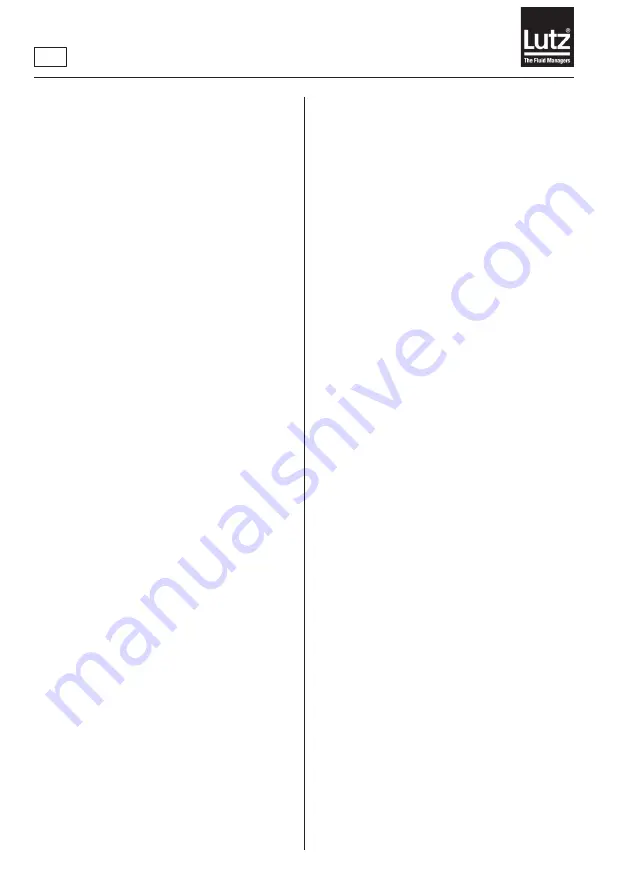
10
0698-825 MD1xL / MD2xL - 06/2021
en
• Use maintenance units (3) consisting of air filter
and oiler. The oiler is not necessary for motors
MD1xL and MD2xL, but is recommended for
longer service life. The motor power is 10-20%
lower with non lubricated air than with lubricated
air.
• Install the maintenance unit with an air connec-
tion of at least G 1/4 in the immediate vicinity of
the compressed air motor (1). Use a resin-free
and acid-free mineral oil with a viscosity of 20 to
30 cSt (20 to 30 mm²/s) in the oiler (3). The oil
consumption should be 1 drop per minute as a
minimum.
• The air filter (3) requires regular maintenance
during which the trapped condensation water
is drained and the filter is cleaned.
• The compressed air motor will achieve maximum
performance at 87 psi (6 bar). The pressure in
the pneumatic system exceeding 87 psi (6 bar),
a pressure regulator (3) must be installed. Ad
-
justment of the pressure regulator (3) must be
effected with the motor running.
• Install an air hose (2) of 1/2” (13 mm) inside
diameter between maintenance unit and com-
pressed air motor to minimize the pressure
losses.
• Use a stop valve in the pressure line in order
to connect and disconnect the motor without
pressure.
• Note the resulting pressure loss when using
quick-action couplings.
Recommendation for compressed air supply
• The classification of the compressed air quality
can be taken from ISO 8573-1: 2010.
• Standard values of compressed air quality are
e.g. to be found in VDMA 15390-1: 2014-12.
• For lubricated air, a minimum compressed air
quality by ISO 8573-1: 2010 [-: 4: 4] is recom-
mended.
• For non lubricated air, a minimum compressed
air quality by ISO 8573-1: 2010 [6 3: 3] is recom-
mended.
• Excessive water content in the compressed air can
cause freezing of the water particles. This may be
the cause for damaging the vanes or clogging the
muffler, which may affect the performance of the
motor.
4.2 Assembly of pump tube to the
motor
3
Motor is switched off
►
Connect the motor with the pump tube.
►
Turn the motor slightly to ensure that the
driver (
→
Fig. 2, Item 1) engages in the
coupling
(
→
Fig. 2, Item 2).
►
Firmly connect the motor and pump tube by
means of the handwheel (right-hand thread)
(
→
Fig. 2).