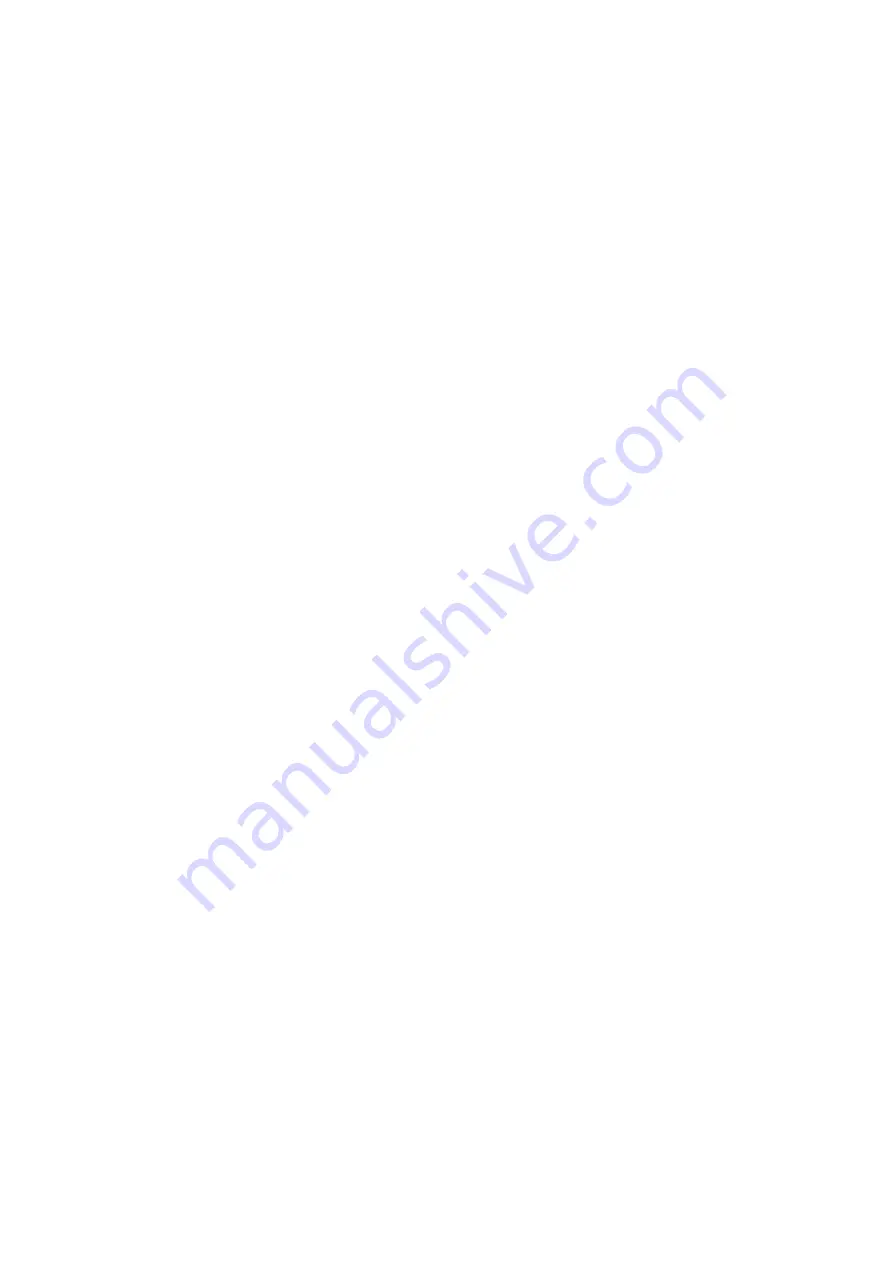
Operation Manual
64
water, otherwise, the rubber components of the system will be quickly damaged and the braking effect
will be reduced.
(3) The air in oil channel system will affect the braking performance, so air bleeding shall be carried
out after part replacement and repair with the method as follows:
A. Remove the sludge and scales at pipeline, oil storage chamber, oil filler and air bleeding location
of the oil channel system;
B. Fill up brake fluid as required;
C. Start the engine until the air pressure reaches 0.67-0.69 MPa and then stop it;
D. Cover a clear plastic pipe onto the air nipple, with the other end of the pipe into the oil container;
E. Continuously step down the brake pedal for several times and then depress it firmly. Release the
bleeding nipple at the upper end of front/rear wheel disk brake to bleed the air until the liquid column
without bubble flows out, and then screw down the bleeding nipple and release the brake pedal. Pay
attention to timely supplement brake fluid into the brake oil cup during air bleeding to avoid air entering
into the system;
F.
After the air bleeding, open the water drain valve at the bottom of air reservoir to drain out the
pressure oil when there is some pressure in the reservoir, otherwise, the water residue will rust the
reservoir and thus affect the service life of the rubber components in the air channel system.
(4) For safety, calibrate the relief valve frequently to maintain it in normal status.
A. Frequently check pressure vessels, in case of air leakage and blockage, immediately replace the
pressure controller;
B. Calibrate the relief valve at least once a year to ensure its rated pressure is 0.784MPa in
serviceable condition;
C. Check the pressure gauge, in case of air leakage and failure, immediately replace it;
D. Have the measurement department or other related specialized department to calibrate the
pressure gauge at least once a year to ensure its serviceable condition;
(5) The user shall pay attention to the following items on the air reservoir when using it:
A. The general service life of air reservoir: It is five years if the loader is continuously used, shorter
time if its use is interrupted or about three years if it is unused for over one month. When the service
life expires, replace the air reservoir by the one with our company's trade mark.
B. Frequently check the outside of the air reservoir, in case of anticorrosive coat stripping, remove
the rust and apply anti-rust paint; in case of weld crack or deformation, immediately stop using it and
replace with a new one;
C. Carry out a pressure resistance test for the air reservoir every year with a test pressure of 1.2MPa.
If the loader has been unused for more than three months, carry out this test before reusing it.
iii
Parking brake system
Structure and working principle of main components: