LM900141A
LST Direct Storage Vessel (From 297 litre to 2820 litre)
Unvented/Boosted Water System Kits
De-stratification Pump Kit
WH9
Condensate Neutralisation Kit
KIT2000
Flue System Components
See Section 10.0
Summary of Contents for ECOKNIGHT EKW116CE
Page 28: ...28 Max distance between brackets ...
Page 29: ...29 ...
Page 30: ...30 ...
Page 34: ...34 ...
Page 35: ...35 ...
Page 55: ...55 15 8 WIRING DIAGRAM 15 8 1 WIRING DIAGRAM ...
Page 56: ...56 15 9 LADDER DIAGRAM 15 9 1 LADDER DIAGRAM ...
Page 87: ...87 ...
Page 88: ...88 ...