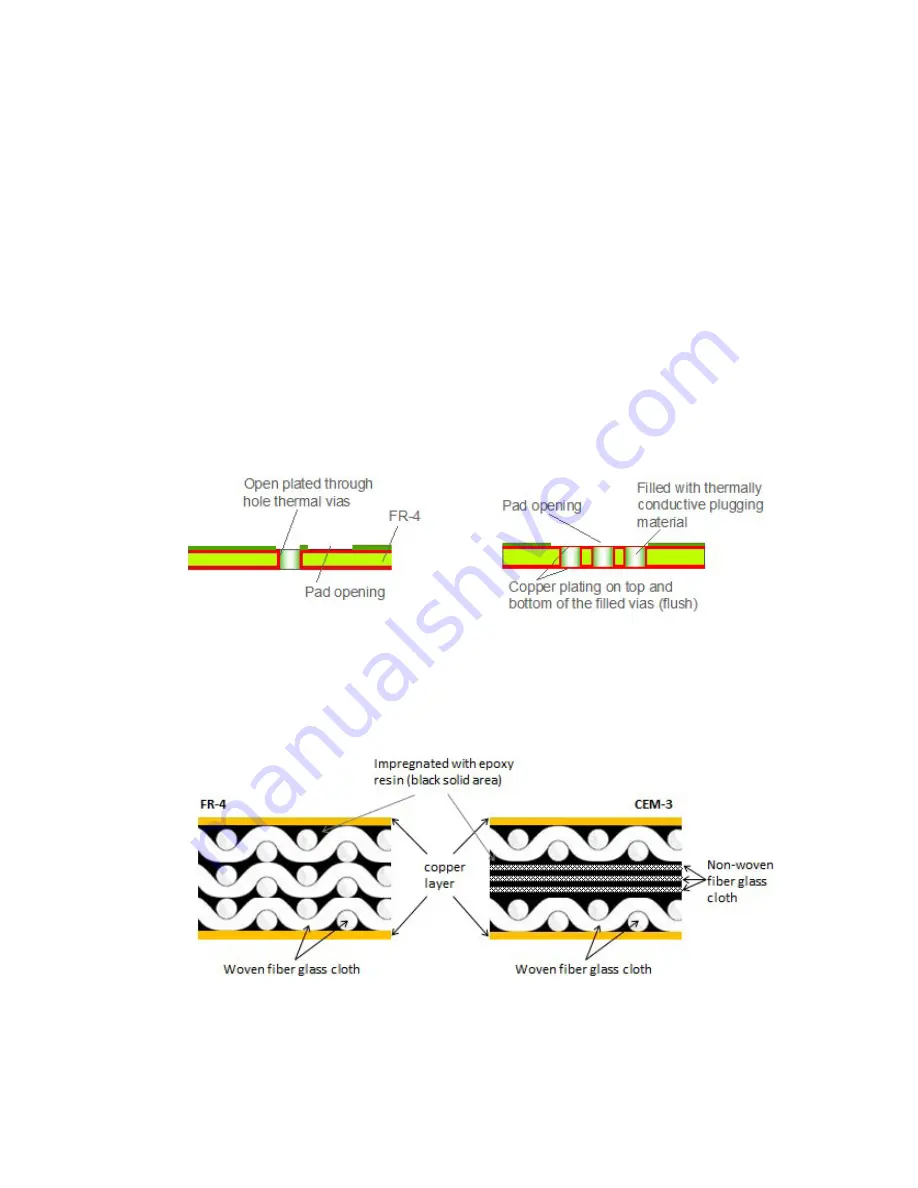
AB217 LUXEON HR30 Application Brief 20160504 ©2016 Lumileds Holding B.V. All rights reserved.
6
FR-4/CEM-3 PCB
FR-4/CEM-3 board construction consists of the following layers (Figure 5):
• FR-4 (woven fiber glass fabrics reinforced epoxy laminate, Figure 6 ) sheet or CEM-3 (composite epoxy material
constructed from both woven and non-woven fiber glass fabrics, Figure 6). These two materials have excellent
electrical insulation properties but have very poor thermal conductivity. Between these two, CEM-3 thermal
conductivity is generally better than FR-4. For detail specifications of PCB, refer to a standard generated by Association
Connecting Electronics Industries, (
), IPC-4101C “Specification for Base Materials for Rigid and Multilayer
Printed Boards” standard.
• Top and bottom copper layers. To improve thermal performance, adding thermal vias will help but may require an
electrically insulting thermal interface material (TIM) between an FR-4 and the heat-sink to ensure that the PCB system
can meet a minimum high potential (hipot – electrical insulation barrier) test and to prevent potential device shorting
over time due to breakdown of the TIM material. Two common approaches include:
– (i) Open vias with plated through holes (Figure 5)
– (ii) Filled and capped thermal vias (Figure 5).
The filled and capped design gives better thermal performance than open via design but at a much higher
manufacturing cost and require good surface co-planarity for small package. The diameter of the via, position and
the quantity need to be studied to find optimum thermal performance at acceptable cost.
• Use of white solder mask.
Figure 5. Left picture shows a cross section of an open via with plated through hole design with one pad opening where the
LED pad is soldered onto. Right picture shows a cross section of a filled and cap via design with one pad opening. One of the
LED pads is then soldered on top of the flush area where the filled and capped vias are underneath it to create direct thermal
path connection between LED and bottom of PCB.
Figure 6. Cross section of a FR-4 and CEM-3 PCBs. Not drawn to scale; for illustration purposes only.