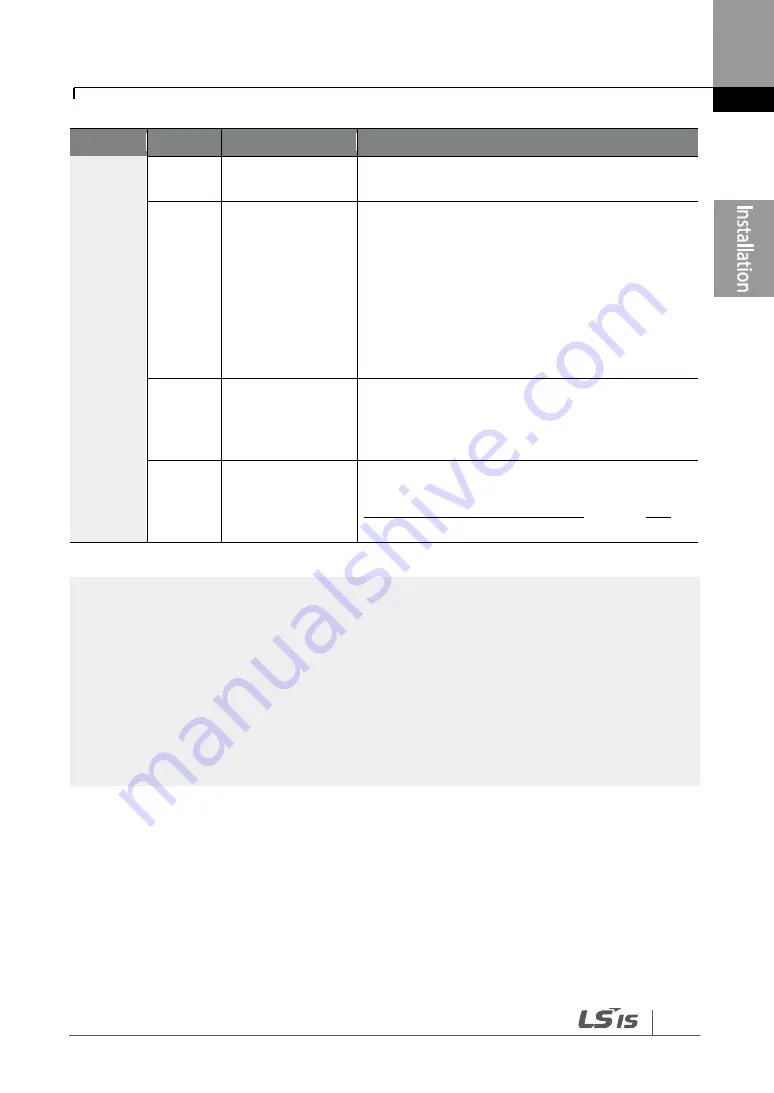
37
Installing the Inverter
Function
Label
Name
Description
configuration (e.g. supplying power to other
external devices).
A1/C1/B
1
Fault relay output
A,B contact
Sends out alarm signals when the inverter‘s
safety features are activated.
( N.O.: AC250 V
≤
2 A , DC 30 V
≤
3 A
N.C.: AC250 V
≤
1 A , DC 30 V
≤
1 A)
Fault condition: A1 and C1 contacts are
connected (B1 and C1 open connection)
Normal operation: B1 and C1 contacts are
connected (A1 and C1 open connection)
Factory default: Frequency
A2/C2
A3/C3
A4/C4
A5/C5
Multi-function
relay output A
contact
Defined in the inverter signal features such as
output via the multi-function output terminal.
(AC 250 V
≤
5 A, DC 30 V
≤
5 A).
S+/S-
/SG
Used to send or receive RS-485 signals. Refer to
0
for more details.
Note
•
While making wiring connections at the control terminals ensure that the total cable length
does not exceed 165 ft (50 m).
•
Ensure that the length of any safety related wiring does not exceed 100 ft (30 m).
•
Ensure that the cable length between the keypad and the inverter does not exceed 10 ft
(3.04 m). Cable connections longer than 10 ft (3.04 m) may cause signal errors.
•
Use ferrite material to protect signal cables from electro-magnetic interference.
•
Take care when supporting cables using cable ties, to apply the cable ties no closer than 6
inches from the inverter. This provides sufficient access to fully close the terminal cover.
Step 5 PNP/NPN Mode Selection
The H100 inverter supports both PNP (Source) and NPN (Sink) modes for sequence inputs
at the terminal. Select an appropriate mode to suit requirements using the PNP/NPN
selection switch (SW2) on the control board. Refer to the following information for detailed
applications.
Summary of Contents for H100
Page 14: ......
Page 18: ...Preparing the Installation 4 37 90 kW 3 Phase ...
Page 27: ...Preparing the Installation 13 ...
Page 47: ...33 Installing the Inverter ...
Page 48: ...Installing the Inverter 34 Input and Output Control Terminal Block Wiring Diagram ...
Page 61: ...47 Installing the Inverter ...
Page 71: ...Learning to Perform Basic Operations 57 ...
Page 88: ...Learning to Perform Basic Operations 74 ...
Page 103: ...89 Learning Basic Features Code Description V1 Quantizing ...
Page 129: ...115 Learning Basic Features ...
Page 140: ...Learning Basic Features 126 ...
Page 148: ...Learning Basic Features 134 ...
Page 171: ...157 Learning Advanced Features Deceleration dwell operation ...
Page 183: ...169 Learning Advanced Features ...
Page 184: ...Learning Advanced Features 170 PID Command Block ...
Page 185: ...171 Learning Advanced Features PID Feedback Block ...
Page 186: ...Learning Advanced Features 172 PID Output Block ...
Page 187: ...173 Learning Advanced Features PID Output Mode Block ...
Page 197: ...183 Learning Advanced Features ...
Page 201: ...187 Learning Advanced Features Code Description 100 EPID1 Control block ...
Page 202: ...Learning Advanced Features 188 EPID2 Control block ...
Page 237: ...223 Learning Advanced Features Time Period Schedule AP3 38 Except3 Day 01 01 ...
Page 244: ...Learning Advanced Features 230 ...
Page 259: ...245 Learning Advanced Features Code Description Code Description Volt ...
Page 362: ...Learning Protection Features 348 ...
Page 415: ...401 RS 485 Communication Features Item Standards Parity check None ...
Page 524: ...Table of Functions 510 ...
Page 533: ...Table of Functions 519 ...
Page 547: ...533 Troubleshooting ...
Page 585: ...Technical Specification 571 ...
Page 594: ...580 ...
Page 595: ...581 ...
Page 596: ...582 ...