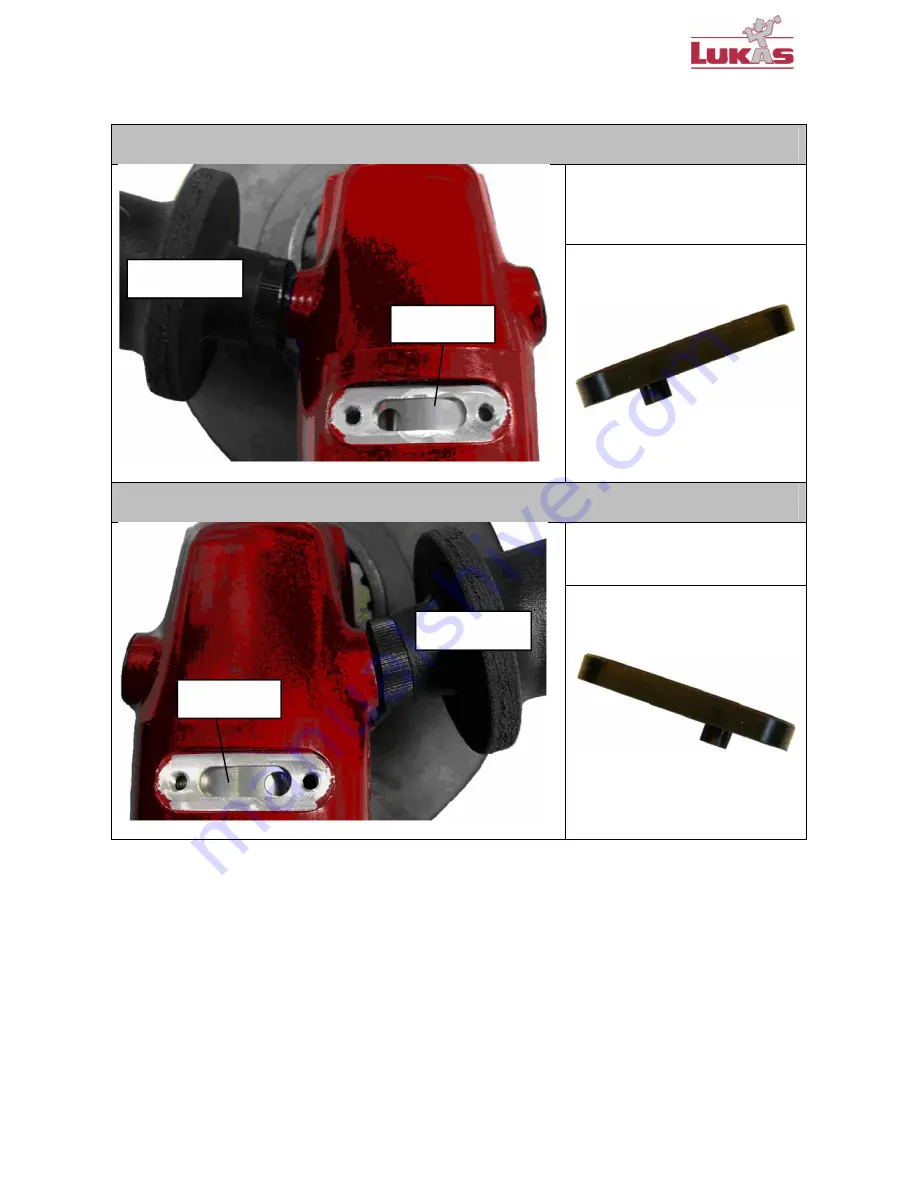
17.10.2008
Page 14
• AMIN 12-125T WH •
Location of the slide / vane for RIGHT-HANDED OPERATION
Location of the support for
right-handed operation
Location of the slide / vane for LEFT -HANDED OPERATION
Location of the support for
left-handed operation
5
Handling
Only use the machine with due regard to the safety instructions and maintenance stipulations.
The machine is started by the lever valve.
Slide / vane
Handle
Slide /
vane
Handle