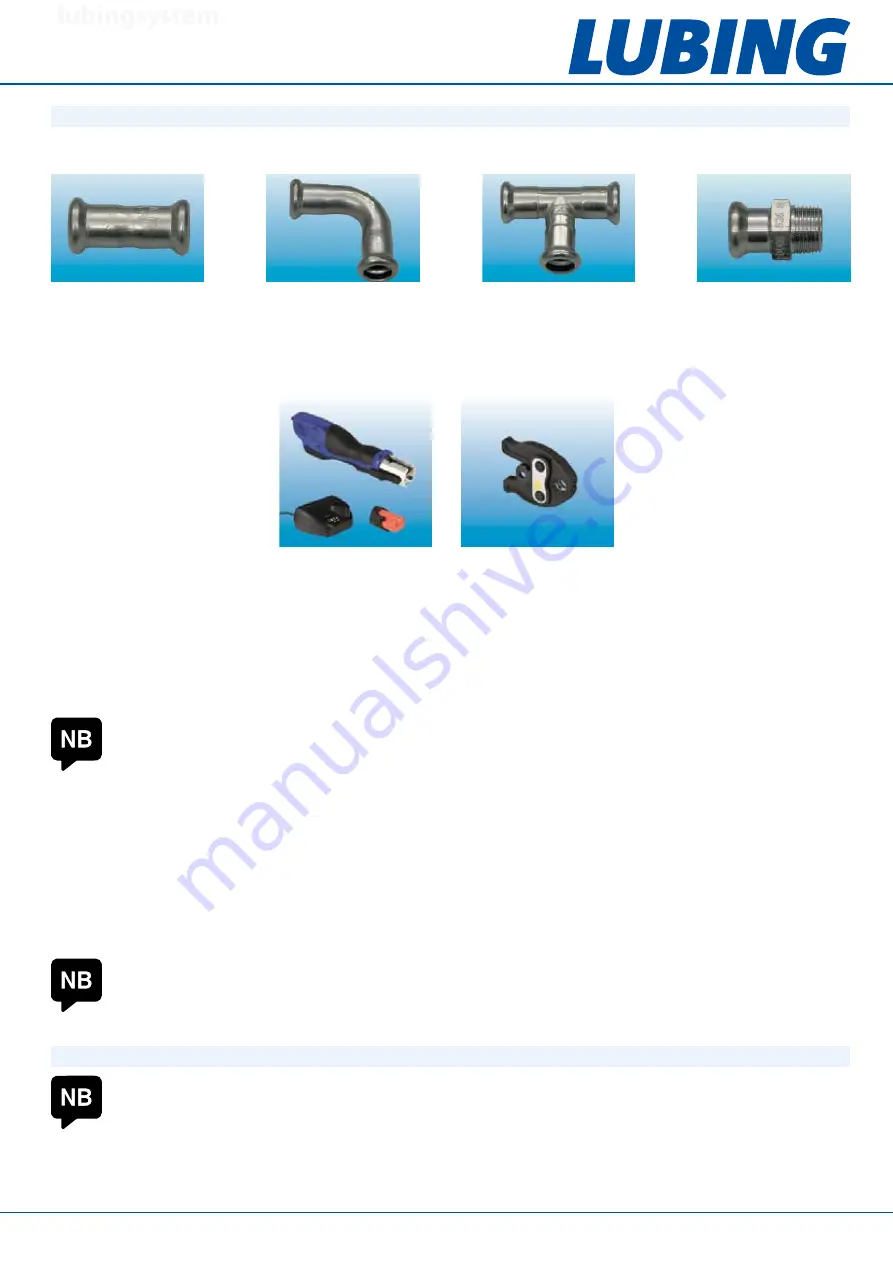
Top climate system
with LUBING Touch Controller
Copyright © Lubing System - All rights reserved
22
4.5.3 PressFix fittings
The nozzle lines and connecting pip
es can also be assembled with PressFix fittings as an alternative to cutting ring
fittings.
Required assembly tools:
PressFix cordless gripper (art. no. 7460)
PressFix Toolhead PB12 (art. no. 7465)
Preparatory measures:
Check press fitting. There must be no dirt or residues in the joint.
Check sealing rings for damage and correct installation in press fitting.
The pipe ends must be carefully deburred on the outside and inside. This is the only way to avoid damage to the
sealing rings when inserting the pipes into the fittings.
Note: damaged sealing rings can lead to leakages.
Proceed as follows during assembly:
–
Push the pipes into the press fitting up to the stop by turning them slightly.
– If problems occur, it is possible that not enough deburring has taken place. Repeat deburring.
– The joints must not be bent, otherwise the seal may be damaged.
– Connect/seal the pipes with the special press tool.
– For reliable and safe pressing, the internal groove of the press jaws must exactly surround the annular bead
of the seal of the fitting.
– The jaws grip around the elevation and press the pipe and sleeve tightly.
– After a click is heard, the joint is ready.
4.5.4 Wall mounting of connecting pipes and nozzle lines
Mounting on walls is done horizontally with pipe clips (art. 7431). The distance to the ceiling should be at least
500mm. The recommended distance between the fixings is 1.5m - the
maximum allowed distance is 2m
. At
Art. no. 7404
Art. no. 7405
Art. no. 7406
Art. no. 7409
Art. no. 7460
Art. no. 7465
NOTE
The use of oil, grease, adhesives or similar substances is strictly prohibited.
NOTE
Assemble with 2 persons to avoid bending of the pipes under their own weight.
NOTE
Nozzle lines can no longer be rotated after successful installation with PressFix fittings - the spray direction
of the nozzles can no more be adjusted afterwards!
lubingsystem.
com
lubingsystem.
com
lubingsystem.
com
lubingsystem.
com
lubingsystem.
com
lubingsystem.
com
lubingsystem.
com
lubingsystem.
com
lubingsystem.
com
lubingsystem.
com
lubingsystem.
com
lubingsystem.
com
lubingsystem.
com
lubingsystem.
com
lubingsystem.
com
lubingsystem.
com
lubingsystem.
com
lubingsystem.
com
lubingsystem.
com
lubingsystem.
com
com
lubingsystem.
com
lubingsystem.
com
lubingsystem.
com
lubingsystem.
com
lubingsystem.
com
lubingsystem.
com
lubingsystem.
com
lubingsystem.
com
lubingsystem.
com
lubingsystem.
com