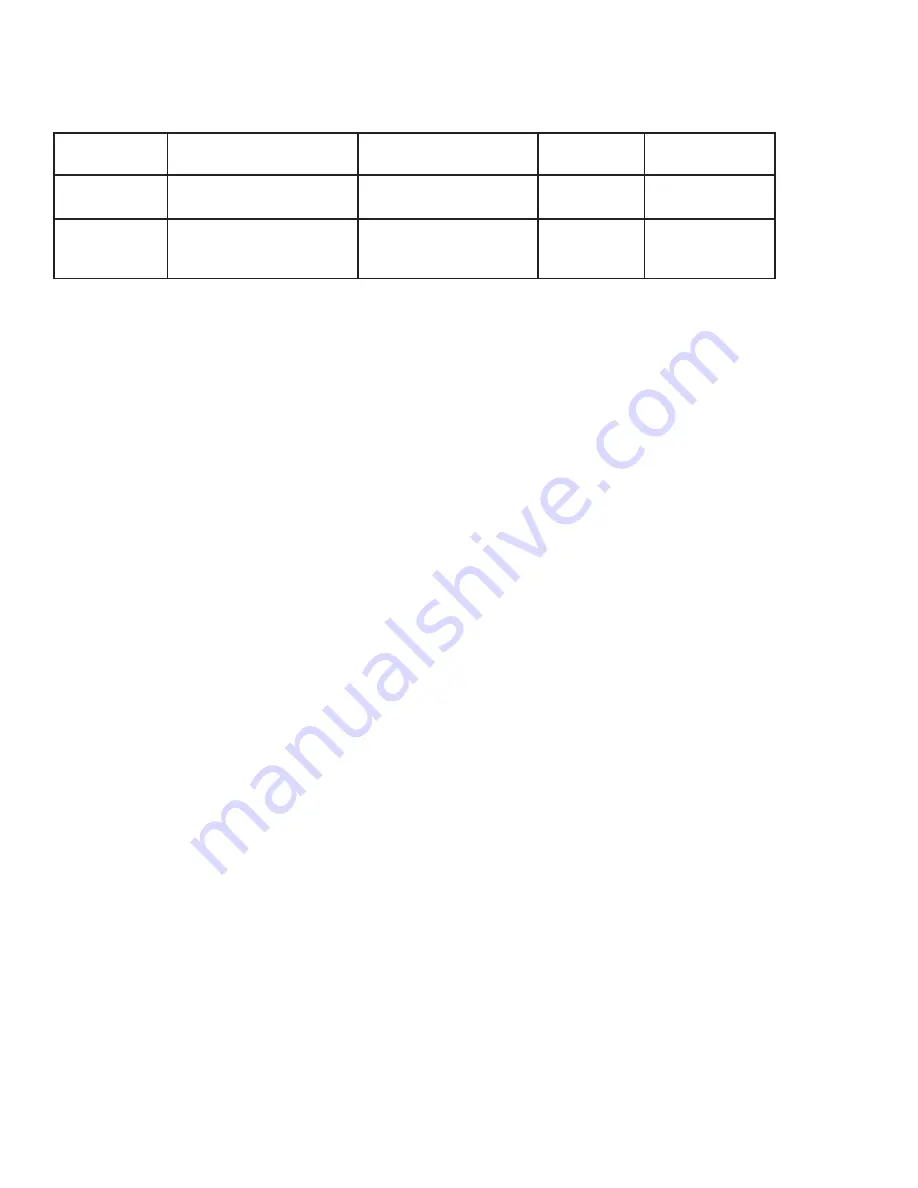
214778
48
Revision A
Table 4.1
Available Ballast Kits for Different Header Types and Configurations (continued)
Header Type
Description
Header Configuration
Initial Rear
Ballast Kit
Additional Rear
Ballast Kits
D145XL
13.7 m (45 ft.) double reel,
double knife, untimed
Transport
1
1
D145XL
13.7 m (45 ft.) double reel,
double knife, untimed
Transport,
Upper cross auger,
Vertical knives
1
1
When the recommended fluid ballast has been added, proceed to
5 Performing Predelivery Checks, page 49
.