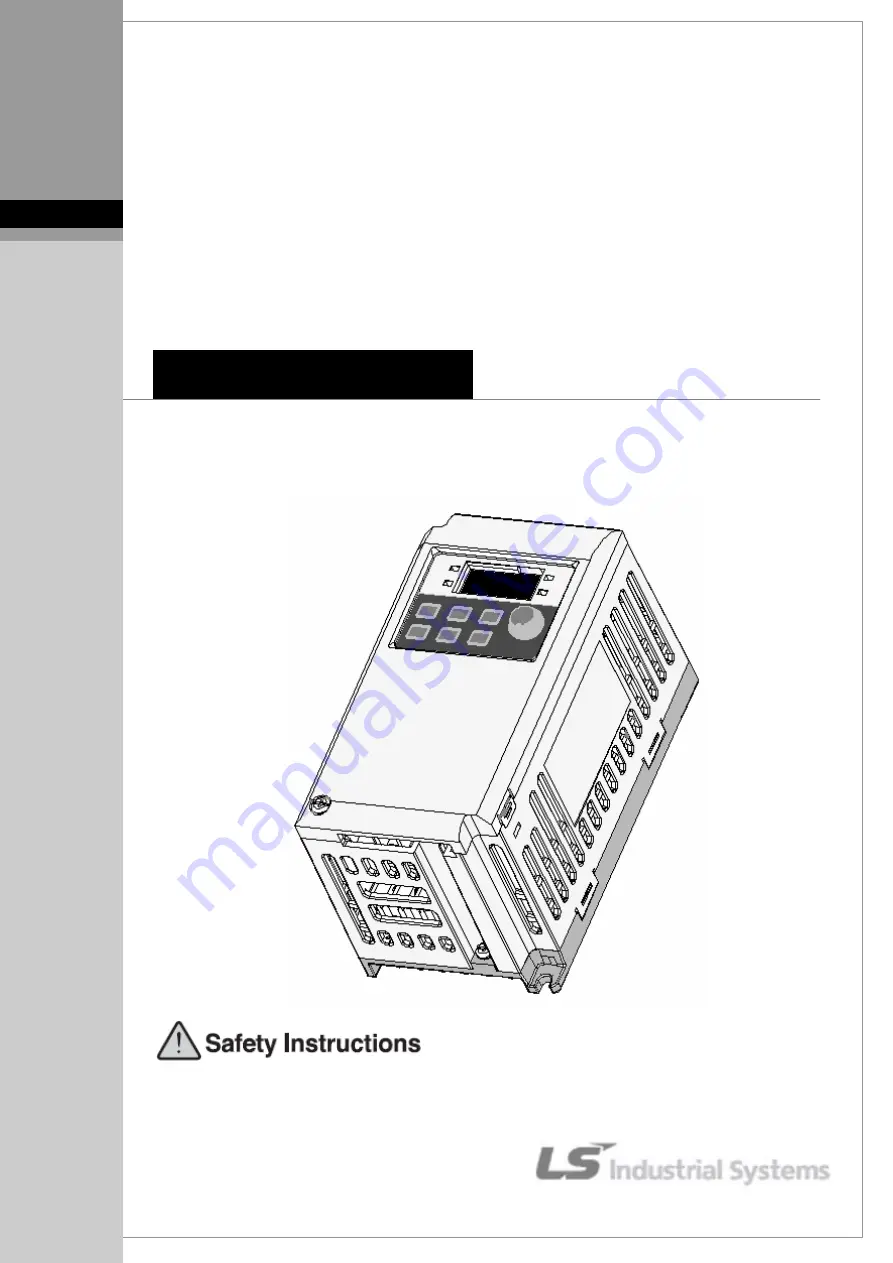
Right choice for ultimate yield
LSIS strives to maximize customers' profit in gratitude of choosing us for your
partner.
SV-iE5 User Manual
0.1~0.4kW (200V)
z
Read this manual carefully before
installing, wiring, operating, servicing
or inspecting this equipment.
z
Keep this manual within easy reach
for quick reference.
Summary of Contents for SV-iE5 Series
Page 124: ...iV ...