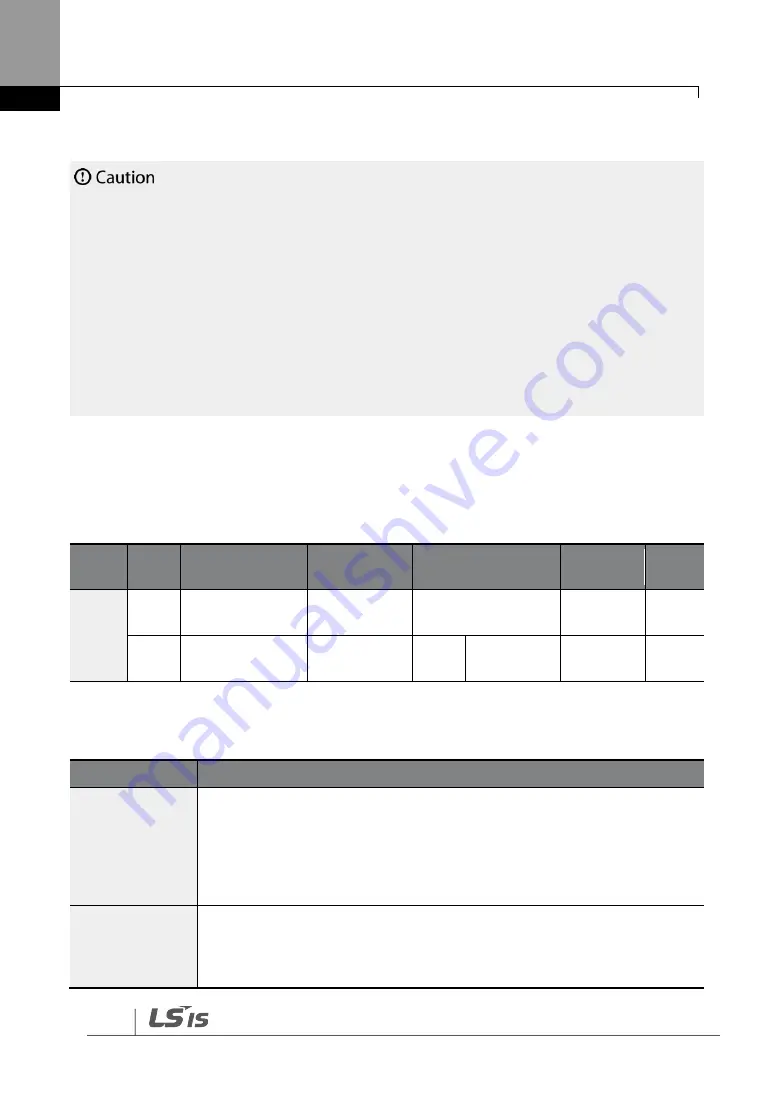
Learning Advanced Features
242
•
If the auto restart number is set, be careful when the inverter resets from a fault trip. The
motor may automatically start to rotate.
•
In HAND mode, auto restart resets the trip condition but it does not restart the inverter
operation.
•
In AUTO mode,
-
if the auto restart is configured, the inverter restarts after a trip condition is released
(command via digital input is used to restart the operation).
-
if the auto restart is not configured and the trip condition is released using the OFF
key, or the switches at the terminal input, the inverter stays in the OFF state.
Because the command information is reset along with the trip condition, a new
command is required to operate the inverter.
5.29 Operational Noise Settings (Carrier Frequency
Settings)
Group Code
Name
LCD Display
Parameter Setting
Setting
Range
Unit
CON
04
Carrier
Frequency
Carrier Freq
3.0
1.0
–15.0
kHz
05
Switching Mode
PWM* Mode
0
Normal
PWM
0
–1
-
* PWM: Pulse width modulation
Operational Noise Setting Details
Code
Description
CON-04
Carrier Freq
Adjusts motor operational noise by changing carrier frequency settings.
Power transistors (IGBT) in the inverter generate and supply high
frequency switching voltage to the motor. The switching speed in this
process refers to the carrier frequency. If the carrier frequency is set high, it
reduces operational noise from the motor. If the carrier frequency is set low,
it increases operational noise from the motor.
CON-05 PWM
Mode
The heat loss and leakage current from the inverter can be reduced by
changing the load rate option at CON-
05 (PWM Mode). Selecting ‗1
(LowLeakage P
WM)‘ reduces heat loss and leakage current, compared to
when ‗0 (Normal PWM)‘ is selected. However, it increases the motor noise.
Summary of Contents for H100
Page 14: ......
Page 18: ...Preparing the Installation 4 37 90 kW 3 Phase ...
Page 27: ...Preparing the Installation 13 ...
Page 47: ...33 Installing the Inverter ...
Page 48: ...Installing the Inverter 34 Input and Output Control Terminal Block Wiring Diagram ...
Page 61: ...47 Installing the Inverter ...
Page 71: ...Learning to Perform Basic Operations 57 ...
Page 88: ...Learning to Perform Basic Operations 74 ...
Page 103: ...89 Learning Basic Features Code Description V1 Quantizing ...
Page 129: ...115 Learning Basic Features ...
Page 140: ...Learning Basic Features 126 ...
Page 148: ...Learning Basic Features 134 ...
Page 171: ...157 Learning Advanced Features Deceleration dwell operation ...
Page 183: ...169 Learning Advanced Features ...
Page 184: ...Learning Advanced Features 170 PID Command Block ...
Page 185: ...171 Learning Advanced Features PID Feedback Block ...
Page 186: ...Learning Advanced Features 172 PID Output Block ...
Page 187: ...173 Learning Advanced Features PID Output Mode Block ...
Page 197: ...183 Learning Advanced Features ...
Page 201: ...187 Learning Advanced Features Code Description 100 EPID1 Control block ...
Page 202: ...Learning Advanced Features 188 EPID2 Control block ...
Page 237: ...223 Learning Advanced Features Time Period Schedule AP3 38 Except3 Day 01 01 ...
Page 244: ...Learning Advanced Features 230 ...
Page 259: ...245 Learning Advanced Features Code Description Code Description Volt ...
Page 362: ...Learning Protection Features 348 ...
Page 415: ...401 RS 485 Communication Features Item Standards Parity check None ...
Page 524: ...Table of Functions 510 ...
Page 533: ...Table of Functions 519 ...
Page 547: ...533 Troubleshooting ...
Page 585: ...Technical Specification 571 ...
Page 594: ...580 ...
Page 595: ...581 ...
Page 596: ...582 ...