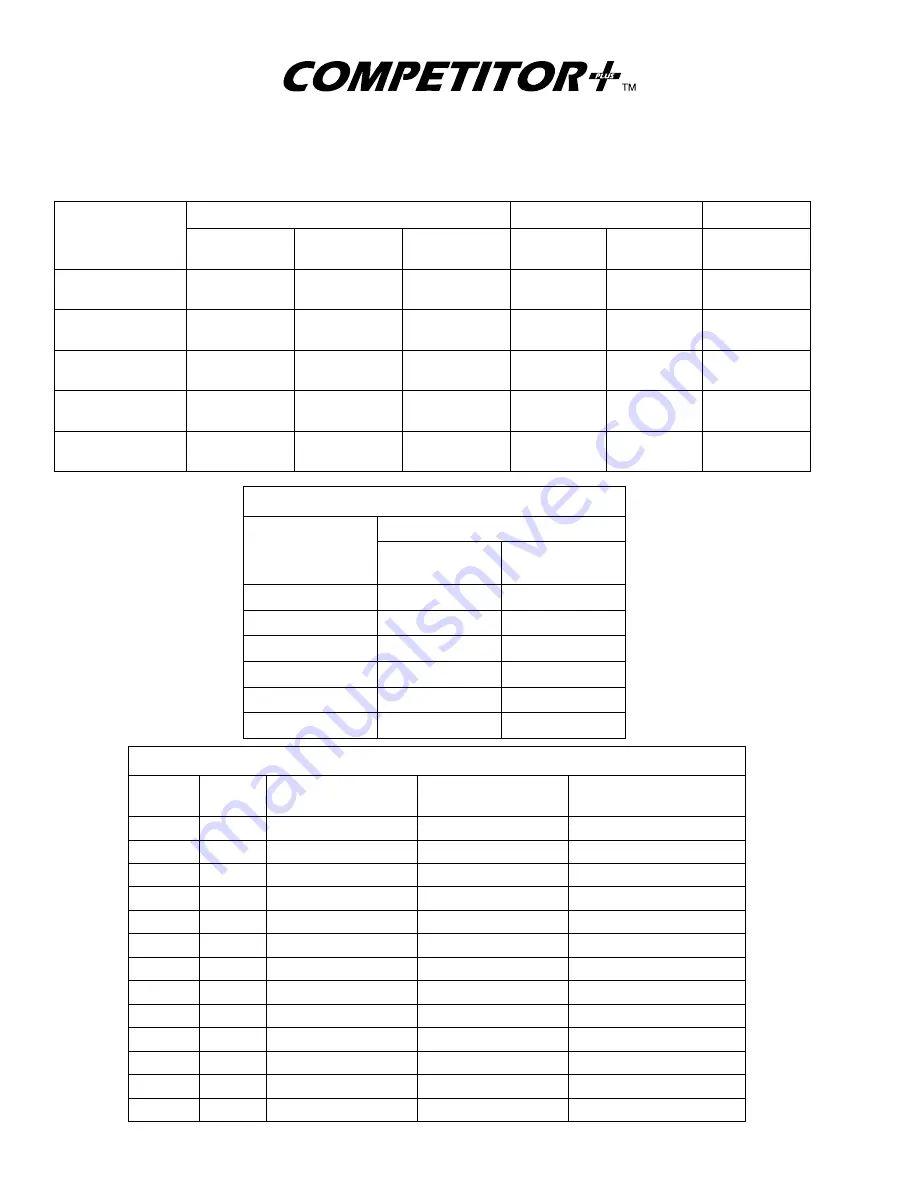
MAINTENANCE AND SERVICE SPECIFICATIONS SHEET
ASSEMBLY CLEARANCES
Metric values (mm) are shown in parentheses ( )
All other values are in inches
LOBES
TO END
PLATES
LOBE TO CASING
INTERLOBE
MODEL
TOTAL
(MIN./MAX.)
DRIVE END
(MINIMUM)
GEAR END
(MINIMUM)
MINIMUM
MAXIMUM
MININUM
2002, 2004
.005” / .010”
(.13 / .25)
.003”
(.08)
.002”
(.05)
.004”
(.10)
.008”
(.20)
.006”
(.15)
3003, 3006
.005” / .010”
(.13 / .25)
.003”
(.08)
.002”
(.05)
.004”
(.10)
.008”
(.20)
.008”
(.20)
4002, 4005,4007
.007” / .012”
(.18 / .30)
.004”
(.10)
.003”
(.08)
.005”
(.13)
.009”
(.23)
.010”
(.25)
5003, 5006, 5009
.007” / .012”
(.18 / .30)
.004”
(.10)
.003”
(.08)
.005”
(.13)
.009”
(.23)
.012”
(.30)
6005, 6008, 6015
.011” / .015”
(.28 / .38)
.008”
(.20)
.003”
(.08)
.006”
(.15)
.010”
(.25)
.010”
(.25)
MODEL
FLUID OUNCES (LITERS)
HORIZONTAL
FLOW
VERTICAL
FLOW
2002, 2004
3.5 (.10)
6.0 (.18)
3003, 3006
6.0 (.18)
16.0 (.47)
4002, 4005, 4007
7.0 (.21)
22.8 (.67)
5003, 5006, 5009
16.0 (.47)
27.6 (.82)
6005, 6008, 6015
28.0 (.83)
52.0 (1.54)
MODEL
RPM
PRESSURE
PSI (mbar)
VACUUM
in. Hg (mbar)
TEMPERATURE RISE
F
o
(C
o
)
2002
5275
12 (825)
14 (475)
225 (125)
2004
5275
7 (480)
14 (475)
185 (103)
3003
3600
12 (825)
14 (475)
170 (94)
3006
3600
7 (480)
14 (475)
115 (64)
4002
3600
15 (1035)
14 (475)
240 (133)
4005
3600
10 (690)
14 (475)
170 (94)
4007
3600
7 (480)
14 (475)
130 (72)
5003
2850
15 (1035)
14 (475)
195 (108)
5006
2850
10 (690)
14 (475)
180 (100)
5009
2850
7 (480)
14 (475)
115 (64)
6005
2350
15 (1035)
16 (540)
250 (139)
6008
2350
12 (827)
16 (540)
240 (133)
6015
2350
6 (415)
12 (410)
130 (72)
14
OIL RESERVOIR CAPACITIES
MAXIMUM OPERATING LIMITS
Summary of Contents for COMPETITOR PLUS 2002
Page 20: ...NOTES...