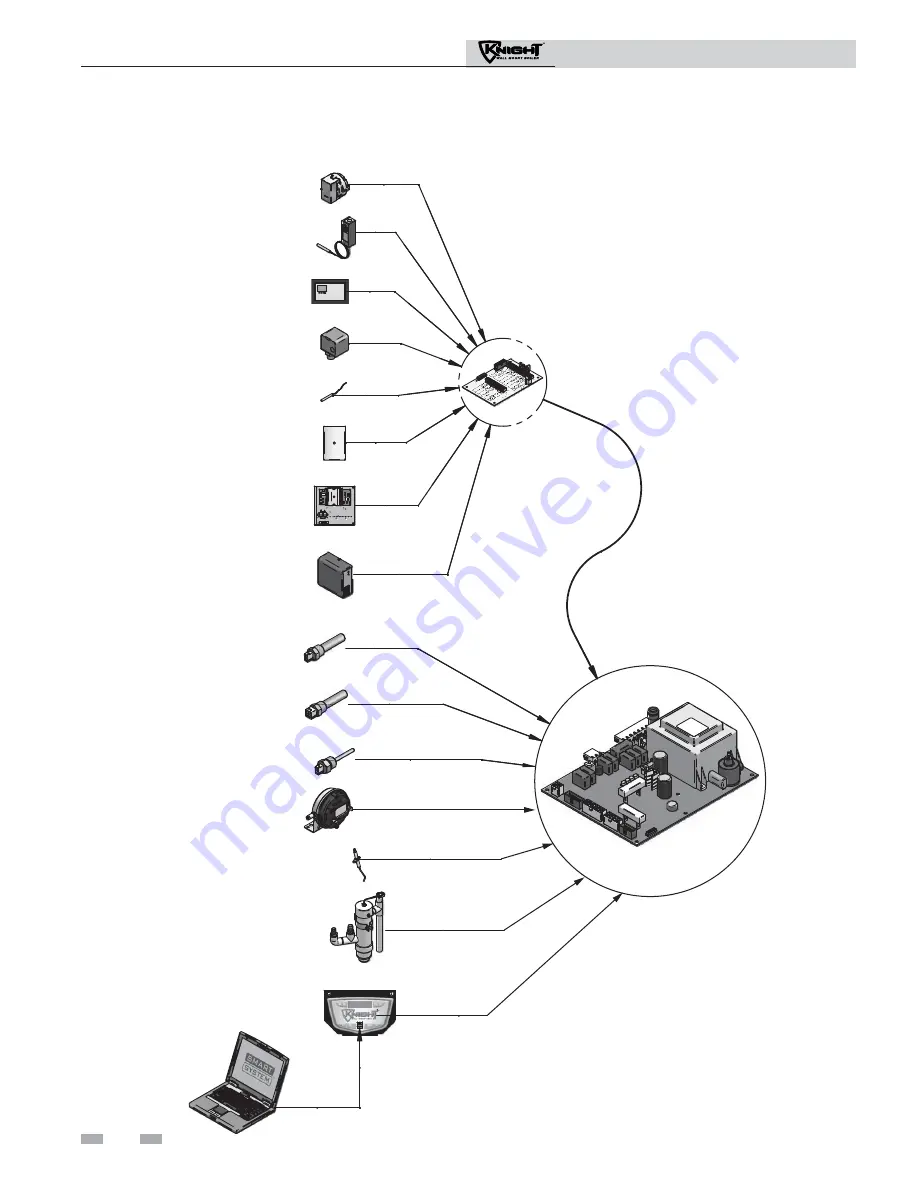
1
Service
8
Service Manual
1
Service
GAS PRESSURE SWITCH
DHW THERMOSTAT
ROOM THERMOSTAT /
ZONE CONTROL
FLOW SWITCH
SYSTEM SENSOR
OUTDOOR SENSOR
SEQUENCER / BUILDING
MANAGMENT SYSTEM
LOW VOLTAGE
CONNECTION
BOARD
INLET TEMPERATURE
SENSOR
OUTLET TEMPERATURE /
HIGH LIMIT SENSOR
FLUE GAS SENSOR
FLAME SENSOR
LOW WATER CUTOFF
BLOCKED DRAIN SWITCH
DISPLAY PANEL
PC INTERFACE
SMART CONTROL
MODULE
AIR PRESSURE SWITCH
Control inputs