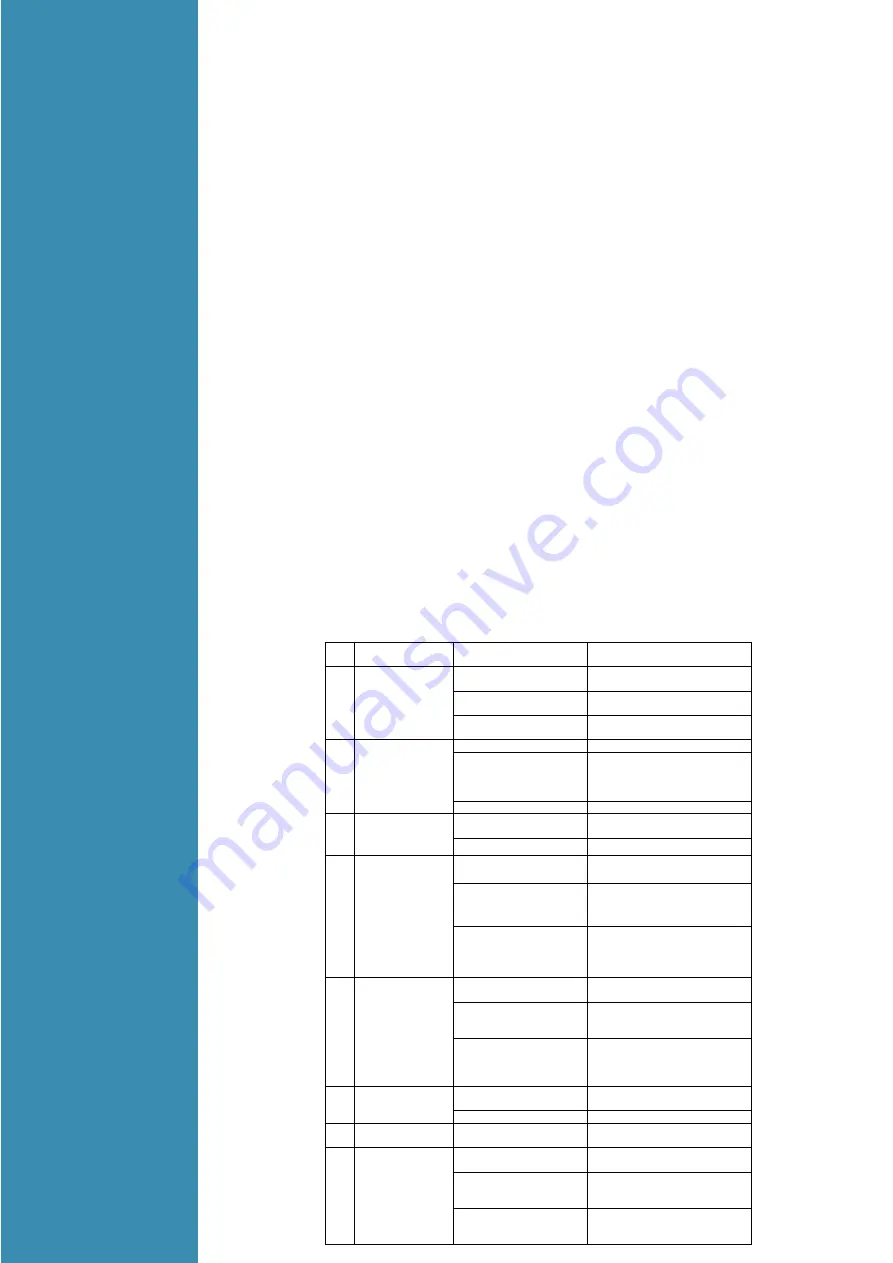
GRAND TIG 200 DC PFC MV adopts the latest Pulse Width Modulation (PWM) technology and the
Insulated Gate Bipolar Transistor (IGBT) power modules. It uses switching frequencies in the
20KHz-50KHz ranges so as to replace the traditional line-frequency transformer type welding machines.
Thus, machines are characterized with portability, small size, lightweight, low energy consumption and
noise, etc.
GRAND TIG 200 DC PFC MV has excellent performance: constant current output makes welding arc
more stable; fast dynamic response speed reduces the impact from the arc length fluctuation to the
current; accurate stepless current adjustment and pre-setting function. There are also some automatic
protection functions for under voltage, over current, over heat, etc. inside the welder, when the
problems listed before occurred, the alarm light on the front panel is on and at the same time the
output current will be cut off. It can self-protect, prolong the usefull life, greatly improved the reliability
and practicality of the welding machine.
The parameters of the machine on the front panel all can be adjusted continuously and steplessly,
such as start current, crater arc current, welding current, base current, duty ratio, upslope time,
downslope time, pre-gas, post-gas, pulse frequency, hot start, arc force and arc length etc. When
welding, it takes high frequency and high voltage for arc igniting to ensure the success ratio of
igniting arc.
TIG DC PULSE Characteristics
:
★
DC Pulsed TIG and MMA, adopt IGBT and advanced PWM technology
★
High performance MCU, Digital control, Digital display
★
HF/Lift TIG, current down slope and up slope, gas post-flow, Pulse Frequency
★
Intelligent protection: over-voltage, under-voltage, over-current, over-heat
1. For MMA, polarity connection can be chosen according to different electrodes
,
please refer to
3.3.
2. For DC TIG, DCEP is used normally (workpiece connected to positive polarity, while torch connected
to negative polarity). This connection has many characters, such as stable welding arc, low tungsten
pole loss, more welding current, narrow and deep weld;
3. DC Pulsed TIG has the following characters: 1) Pulse heating. Metal in Molten pool has short time on
high temperature status and freezes quickly, which can reduce the possibility to produce hot crack
of the materials with thermal sensitivity. 2) The workpiece gets little heat. Arc energy is focused. Be
suitable for thin sheet and super thin sheet welding. 3) Exactly control heat input and the size of the
molten pool. The depth of penetration is even. Be suitable for welding by one side and forming by
two sides and all position welding for pipe. 4) High frequency arc can make metal for microlite
fabric, eliminate blowhole and improve the mechanical performance of the joint. 5) High frequency
arc is suitable for high welding speed to improve the productivity.
This machine has wide range of applications. Given its small size, light weight, easy and flexible
operation, it can be used in various kinds of environment, such as working aloft, field work, interior
decoration, etc.
GRAND TIG 200 DC PFC MV is suitable for all positions welding for various plates made of stainless steel,
carbon steel, alloyed steel, titanium, copper, etc, which is also applied to pipe installment, mould
mend, petrochemical, architecture decoration, car repair, bicycle, handicraft and common
manufacture.
3.3.3
MMA
Welding
trouble
shooting
3.3.2
Operation
for MMA
Welding
(1)
According to the above method to install is correct, turn the power switch, so that the power
switch is “ON” position, then the power indicator light, the fan comes on, the device work
properly.
(2)
Select the MMA function with the 4T/2T/MMA selector switch.
(3)
Set the required output current by turning the current control knob .
(4)
Place the electrode into the electrode holder and clamp tight.
(5)
Strike the electrode against the work piece to create and arc and hold the electrode steady
to maintain the arc.
(6)
Commence welding. If necessary, readjust the Welding Current control knob to obtain the
welding condition required.
(7)
After completion of welding the Power Source should be left turned ON for 2 to 3 minutes. This
allows the fan to run and cool the internal components.
(8)
Switch the ON/OFF Switch (located on the rear panel) to the OFF position.
NOTE:
-
Note the polarity of wiring, the general DC welding wire in two ways. Selected according to the
technical requirements of welding the appropriate connection, if you choose incorrectly will
result in arc instability and spatter large adhesion and other phenomena, such cases can be
quickly reversed to joints.
-
If the work piece distance from the welding machine, the second line(electrode holder and
ground) is longer, so choose the appropriate conductor cross-sectional area should be larger
to reduce cable voltage drop.
The following chart addresses some of the common problems of MMA welding. In all cases of
equipment malfunction, the manufacturer’s recommendations should be strictly adhered to and
followed.
NO. Trouble
Possible Reason
Suggested Remedy
1
No arc
Incomplete welding circuit
Check earth lead is connected.
Check all cable connections.
No power supply
Check that the machine is switched
on and has a power supply
Wrong mode selected
Check the MMA selector switch is
selected
2
Porosity
−
small
cavities or holes
resulting from gas
pockets in weld
metal
Arc length too long
Shorten the arc length
Work piece dirty,
contaminated or moisture
Remove moisture and materials like
paint, grease, oil, and dirt, including
mill scale from base metal
Damp electrodes
Use only dry electrodes
3
Excessive Spatter
Amperage too high
Decrease the amperage or choose a
larger electrode
Arc length too long
Shorten the arc length
4
Weld sits on top,
lack of fusion
Insufficient heat inpu t
Increase the amperage or choose a
larger electrode
Work piece dirty,
contaminated or moisture
Remove moisture and materials like
paint, grease, oil, and dirt, including
mill scale from base metal
Poor welding technique
Use the correct welding technique or
seek assistance for the correct
technique
5
Lack of penetration
Insufficient heat inpu t
Increase the amperage or choose a
larger electrode
Poor welding technique
Use the correct welding technique or
seek assistance for the correct
technique
Poor joint preparation
Check the joint design and fit up,
make sure the material is not too
thick. Seek assistance for the correct
joint design and fit u p
6
Excessive
penetration - burn
through
Excessive heat input
Reduce the amperage or use a
smaller electrode
Incorrect travel speed
Try increasing the weld trav el speed
7
Uneven weld
appearance
Unsteady hand, wavering
hand
Use two hands where possible to
steady up, practise your technique
8
Distortion
−
movement of base
metal during
welding
Excessive heat input
Reduce the amperage or use a
smaller electrode
Poor welding technique
Use the correct welding technique or
seek assistance for the correct
technique
Poor joint preparation and or
joint design
Check the joint design and fit up,
make sure the material is not too
thick. Seek assistance for the correct