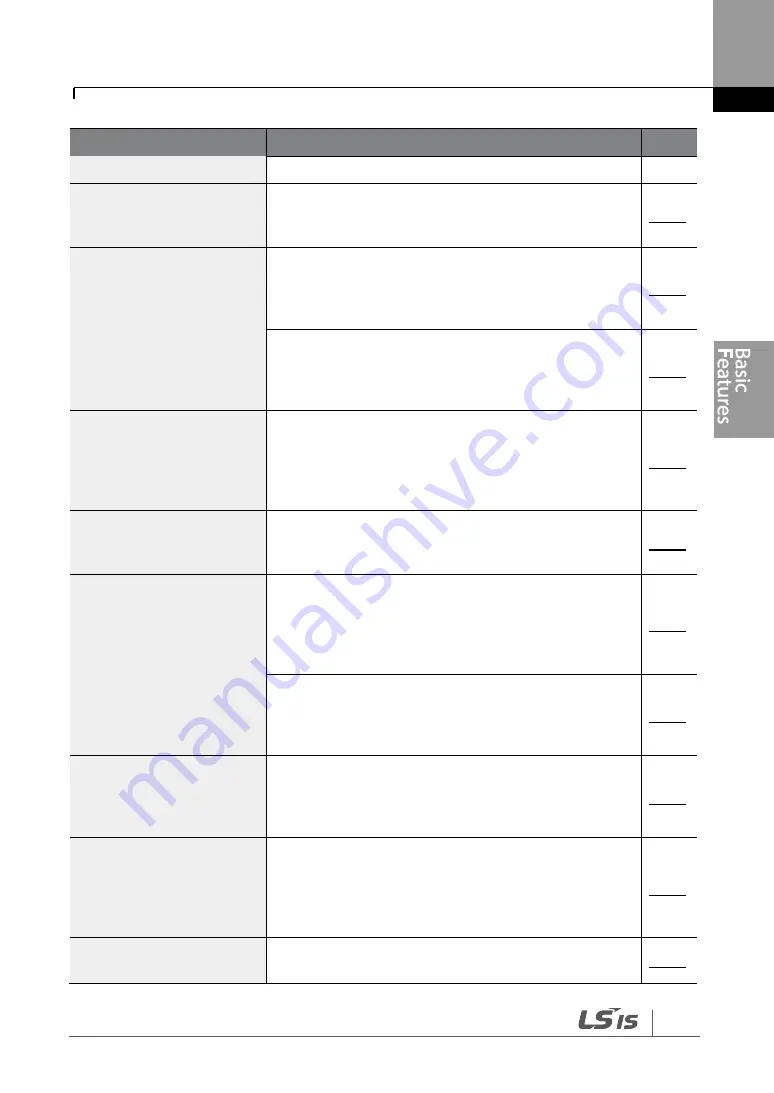
77
Learning Basic Features
Basic Tasks
Description
Ref.
frequency may vary during operation.
Square reduction V/F
pattern operation
Configures the inverter to run the motor at a square
reduction V/F pattern. Fans and pumps are appropriate
loads for square reduction V/F operation.
User V/F pattern
configuration
Enables the user to configure a V/F pattern to match
the characteristics of a motor. This configuration is for
special-purpose motor applications to achieve optimal
performance.
Manual torque boost
Manual configuration of the inverter to produce a
momentary torque boost. This configuration is for loads
that require a large amount of starting torque, such as
elevators or lifts.
Automatic torque boost
Automatic configuration of the inverter that
provides‖auto tuning‖ that produces a momentary
torque boost. This configuration is for loads that require
a large amount of starting torque, such as elevators or
lifts.
Output voltage adjustment
Adjusts the output voltage to the motor when the power
supply to the inverter differs from the motor‘s rated
input voltage.
Accelerating start
Accelerating start is the general way to start motor
operation. The typical application configures the motor
to accelerate to a target frequency in response to a run
command, however there may be other start or
acceleration conditions defined.
Start after DC braking
Configures the inverter to perform DC braking before
the motor starts rotating again. This configuration is
used when the motor will be rotating before the voltage
is supplied from the inverter.
Deceleration stop
Deceleration stop is the typical method used to stop a
motor. The motor decelerates to 0 Hz and stops on a
stop command, however there may be other stop or
deceleration conditions defined.
Stopping by DC braking
Configures the inverter to apply DC braking during
motor deceleration. The frequency at which DC braking
occurs must be defined and during deceleration, when
the motor reaches the defined frequency, DC braking is
applied.
Free-run stop
Configures the inverter to stop output to the motor
using a stop command. The motor will free-run until it
Summary of Contents for H100
Page 14: ......
Page 18: ...Preparing the Installation 4 37 90 kW 3 Phase ...
Page 27: ...Preparing the Installation 13 ...
Page 47: ...33 Installing the Inverter ...
Page 48: ...Installing the Inverter 34 Input and Output Control Terminal Block Wiring Diagram ...
Page 61: ...47 Installing the Inverter ...
Page 71: ...Learning to Perform Basic Operations 57 ...
Page 88: ...Learning to Perform Basic Operations 74 ...
Page 103: ...89 Learning Basic Features Code Description V1 Quantizing ...
Page 129: ...115 Learning Basic Features ...
Page 140: ...Learning Basic Features 126 ...
Page 148: ...Learning Basic Features 134 ...
Page 171: ...157 Learning Advanced Features Deceleration dwell operation ...
Page 183: ...169 Learning Advanced Features ...
Page 184: ...Learning Advanced Features 170 PID Command Block ...
Page 185: ...171 Learning Advanced Features PID Feedback Block ...
Page 186: ...Learning Advanced Features 172 PID Output Block ...
Page 187: ...173 Learning Advanced Features PID Output Mode Block ...
Page 197: ...183 Learning Advanced Features ...
Page 201: ...187 Learning Advanced Features Code Description 100 EPID1 Control block ...
Page 202: ...Learning Advanced Features 188 EPID2 Control block ...
Page 237: ...223 Learning Advanced Features Time Period Schedule AP3 38 Except3 Day 01 01 ...
Page 244: ...Learning Advanced Features 230 ...
Page 259: ...245 Learning Advanced Features Code Description Code Description Volt ...
Page 362: ...Learning Protection Features 348 ...
Page 415: ...401 RS 485 Communication Features Item Standards Parity check None ...
Page 524: ...Table of Functions 510 ...
Page 533: ...Table of Functions 519 ...
Page 547: ...533 Troubleshooting ...
Page 585: ...Technical Specification 571 ...
Page 594: ...580 ...
Page 595: ...581 ...
Page 596: ...582 ...