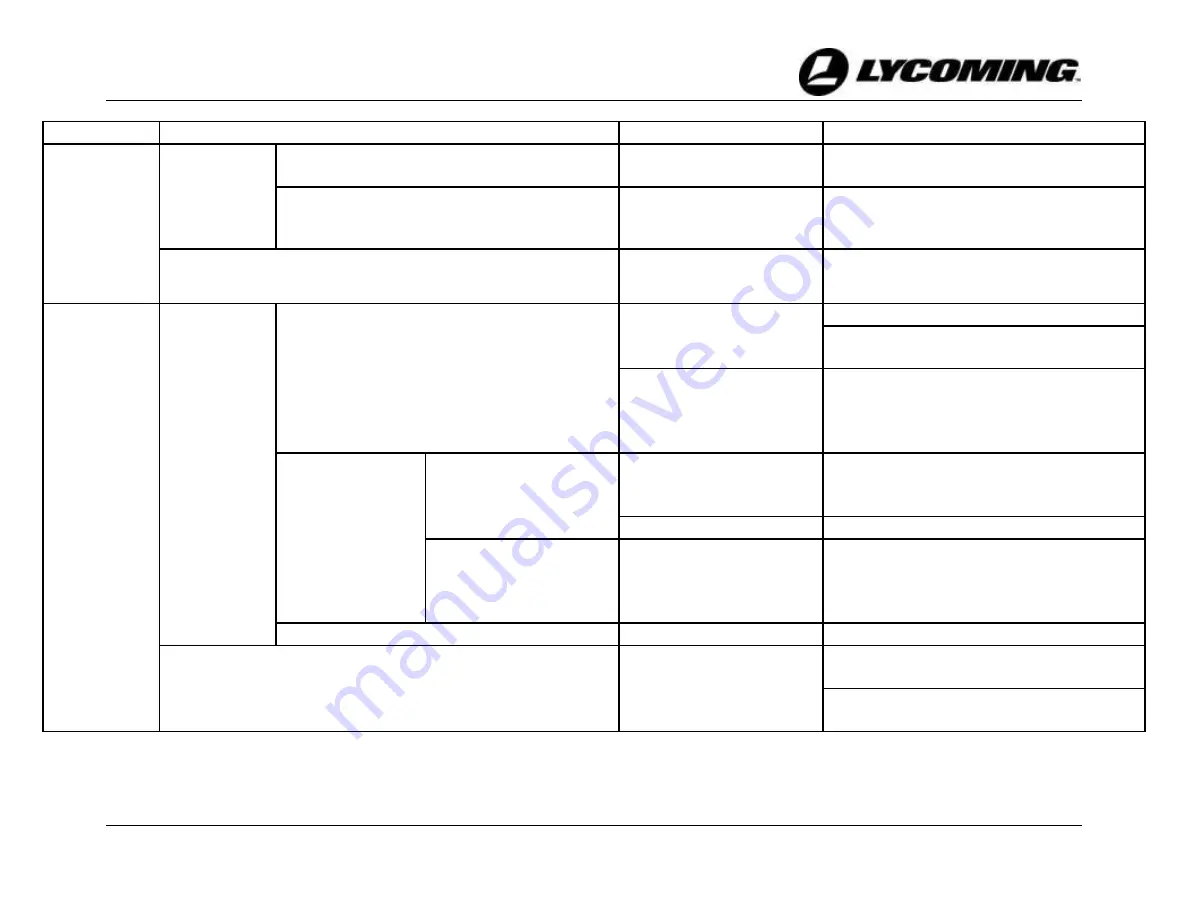
IO-390-D Series Engine Maintenance Manual
© 2020 Avco Corporation. All Rights Reserved
12-30
March 2020
Page 99
IO-390-D Series Engine Maintenance Manual
Problem
Problem Isolation
Probable Cause
Corrective Action
Engine runs
rough (Cont.)
Isolate EIS
ignition
causing
roughness
(Cont.)
Unable to verify ignition correctly timed to
engine #1 cylinder TDC
Ignition not timed to
engine correctly
Reinstall ignition unit in accordance with
installation instructions
LED blinks rapidly (12 times per second)
Internal ignition fault
Contact Lycoming customer support
Roughness caused by magneto or ignition other than EIS
Magneto problem
Contact magneto manufacturer
Engine will
not start,
kicks back
during start
or does not
run on EIS
Power
measured
(8.5 to
30VDC) at
power
terminal
P-lead terminal grounded
P-lead wire is connected
to ground
Check ignition switch
Check integrity of p-lead wire for
chaffing to ground
Internal ignition fault if
p-lead terminal is
grounded with wire
removed
Contact Lycoming customer support
P-lead terminal
not grounded
(open)
Ignition verified as
correctly timed to
engine #1 cylinder TDC
Ignition harness wires
connected to incorrect
spark plugs
Check routing of harness wires
Internal ignition fault
Contact Lycoming customer support
Unable to verify
ignition correctly timed
to engine #1 cylinder
TDC
Ignition not timed to
engine correctly
Reinstall ignition unit in accordance with
installation instructions
LED blinks rapidly (12 times per second)
Internal ignition fault
Contact Lycoming customer support
Unable measure power (8.5 to 30VDC) at power terminal
No power to ignition unit
Verify ignition power wire is connected to
power source
Check ignition power wire integrity,
terminals & fuse