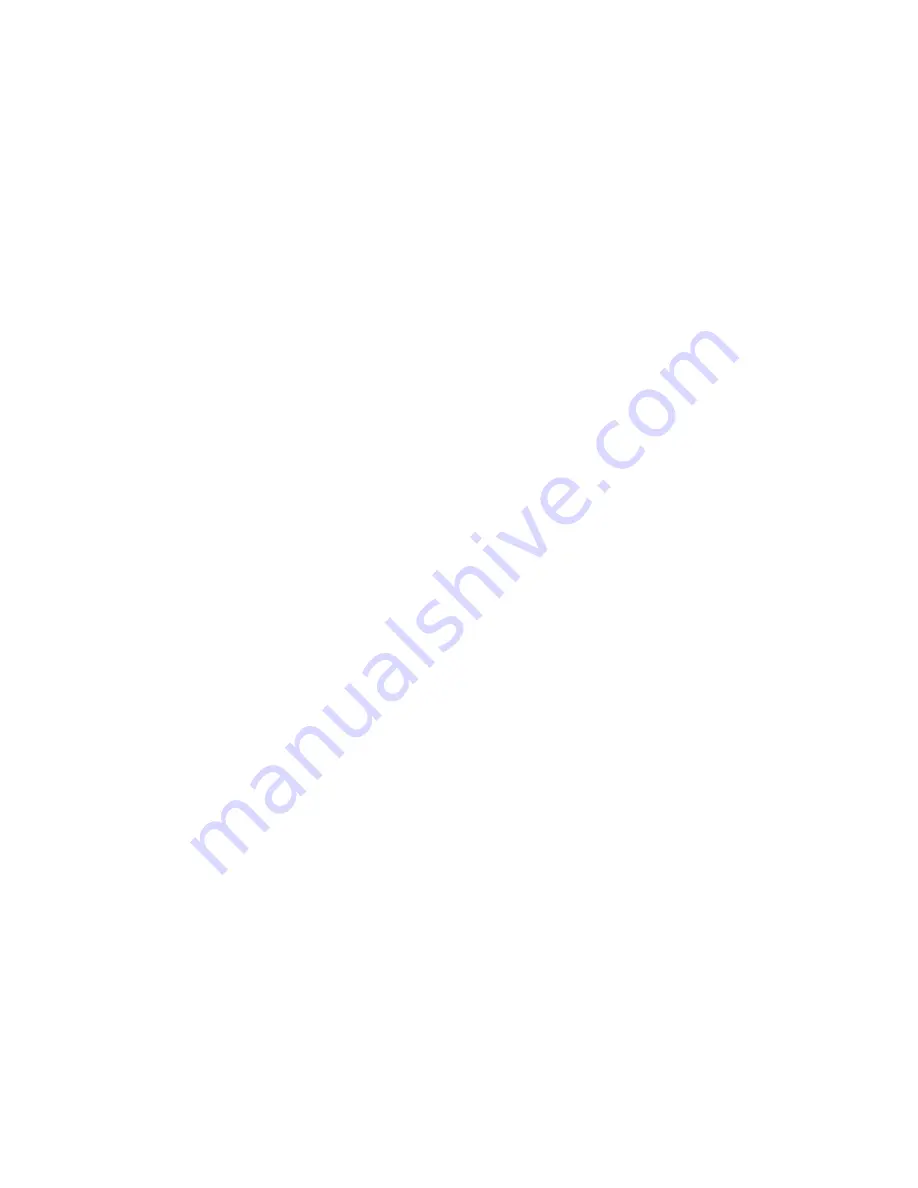
2
Content
Page
1
Correct use of the device
3
2
Organisational measures
3
3
General safety instructions
4
4
Maintenance and servicing instructions
5
5
Safety instructions for hose lines
6
6
Functions and performance
8
7
Connecting the device
9
8
Operation
11
9
Cutting
13
10
Dismantling of the device / switching off after use
14
11
Maintenance
14
12
Repairs
15
13
Troubleshooting
19
14
Technical data
20