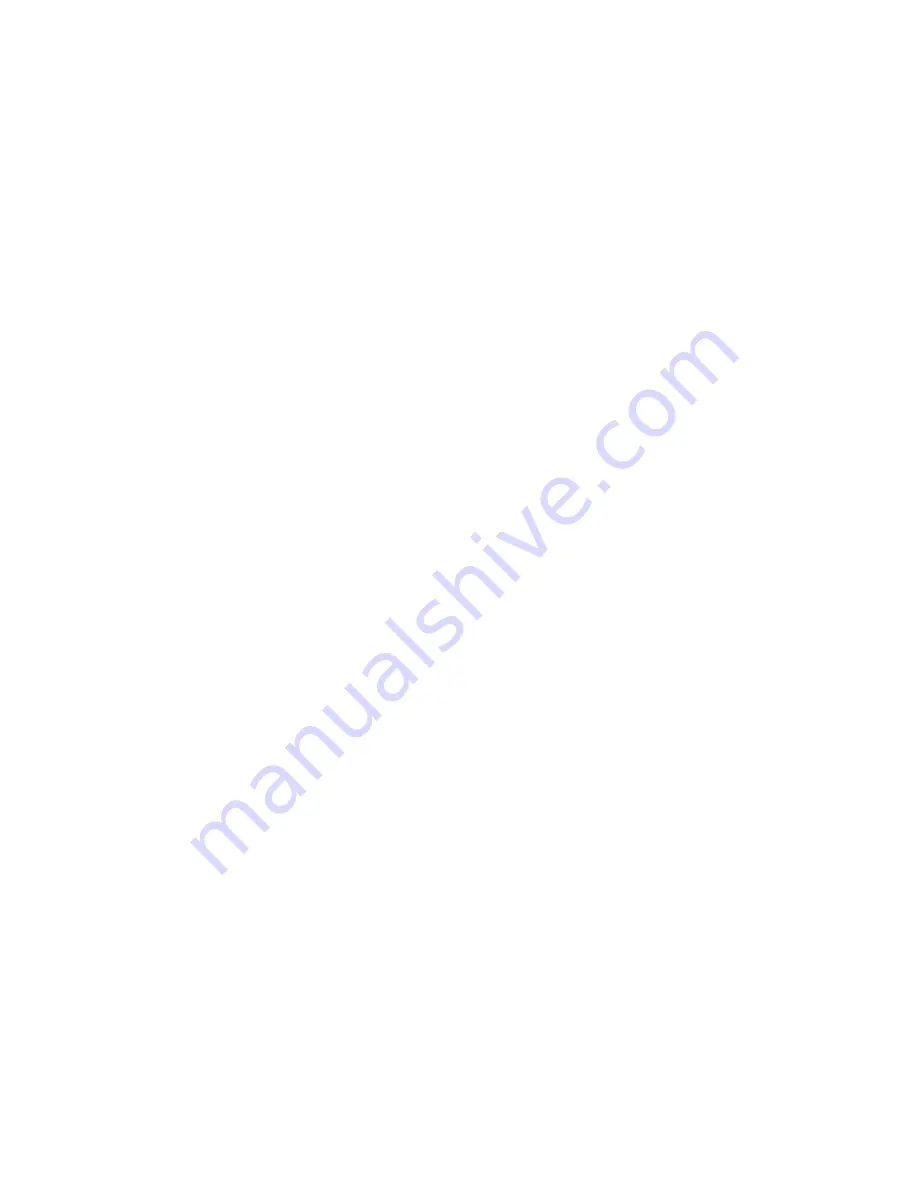
9
7.3 Hydraulic power package
A LUKAS motor pump of PO6... LSI series is to be used for operating the devices. If the
power pack comes from a manufacturer other than LUKAS, it must be ensured that it
fulfills the LUKAS specifications (see connection diagram), as otherwise dangers may
occur for which LUKAS cannot be held liable. Especially it has to be made sure that the
permissible working pressure of 50 MPa (500 bar) is without consultation with LUKAS
not exceeded.
7.4 Hoses
The connection between pump power pack and cutter unit is normally effected with
LUKAS hoses. If pipes are to be used, please contact LUKAS.
7.5 Control of movements in operation
7.5.1 LSI 600
(device without valve for externally controlled operation)
For hydraulic connection two extra hoses are required (hoses to be ordered separately).
The hoses are to be mounted to the pressure ports in the cylinder bottom and to be
tightened with a torque of 45 Nm. When fitting the cutter unit to a manipulator, certain
principles must be absolutely observed to avoid any risk for persons and the device:
- The device must be fitted swivelling around its longitudinal axis (made possible by
means of an axis of rotation on the robot or an adequate rotor sleeve / LUKAS special
accessories) so that before the cutting operation it can adjust itself at a right angle
to the object to be cut.
- Safety covers and/or measures for safety shut-off must be ensured.
Important!
Before putting the device into operation, mounting must be agreed with LUKAS from
the engineering and safety points of view in all cases.
7.5.2 LSI 600 E and 400 E
(Device with switch actuation for manual operation and manual control)
These devices are operated electrically. The electric connection cable has the same
length as the two hoses.
8
Connection of the devices
8.1 Hydraulic (LSI 600)
In the cylinder bottom can be screwed in 2 LUKAS hydraulic hoses in any desired length.
8.2 Hydraulic (LSI 600E and LSI 400E)
Two hoses (each 0.5 m long) are fitted to the device; they are connected with the pump
power pack via a hose pair (5 m / 10 m / 20 m, as is necessary). All hoses are colour
marked and have rapid action couplings so that they can be connected without the risk
of mix-up:
HP = High pressure ——> red,
R = reflux ——> blue.
Summary of Contents for LSI 400
Page 24: ...3 c xI z1 1 9 I _ I...
Page 25: ...Opening Hydraulic cylinder Culling...
Page 26: ...Hydraulic diagram T A...