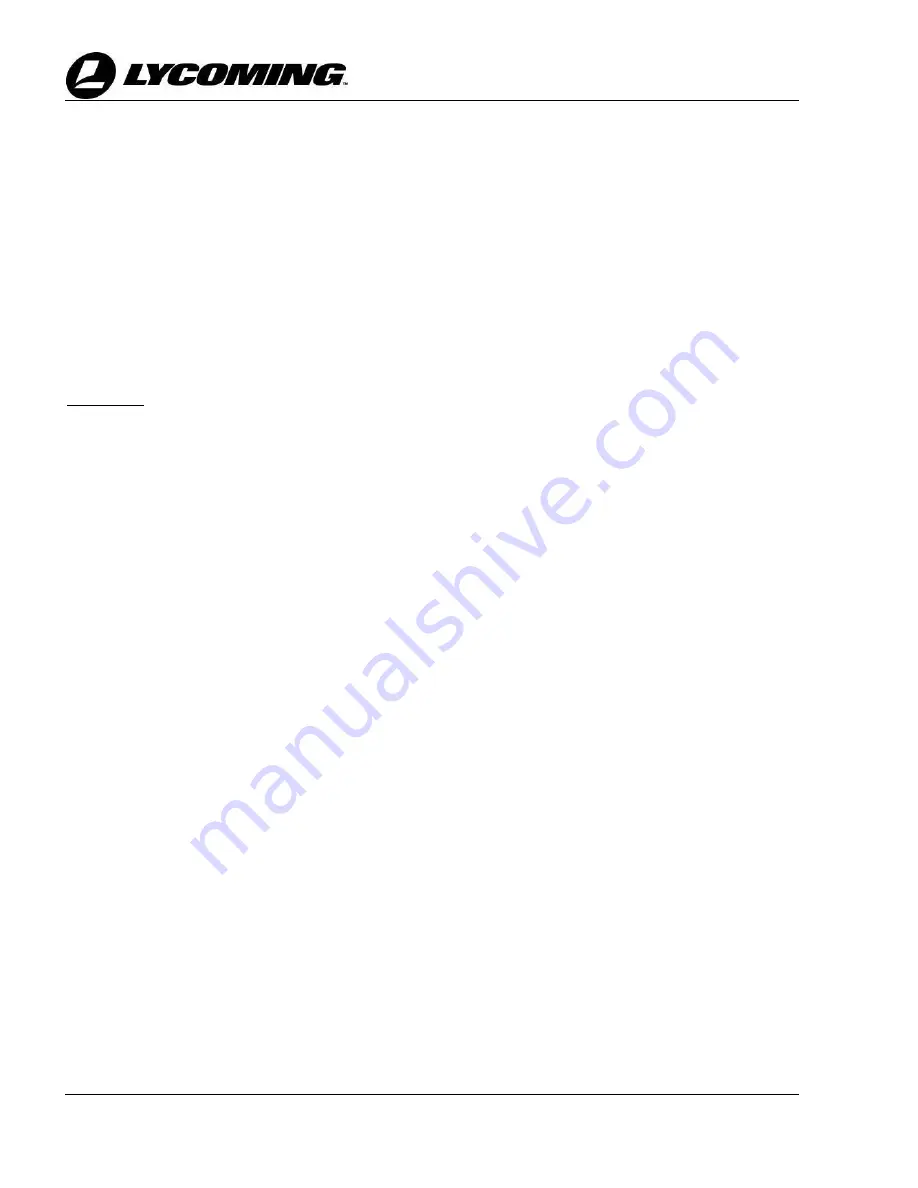
Theory of Operation
© 2018 Avco Corporation. All Rights Reserved
Page 18
October 2018
TEO-540-A1A Engine Installation and Operation Manual
Engine Overhaul vs. Engine Rebuild
Engine overhaul is different from engine rebuild as follows:
1.
Engine overhaul – The engine is completely disassembled and assembled with parts and
components that have been inspected to be within serviceable limits. After an engine overhaul,
the engine is returned to service and the engine operating hours continue without interruption as
recorded in the engine logbook.
2.
Engine rebuild - The engine is completely disassembled and assembled with parts and
components that have been inspected to new limits. An engine rebuild is only completed at the
Lycoming Engines’ factory. After an engine rebuild, the engine is issued a zero-time logbook.
Timekeeping
The EECS records the amount of time the controller has power (as "EECS Hours").
NOTICE:
The total recorded hours cannot be reset. This time is just a continuous counter until the
unit is out of service and is reset during a factory engine rebuild.