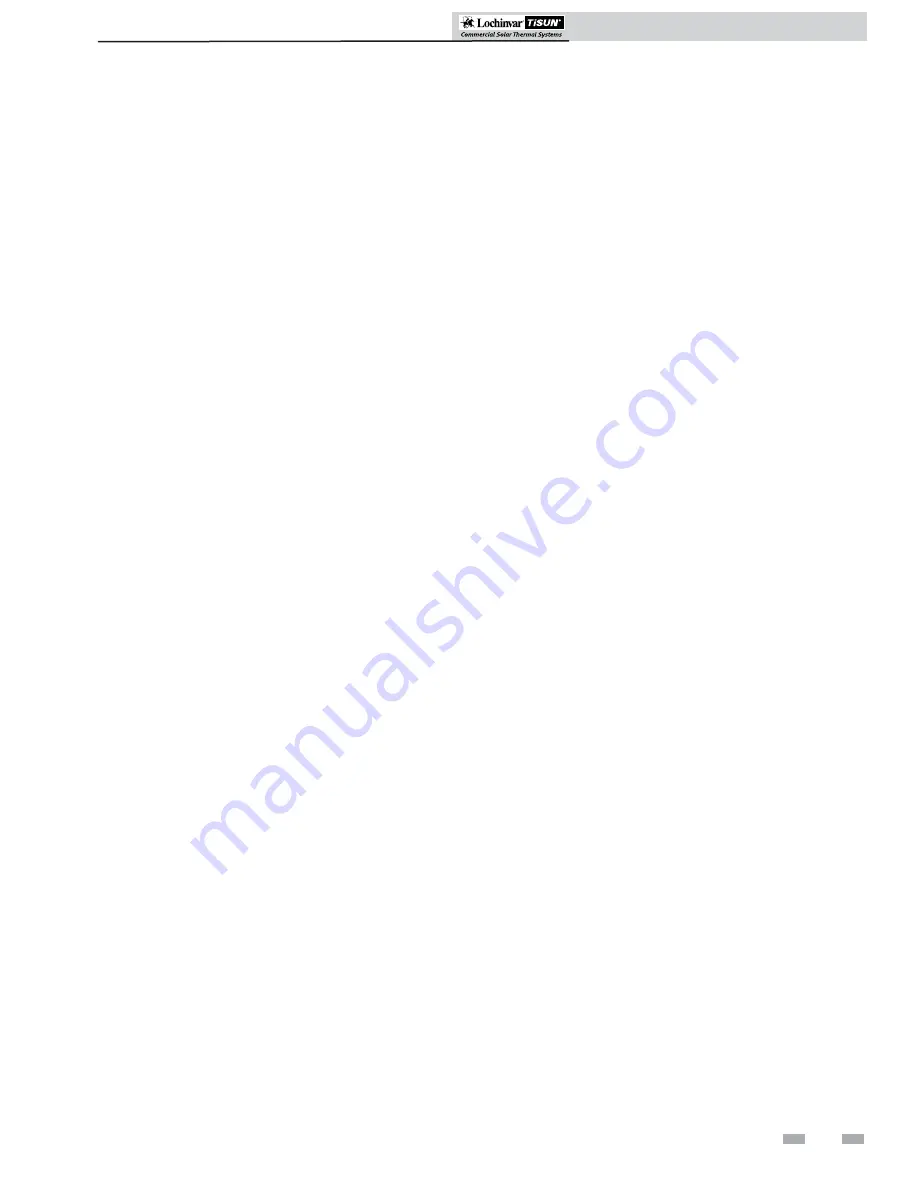
7
4
Commissioning the solar system
General
■
Before commissioning, all piping, connections and saftey
equipment should be checked to ensure that they are
correctly installed.
■
All pre-fitted solar station screw connections are firmly
tightened in the factory so that they do not usually need
retightening.
■
Seal integrity must be tested when commissioning and a
pressure test must be completed.
■
Fill the complete solar system with Lochinvar/TiSUN solar
liquid only. The mixing ratio should be adapted to local
conditions.
■
Never flush or pressure test the complete solar system with
just water. Flushing the system with water only can cause a
freezing hazard.
Filling, flushing and bleeding
■
There is one fill valve with hose connection for filling,
flushing and draining the solar system on both the safety
group and sensor measurement section.
■
Connect the pressure hose (forward flow) to the safety
group’s filling connection under the pressure gauge and
open fill/flush valve.
■
Connect the flushing hose (return) to the flushing
connection on the sensor measuring section and open
fill/flush valve.
■
Refer to “Technology, installation and commissioning:
Operation, multi-function ball valve and check valve” on
page 6.
■
Open the supply ball valve (by turning the red thermometer
handle counter-clockwise until it stops).
■
Close return ball valve (by turning the blue thermometer
handle clockwise, until it stops).
■
If necessary, the supply and return check valve can be
opened by moving the thermometer handles to the 45
°
position.
■
Put sufficient solar liquid in the tank of a filling and flushing
pump (not supplied). The mixing ratio should be adapted
to local conditions in terms of freeze protection.
■
Fill the solar system via the filling and flushing pump and
then flush the solar circuit for at least 15 min. to purge all of
the air out of the circuit.
■
Close the fill/flush valve (return) with the filling and
flushing pump running and increase the system pressure to
60 psi. The system pressure can be read at the
pressure gauge.
■
Close the fill/flush valve (forward flow) and switch off the
filling and flushing pump.
■
Open return ball valve (by turning the blue thermometer
handle 90
°
counter-clockwise until it stops).
■
The solar system features an air separator. Open the bleeder
valve until the solar liquid exits free of air bubbles.
■
Only if collector bleeder is installed: Bleed the system on the
collector until the solar liquid exits free of bubbles.
■
If necessary, increase the test pressure again to 60
psi and check the system for leaks. If the pressure gauge
shows the pressure dropping substantially, you have a leak
in the system.
■
Set the operating pressure to 60 psi as prescribed by the
system
manufacturer
■
Start up the circulation pump at maximum speed and allow
liquid to circulate for at least 15 min.
■
Remove the filling station hoses and screw the caps on the
flushing and filling valves.
■
Check the system again for leaks. Use the red and blue
thermometer handles to fully open the forward flow and
return ball valves.
■
Activate speed control on solar control unit. The highest
speed level should be set on the pump (phase control).
Note
:
The minimum speed set on the solar control unit must
not fall below the pump’s minimum nominal speed.
Note instructions for pump and solar control unit.
■
Once the installation settings have been completed and
checked, fit the solar station’s front insulation shell.
■
Refer to the collector manufacturer’s recommendations for
minimum flow requirements.
SL-PS Installation & Operation Manual