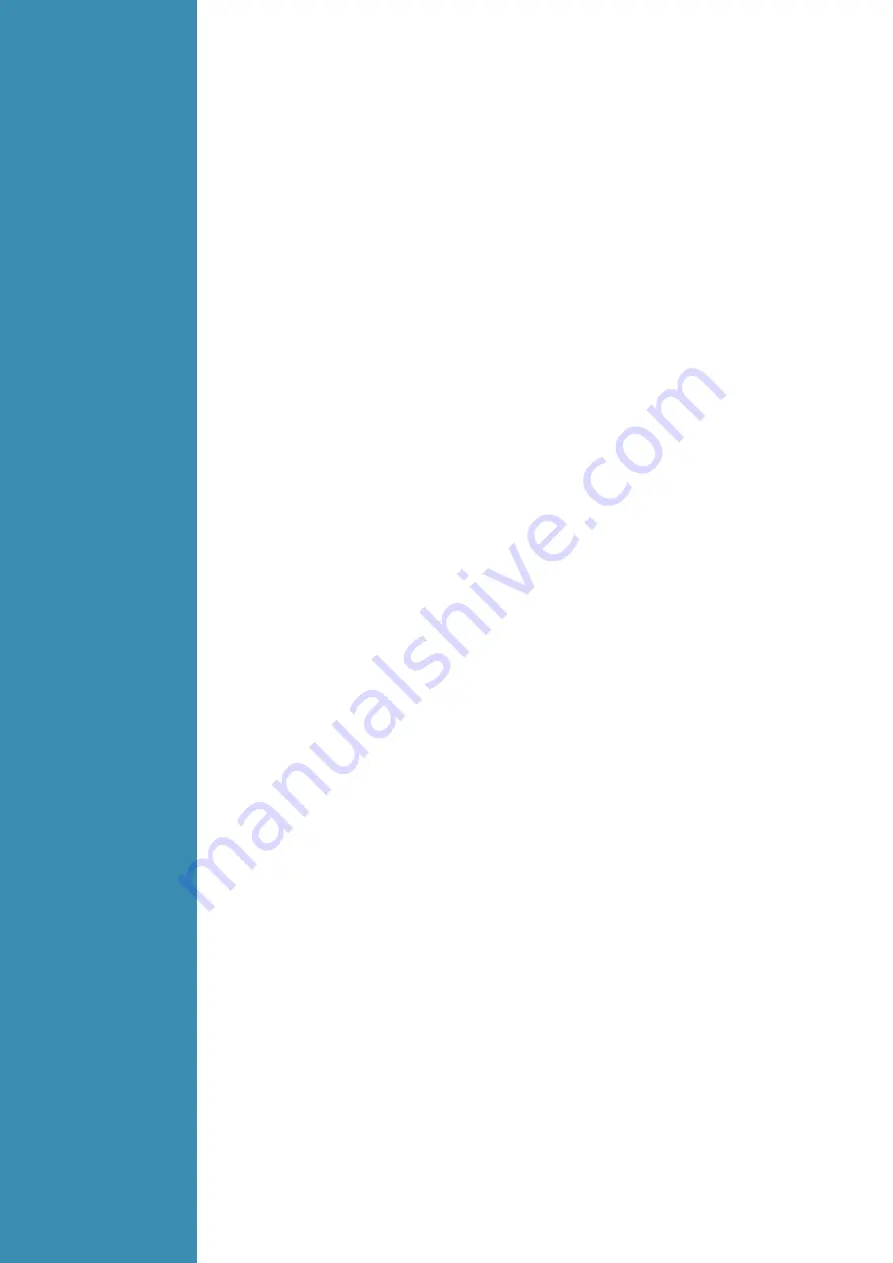
GRAND
TIG 200
D C P F C M V
Lift TIG Ignition
is a compromise that minimises tungsten contamination while eliminating the electrical
interference of HF start systems. Lift arc starting works by lightly resting the tungsten on the work
piece, activating the torch trigger signal and then lifting the tungsten off. The control circuit will sense
when the tungsten is removed from the work piece and send a low powered pulse of electricity
through the tungsten that will cause the TIG arc to initiate. Because the tungsten is not ‘live’ when it is
in contact with the work, contamination is minimised.
TIG 2T/4T Trigger Control (28)
2T mode the trigger is pulled and held on to activate the welding circuit, when the trigger is released,
the welding circuit stops. 4T is known as ‘latching’ mode. The trigger is pulled once and released to
activate the welding circuit, pulled and released again to stops the welding circuit. This function is
useful to longer welds as the trigger is not required to be held on continuously. TIG series of welding
machines also has more advanced current controls that can be used in 4T mode.
Parameter Select/ Adjust Knob (8)
Switch between welding parameter settings by pressing this knob, adjust by turning the knob. Value of
the parameter selected will be shown on the digital multifunction display (34).
TIG Parameter Setting
Pre gas flow setting indicator (18)
Controls the period shielding gas will flow for when the torch is triggered before the arc starts. This
purges the work area of atmospheric gas which could contaminate the weld before the weld starts.
Unit(S) and setting range (0-2S).
Start current setting indicator (19)
Available in 4T trigger mode, sets a welding current 5-100% of the main welding current activated
when the trigger is held on to ‘latch’ the trigger before the main weld current is started. Once the
trigger is released, the current will go through the upslope (20) period if it is set, to the main welding
current (17).
Up slope setting indicator (20)
When the trigger is activated, the welding current will increase gradually over the time selected up to
the set main welding current (17). Unit(S) and setting range (0-10S).
TIG welding current setting indicator (17)
Sets the main welding current. Unit(A) and setting range (5-200A).
Base current setting indicator (5)
Only available when pulse mode (15) is selected. Sets the current of the low/ base pulse. Unit(A) and
setting range (5-200A).
Down slope setting indicator (11)
When the trigger is released, the welding current will reduce gradually over the time selected down
to 0. This allows the operator to complete the weld without leaving a ‘crater’ at the end of the weld
pool. Unit(S) and setting range (0-10S).
End current setting indicator (10)
Available in 4T trigger mode, sets a welding current 5-100% of the main welding current activat- ed
when the trigger is held on to ‘unlatch’ the trigger before the weld is finished. If downslope (11) is set,
the current will go through the downslope period before going to the end current set. When the trigger
is released, the arc will stop.
Post gas flow setting indicator (9)
Controls the period of time the shielding gas continues to flow for after the arc is stopped. This protects
the weld area and torch tungsten from contamination while it is still hot enough to react with
atmospheric gases, after the weld is finished. Unit(S) and setting range (0-10S).
Pulse width setting indicator (12)
Only available when pulse mode (15) is selected. Sets the time proportion as a percentage between
the peak current and base current when using pulse mode. Neutral setting is 50%, the time period of
the peak current and base current pulse is equal. Higher pulse duty setting will give greater heat input,
while lower pulse duty will have the opposite effect. Unit(%) and setting range (5-95%).
Pulse frequency setting indicator (13)
Only available when pulse mode (15) is selected. Sets the rate that the welding output alternates
between the peak and base current settings. Unit(Hz).
Pulse mode ‘off’ indicator (16)
Pulse mode ‘On’ indicator (15)