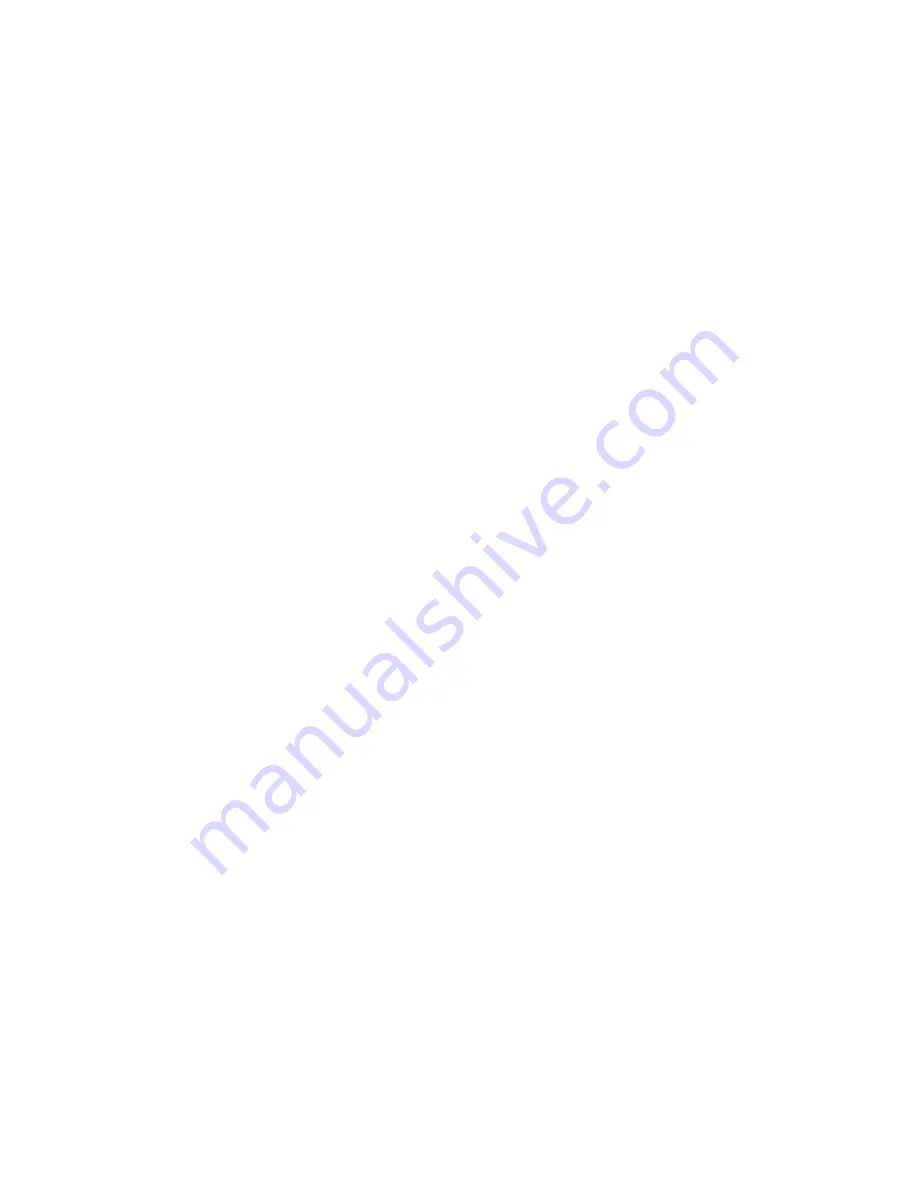
INSTALLATION
WARNING:
Customers are cautioned to provide adequate protection, warning and safety equipment necessary to
protect personnel against hazards involved in the installation and operation of this equipment in the system or facility.
Do not use air blowers on explosive or hazardous gases. Casing pressure must not exceed 25 PSIG (1.72 bar g). Each
size blower has limits on pressure differential, running speed, and discharge temperature, which
must not
be exceeded.
These limits are shown on the Specification Sheet "Maximum Operating Limits".
LOCATION
Install the blower in a clean, dry, well lighted area if possible. Leave plenty of room around the blower for inspection and
maintenance.
FOUNDATION
We recommend a solid foundation be provided for permanent installation. It is necessary that a suitable base be used,
such as a steel combination base under blower and motor, or a separate sole plate under each.
Before tightening the bolts, check to see that both mounting feet are resting evenly on the foundation, shim as necessary
to eliminate stress on the base when the bolts are tightened.
Where a solid foundation is not feasible, care must be taken to insure that equipment is firmly anchored to adequate
structural members.
DRIVE
When the blower is V-belt driven the sheaves must be positioned so that the hub face of the blower sheave is not more
than 1/4" (6.5 mm) from the blower drive end plate and the driver sheave is as close to the driver bearing as possible.
Care should be taken when installing sheave onto shaft. The faces of the sheaves should be accurately in line to
minimize belt wear.
Adjust the belt tension to the belt manufacturer’s specifications.
For installations where the blower is to be operated by direct drive, selection of the driver should be such as not to
exceed the maximum speed ratings of the blower. (See Specification Sheet "Maximum Operating Limits.)
A flexible type coupling should be used to connect driver and blower shafts. The two shafts must be aligned within .005"
(.13 mm) T.I.R. (Total Indicated Runout)
PROTECTIVE MATERIALS
Remove protective materials from the shaft.
Remove the protective covers from the inlet and outlet ports and inspect the interior for dirt and foreign material.
WARNING:
Keep hands, feet, foreign objects and loose clothes from inlet and outlet openings to avoid injury or
damage if lobes are to be rotated at this point.
LUBRICATION
Do not start up the blower until you are positive that it has been properly and fully lubricated. (See Lubrication Section.)
PIPING
Inlet and outlet connections on all blowers are large enough to handle maximum volume with minimum friction loss.
Maintain same diameter piping. Silencers must not be supported by the blower. Bending moments must be avoided.
Be certain all piping is clean internally before connecting to the blower. We recommend placing a 16-mesh wire screen
backed with hardware cloth at or near the inlet connections for the first 50 hours of use until the system is clean. Make
provisions to clean the screen after a few hours of operation and completely discard it once the system is clean, as it will
eventually deteriorate and small pieces going into the blower can cause serious damage. A horizontal or vertical air
flowing piping configuration is easily achieved by rearranging the mounting feet position.
WARNING:
Do not operate equipment without adequate silencing devices since high noise level may cause hearing
damage. (Reference OSHA Standards.)
RELIEF VALVES
We recommend the use of relief valves to protect against excessive pressure or vacuum conditions. These valves
should be tested at initial start-up to be sure they are adjusted to relieve at or below the maximum pressure differential
rating of the blower.
CAUTION:
Upon completion of the installation, and before applying power, rotate the drive shaft by hand. It must move
freely. If it does not, look for uneven mounting, piping strain, excessive belt tension or coupling misalignment or any
other cause for binding.
5
Summary of Contents for COMPETITOR PLUS 2002
Page 20: ...NOTES...