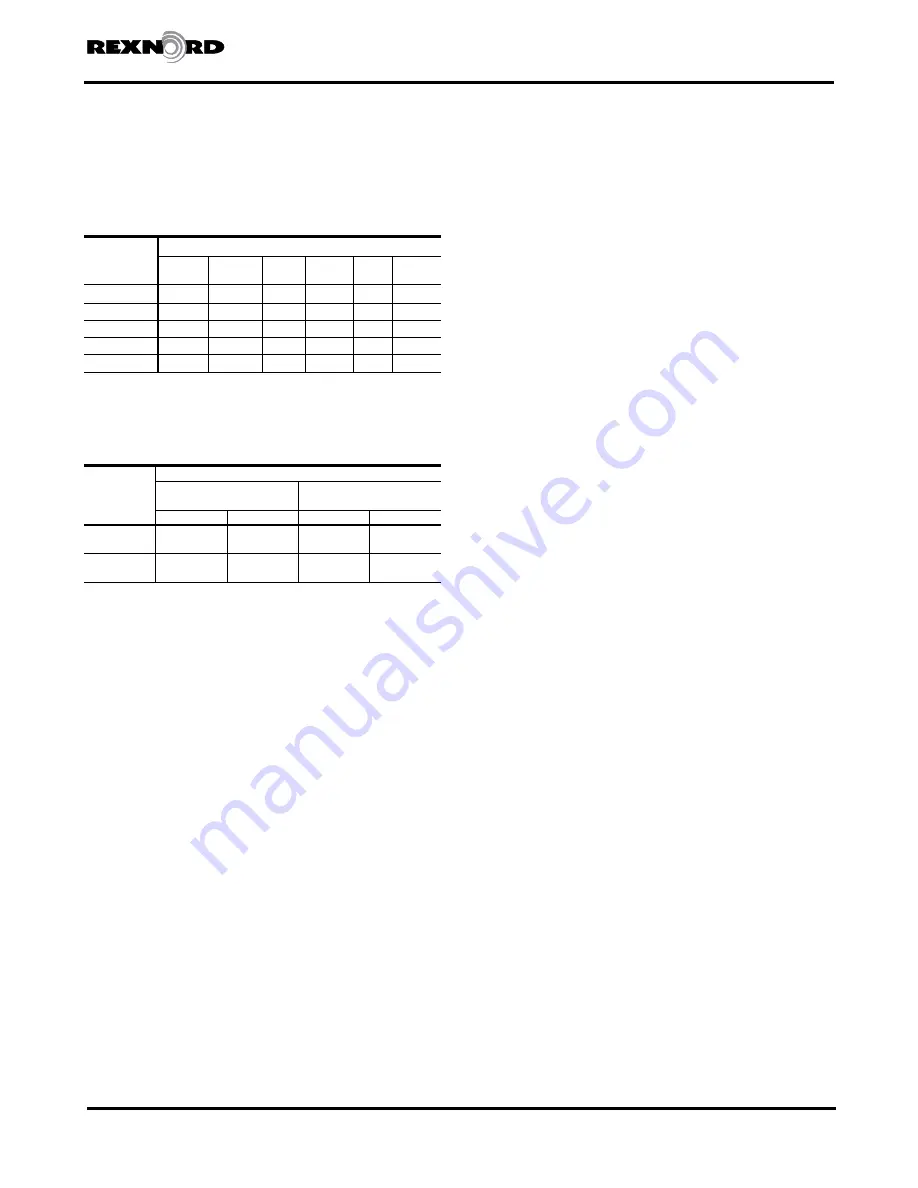
Rexnord
®
Planetgear™ 7000 Series Speed Reducer
s
Owners Manual
Sizes Neptune, Neptune Plus, Orion Plus, Saturn Plus & Titan Plus (Page 7 of 32)
Rexnord
158-170
3001 W. Canal St., Milwaukee, WI 53208-4200
January 2015
Telephone: 414-937-4359 Fax: 414-937-4359 www.rexnord.com
Supersedes 11-12
TABLE 3 — Approximate Oil Capacity
À
REDUCER
SERIES
Reduction Type
S/D/T
Gallons
S/D/T
Liters
Quad
Gallons
Quad
Liters
Quint
Gallons
Quint
Liters
Neptune
7.8(14.0)
29.5(53.0)
8.5(15.5) 32.2(58.7) 8.3(15.3) 31.4(54.9)
Neptune Plus
7.8(14.0)
29.5(53.0)
8.5(15.5) 32.2(58.7) 8.3(15.3) 31.4(54.9)
Orion Plus
12.0(19.0)
45.4(72.0) 12.7(20.0) 48.0(75.7) 12.8(21.0) 48.5(79.5)
Saturn Plus
13.0(22.0)
49.2(83.3) 15.0(25.0) 56.8(94.6) 14.8(24.8) 56.0(93.9)
Titan Plus
15.5(34.0)
z
58.6(128.7)
z
17.5(38.0) 66.2(143.9) 17.2(38.0) 65.1(143.8)
S= Single, D= Double, T= Triple, Quad= Quadruple, Quint= Quintuple
() - Vertically oriented reducers
4
Quantities are approximate. Always fill drive to the specified level.
z
Double and Triple only.
TABLE 4 — Viscosity Grade Recommendation
For Petroleum-Based Lubricants
OUTPUT
SPEED
AMBIENT TEMPERATURES
+15° to +60°F
(-9° to +16°C)
+50° to +125°F
(+10° to +52°C)
ISO-VG
AGMA
ISO-VG
AGMA
RPM
BELOW 20
150
4
320
6
20 RPM
And ABOVE
150
4
220
5
OIL LEVELS
From the nameplate or the oil capacity chart below, determine
the quantity of oil needed. Fill reducer to the oil fill plug
as described in the Maintenance section (Section V) for
horizontally mounted units, or the Vertical Service section
(Section VII) for vertically mounted units.
LUBRICANT CHANGES
OIL ANALYSIS REPORT
— Checking oil conditions at
regular intervals is recommended. Analyze oil samples
approximately every 1,000 hours for petroleum lubricants
or every 3,000 hours for synthetic lubricants. In the
absence of more specific limits, the guidelines listed below
may be used to indicate when to change petroleum or
polyalphaolefin type synthetic lubricants:
1. Water content is greater than 500 ppm (parts per
million) (0.05%).
2. Iron content exceeds 150 ppm.
3. Silicon (dust/dirt) exceeds 25 ppm, above reference
sample from new oil container.
4. Copper content exceeds 75 ppm.
5. TAN (Total Acid Number) 50% increase above reference
sample from new oil container.
6. Viscosity changes more than ±15%.
7. Solid particle contamination code exceeds 25/22/18 for
particle sizes
≥
4/
≥
6/
≥
14 microns, respectively per ISO
4406.
Laboratory analysis is recommended for optimum lubricant
life and gear drive performance. Oil samples should be
taken from the oil level hole, not the drain hole.
PETROLEUM LUBRICANTS
— In the absence of oil
analysis, change gear oils every 6 months or 2,500
operating hours, whichever occurs first. Change oil more
frequently when gear drives operate in extremely humid,
chemical or dust laden atmospheres. In these cases,
lubricants should be changed every 3 to 4 months or
1,500 to 2,000 hours. If the drive is operated in an area
where temperatures vary with the seasons, change the
oil viscosity grade to suit the temperature, refer to Table
4. Generally lubricant suppliers can analyze oil from the
drive periodically and recommend economical change
schedules.
SYNTHETIC LUBRICANTS
— In the absence of oil
analysis, synthetic lube change intervals can be extended
to 8,000 hours depending upon operating temperatures.
Laboratory analysis is recommended for optimum lubricant
life and drive performance. Change lube with change in
ambient temperature, if required. Refer to Table 5.
GREASE PURGED SEALS
All drives are furnished with grease purged seals which
minimize the entry of contaminants and abrasive dusts into
the drive. Drives are shipped with NLGI #2 grade grease in
the seal housing cavities unless otherwise specified.
Whenever changing oil in the drive, purge the seals
with one of the NLGI #2 grade greases listed in Table 8.
Depending upon the degree of contamination, periodically
(at least every six months), purge contaminated grease
from seals by slowly pumping fresh bearing grease
through the seal,
WITH HAND GREASE GUN
, until fresh
grease flows out along the shaft. Wipe off purged grease.
CAUTION
: Rapid regreasing with a power grease gun can
force grease inward past the seals and plug the oil drain
back system causing seal leaks
WARNING
: Greases in Table 8 contain harmful substances
and are not allowed in the food processing industry. If
grease could contaminate the product, as in the food and
drug industries, the grease originally supplied with gear
drive must be removed and replaced with a grease listed
in Table 14. Simply purging grease with a grease gun
will not remove all grease and cross-contamination will
likely occur. Grease registered as H1 by NSF, (National
Sanitation Foundation) is suitable for food processing
applications.
STORED & INACTIVE GEAR DRIVES
Refer to Section VII (Storage Procedures) for details on
stored & inactive gear drives.
Summary of Contents for CD-1261
Page 1: ... 0 1 2121 3 4 1 5 6 ...
Page 2: ... ...
Page 3: ... ...
Page 4: ... ...
Page 5: ... ...
Page 6: ... 0 1 2 3 4 5 6 5 6 7 1 1 5 6 5 6 5 6 1 0 0 ...
Page 7: ... ...
Page 8: ... 0 1 2 0 3 0 ...
Page 9: ... ...
Page 10: ... 0 12 2 0 3 4 5 5 5 0 0 ...
Page 11: ... 6 12 0 0 7 5 5 0 8 0 8 5 0 50 9 4 12 0 0 9 4 0 9 64 0 5 0 0 1 0 0 ...
Page 12: ... 0 2 0 0 3 0 6 6 6 6 6 0 0 0 5 5 0 6 0 ...
Page 14: ... ...
Page 15: ... 0 0 1 1 2 1 1 3 0 4 5 1 0 1 0 0 2 1 2 1 0 0 0 2 1 1 1 1 1 0 0 0 1 0 0 0 1 0 1 6 1 1 ...
Page 17: ... 1 0 3 0 0 1 1 1 71 0 0 1 1 1 0 1 1 ...
Page 18: ... ...
Page 25: ... 8 ...
Page 28: ... 1 7 4 0 4 1 4 1 1 4 1 1 1 4 85 4 4 1 4 1 4 0 6 4 1 1 1 01 0 1 4 6 4 1 1 4 L 1 ...
Page 29: ... 4 ...
Page 30: ... 0 1 2 3 24 3 5 6 4 5 6 4 5 5 1 5 4 74 8 5 9 1 4 27 3 5 4 74 8 5 5 29 13 27 3 1 29 13 5 1 ...
Page 31: ... 8 8 80 1 2 3 5 6 4 5 6 4 5 5 1 5 A 9 1 B 4 27 3 888 7 8 0 B 4 C D 5 29 13 B 27 3 888 7 29 13 ...
Page 32: ... 4 24 3 5 6 4 5 6 4 5 5 4 7 M 7 4 7 N 2 0 7 2 M 0 N M ...
Page 35: ... 8 G 8 0 G 4 88 8E 1 2 3 5 6 4 5 6 4 5 5 1 4 1 4 27 3 1 088 7 5 4 1 5 29 13 H 27 3 088 7 ...
Page 36: ... E 5 ...
Page 37: ... 9 4 5 H 0 1 2034 2034 2034 2034 0 5 1 6 71 6 1 2 1 1 1 0 1 81 1 9 9 ...
Page 38: ... 1 5 1 5 1 3 05 3 1 0 1 1 6 A 6 1 A 6 B 1 6 B 6 1 1 1 6 6 6 2 9 0 6 ...
Page 39: ... 0 ...
Page 40: ... 0 0 ...
Page 42: ......
Page 43: ... 0122 3 4 5 6 4 4 4 4 5 4 4 4 4 4 7 7 4 4 6 4 4 5 5 4 5 8 8 3 5 3 5 3 5 3 5 5 ...
Page 44: ... 0 0 0 0 0 0 0 0 0 0 1 1 2 3 0 3 3 0 0 33 0 3 0 3 3 0 ...
Page 46: ... 011 2 3 3 4 3 2 5 5 6 ...
Page 47: ... 011 2 3 4 5 3 6 3 7 7 2 4 ...
Page 48: ... 00 1 2 3 4 3 5 5 5 5 5 3 1 1 2 2 6 1 1 1 5 5 7 5 5 5 5 ...
Page 49: ... 0122 3 4 5 6 7 4 8 4 4 8 4 4 8 5 5 5 5 5 5 5 5 5 5 5 5 ...
Page 50: ... 0 11 2 2 2 2 2 3 4 5 0 5 3 6 7 6 6 8 9 8 9 6 6 8 9 0 1 1 1 1 1 8 9 1 1 1 5 ...
Page 51: ... 011 2 3 4 5 4 2 2 2 6 2 6 6 3 3 3 3 3 3 3 ...
Page 53: ... 011 2 3 4 5 4 2 6 33 2 33 6 6 6 ...
Page 54: ... 011 2 3 3 3 3 4 5 4 33 2 33 6 3 3 3 ...
Page 56: ... 0122 3 4 5 6 7 8 4 4 5 8 4 4 8 9 9 9 8 4 4 4 88 8 8 8 ...
Page 57: ... 0 1 1 1 2 1 3 1 1 1 0 1 1 1 4 1 1 ...
Page 58: ... ...
Page 59: ... ...
Page 96: ...Bearing Maintenance Guide x Lubrication x Troubleshooting ...
Page 97: ......
Page 98: ......
Page 99: ......
Page 100: ......
Page 101: ......
Page 102: ......
Page 103: ......
Page 104: ......
Page 105: ......
Page 106: ......
Page 107: ......
Page 108: ......
Page 109: ......
Page 110: ......
Page 111: ......
Page 112: ......
Page 113: ......
Page 114: ......
Page 115: ......
Page 116: ......
Page 117: ......
Page 118: ......
Page 119: ......
Page 120: ......
Page 121: ......
Page 122: ......
Page 123: ......
Page 124: ......
Page 125: ......
Page 126: ......
Page 165: ... 0 0 1 2 3 4 5 6 52 3 52 3 7 8 4 6 52 4 6 1 9 9 9 9 9 ...
Page 166: ... 0 5 9 9 2 2 4 6 4 6 4 6 7 8 7 8 2 4 6 4 7 8 7 8 2 4 6 4 6 52 A ...
Page 167: ... 0 0 1 2 1 2 3 4 2 1 2 3 4 ...
Page 168: ... 0 2 1 2 3 3 4 2 1 2 3 4 2 ...
Page 194: ......
Page 195: ......
Page 196: ......
Page 218: ......
Page 219: ......
Page 234: ...15 Notes Model 121 Regulators Brochure ...
Page 236: ......