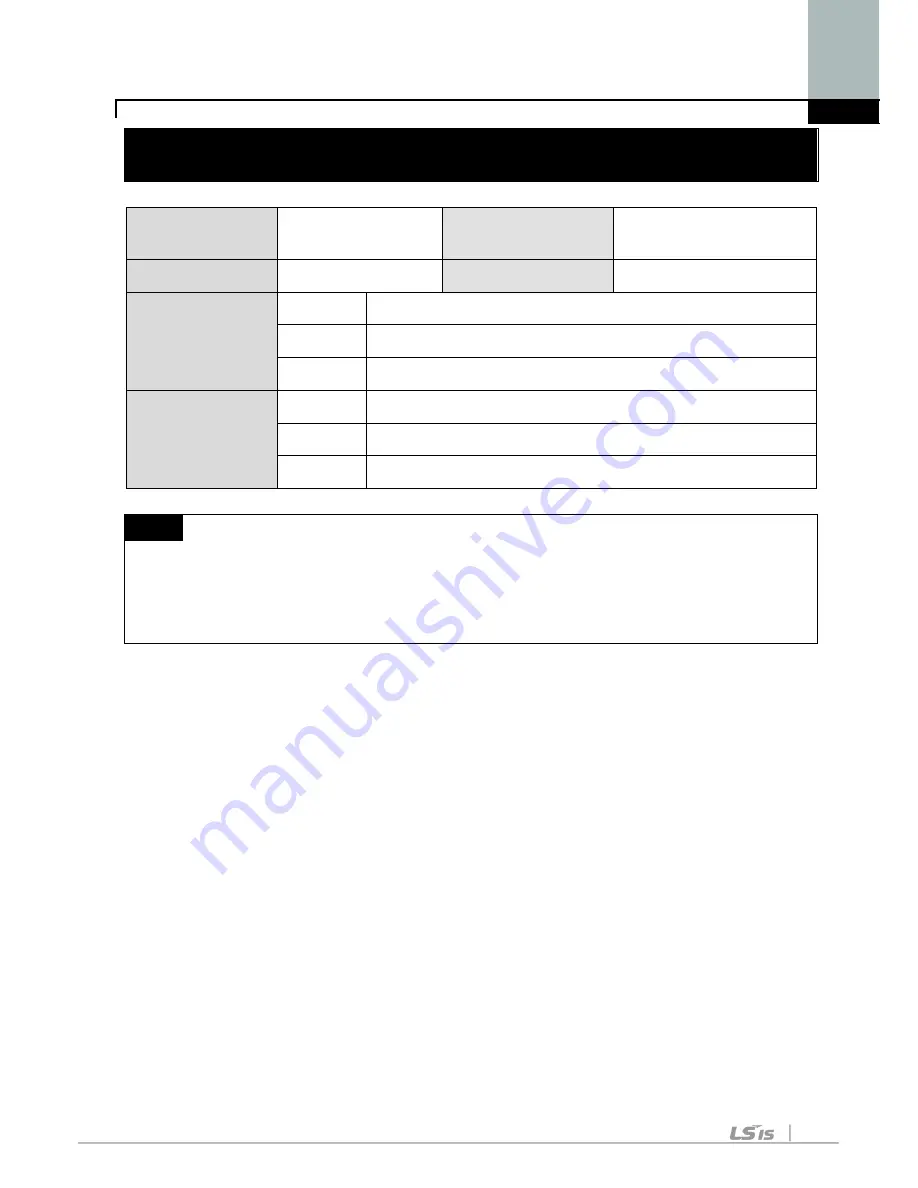
Warranty
xi
WARRANTY
Maker
LSIS Co., Ltd
Installation
(start-up) date
Model No.
SV-iC5
Warranty period
Customer info
Name
Address
Tel.
Sales office
Name
Address
Tel.
Note
This product has been manufactured through the strict QC control and
inspection of LSIS. Warranty period is 12 months after installation or 18
months after manufactured when the installation date is unidentified.
However, the guarantee term may vary on the sales term.
In-warranty service information
If the defective part has been identified under normal and proper use within the
guarantee term, contact your local authorized LS distributor or LS Service center.
Out-of-warranty service information
The guarantee will not apply in the following cases.
Troubles are attributable to a user’s intentional negligence or carelessness.
Damage was caused by abnormal voltage and peripheral devices’ malfunction (failure).
Damage was caused by natural disasters(earthquake, fire, flooding, lightning and etc).
When LS nameplate is not attached.
Summary of Contents for 004iC5-1
Page 8: ......
Page 22: ...3 Wiring 3 6 ...
Page 38: ...5 Programming Keypad 5 14 ...
Page 42: ...6 Basic Operation 6 4 ...
Page 64: ...7 Function List 7 22 ...
Page 74: ...9 Specifications 9 4 ...