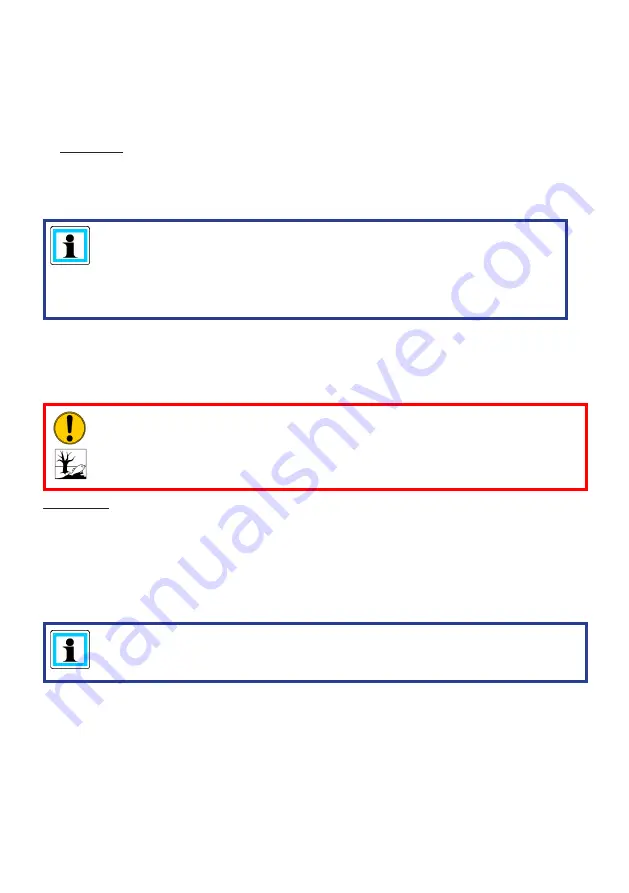
17
NOTE:
In this test, an idle time of approximately 2 minutes needs to be observed and
the hydraulic pump needs to be reloaded to operating pressure.
The resulting max. operating pressure must not drop by more than 5% after
10 seconds.
A test pressure gauge is available from the LUKAS line of accessories.
Perform an operational check of the hydraulic pump at least once per year; in the case of
continuous use, once every half year.
Operational check
• no suspicious noises,
• tests at maximum load.
Execution:
Place the hydraulic pump on a solid base to operate. Then, connect a test manometer
to the supply hose line. Release the pump lever lock and close the discharge valve.
Then, the pressurisation to operating pressure corresponding to the specification on the
identification plate occurs.
10.3 Hydraulic fluid change or adding hydraulic fluid
The hydraulic fluid should be changed if dirty at least once a year. When the hydraulic pump
is operated in an especially dusty environment, we recommend changing the fluid at least
once every half year.
ATTENTION!
Add hydraulic fluid only if the hydraulic pump is disconnected from the lines or
the equipment operated with the pump is hydraulically depressurised. Otherwise,
after filling the entire hydraulic system could contain more hydraulic fluid than the
tank can hold.
Procedure:
1. Open the bleed/fill cap on the tank.
2. Add hydraulic fluid until the fluid level comes up to 1-2 cm below the top edge of the oil
tank.
3. Bleed the hydraulic pump as described in the chapter "bleeding the pump".
4. Check the fluid level again and close the tank again at the correct fluid level with the
vent/fill cap on the tank. Should the tank no longer be sufficiently full after bleeding, start
the fill procedure again at item 2.
NOTE:
Should the fluid level in the tank still not be reached after repeated refilling (during
maintenance), we recommend searching for leaks in the hydraulic system.
10.4 Care
If possible, do not store the hand pump in a damp or extremely dusty environment in order
to ensure a long service life. If this is unavoidable, you should perform more frequent
maintenance and/or shield the pump from these effects if possible.
Regularly coat all metal parts with oil to prevent any corrosion.
Summary of Contents for 81-50-35
Page 2: ...2...
Page 27: ...27 13 Notes...