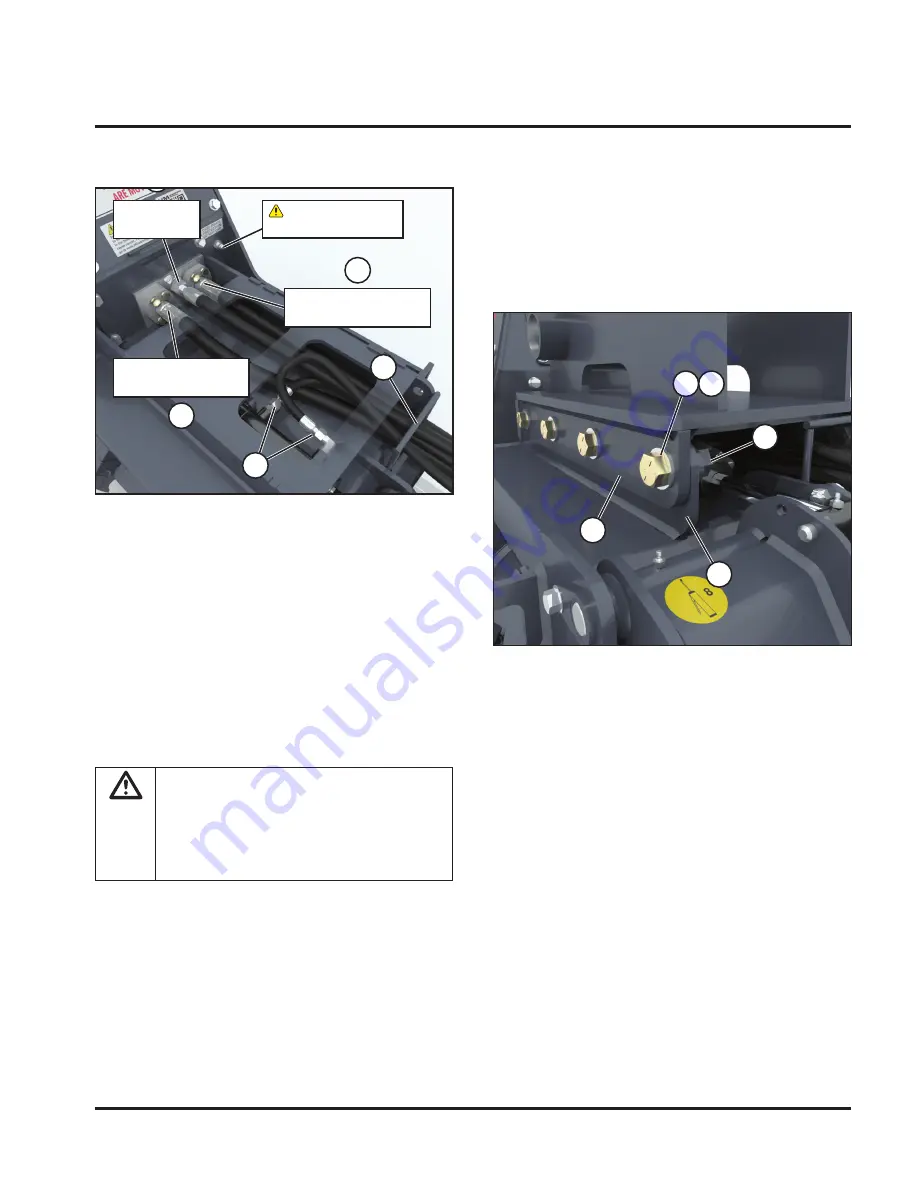
11
Battle Ax OM
Mounting the Battle Ax to the
Excavator
For a mounting bracket specific to your model of
excavator, contact Loftness.
NOTE:
Make sure hydraulic hoses are connected to the
Battle Ax before installing the mounting bracket.
3 4
5
1
2
5
Bolt the base mount (1) to the mounting plate (2) using the
eight bolts (3) and washers (4) (four on each side). Secure
with nut plates (5) (one on each side). Tighten.
Align excavator boom and connect to the mounting bracket.
Verify connection from excavator to mounting bracket is
secure.
Set-up Instructions
Hydraulic Connections
3
5
Tank
-16 Code 62 Split Flange
1
2
Case Drain
-12FJIC
Do not cap Case
Drain Protection.
Pressure
-16 Code 62 Split Flange
4
Connect hydraulics hoses (not included with the Battle
Ax) from the excavator to the Battle Ax. See below for
hose requirements.
1.
Tank
;
-16 Code 62 Split Flange
2.
Pressure
;
-16 Code 62 Split Flange
3.
Case Drain
;
-12FORB
4.
Hydraulic Thumb
(if equipped)
;
-8FORB
NOTE:
Route houses through ring (5) on frame.
IMPORTANT
:
Minimum case drain hose size is 3/4 in. It
is recommended that the hose connects
directly to the hydraulic reservoir.
WARNING:
Hydraulic Lines. Protect hands
and body from high pressure fluids.
Pressurized fluids can penetrate the skin.
Disconnect and lock out power source before
disconnecting and/or connecting hydraulic
hoses.
NOTE:
Use hoses that are the same diameter size as
those used on the hydraulic motor. Using smaller
diameter hoses will decrease hydraulic efficiency.
IMPORTANT
:
It is the owner’s responsibility to assure
that the hydraulic hoses from the power
unit to the attachment are not caught
in pinch points, or in any way damaged
by moving parts. Make sure hoses are
secured closely to the excavator’s boom
to avoid getting caught in tree branches.
Summary of Contents for 41BX30
Page 2: ......
Page 4: ......
Page 6: ......
Page 8: ......
Page 12: ...2 Battle Ax OM...
Page 35: ...25 Battle Ax OM PARTS IDENTIFICATION Parts Identification...
Page 56: ...46 Battle Ax OM...
Page 59: ...49 Battle Ax OM Appendix Torque Specifications Inches Hardware and Lock Nuts...
Page 60: ...50 Battle Ax OM Torque Specifications Cont d Metric Hardware and Lock Nuts Appendix...
Page 61: ......