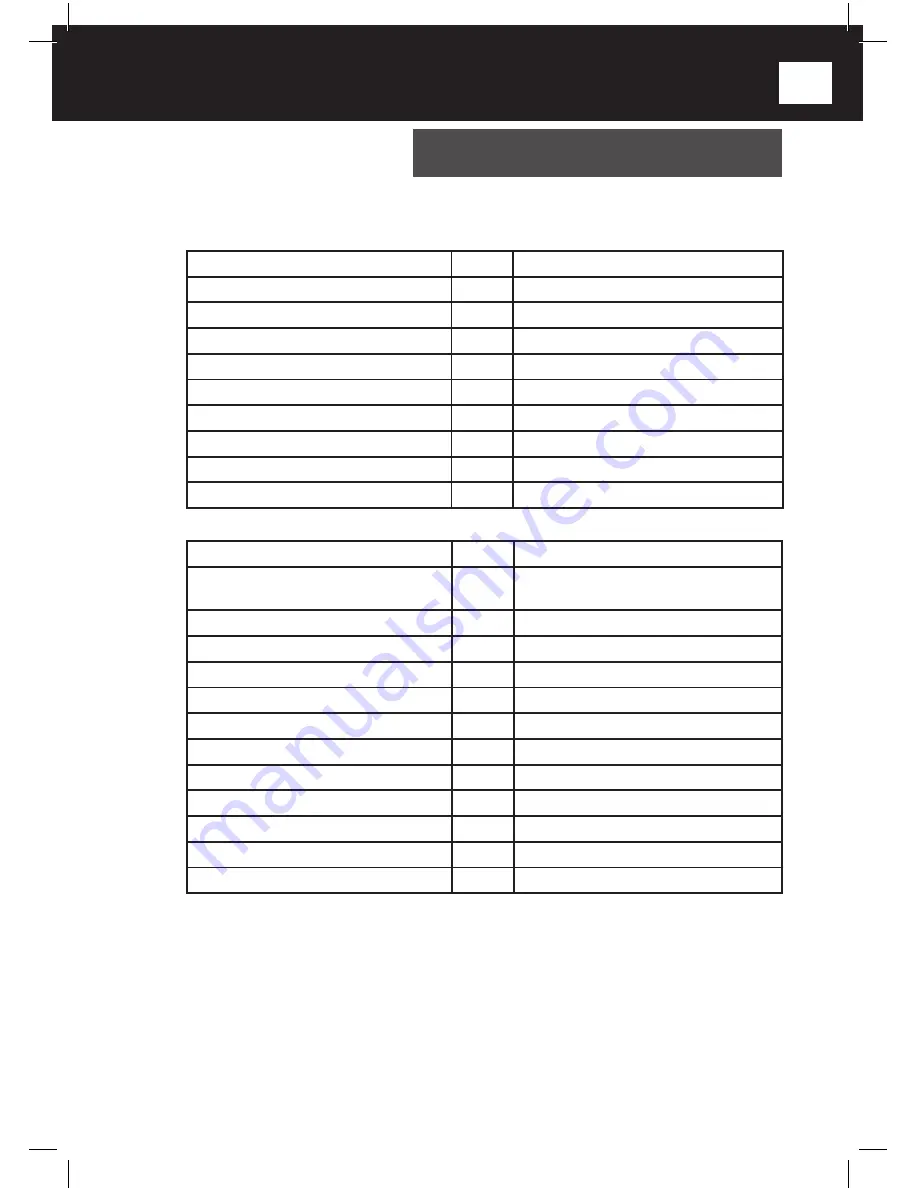
5
D
TECHNICAL SPECIFIKATIONS
10. TECHNICAL SPECIFIKATIONS
Model:
RP-110HP
Motor:
1-Cylinder 4-stroke-OHV petrol motor
Power:
kW
4,8
Rotation speed:
1/min
3600
Fuel:
Non-lead normal petrol
Tank volume:
l
3,6
Motor oil:
SAE 10W-30 oder 10W-40
Oil volume:
l
~ 0,6
Spark plug:
FTC
or equivalent
Spark gap:
mm
0,7- 0,8
Compactor plate (L x B):
mm
570 x 440
Total measurements incl.
Steering shackle (L x B x H):
mm
1080 x 440 x 940
Compacting frequency:
Hz
0
Centrifugal force:
kN
15
Compacting depth:
cm
30
Surface capacity:
m²/h
416,1
Max. Working speed:
m/min
19,5
Vibration bounces/min:
VPM
400
Max. allowed tilt angel for the motor:
Grad
0°
Weight (net / gross):
kg
5
Hand/arm vibrations:
m/s
18,55
Noise level –pressure LPA:
dB(A)
96,6
Noise level –power LWA:
dB(A)
106,79
Stated specifications are typical values and cannot be regarded as granted threshold limit values on-
site. Even if there is a correlation between the values, it cannot be presupposed that further steps for
protection may not be required on the working site. Further conditions on the working site which affects
the situation could be the actual working space, further noise sources like the number of tools and
machinery and further activities. The limit values may also deviate from country to country. It is up to the
user to consider and take measures to eliminate such risks.
GB
RP-110HP_manual_GB.indd 25
04.02.2010 09:23:05
Summary of Contents for RP-110HP
Page 4: ...4 6 7 8 5 5 4 9 1 3 4 RP 110HP_manual_GB indd 4 04 02 2010 09 22 48...
Page 5: ...5 9 10 2 4 11 12 9 1 13 5 RP 110HP_manual_GB indd 5 04 02 2010 09 22 48...
Page 28: ...28 13 PARTS INCLUDED Motor unit PARTS INCLUDED RP 110HP_manual_GB indd 28 04 02 2010 09 23 05...
Page 29: ...29 GB Agitator PARTS INCLUDED RP 110HP_manual_GB indd 29 04 02 2010 09 23 05...
Page 31: ...31 GB RP 110HP_manual_GB indd 31 04 02 2010 09 23 06...