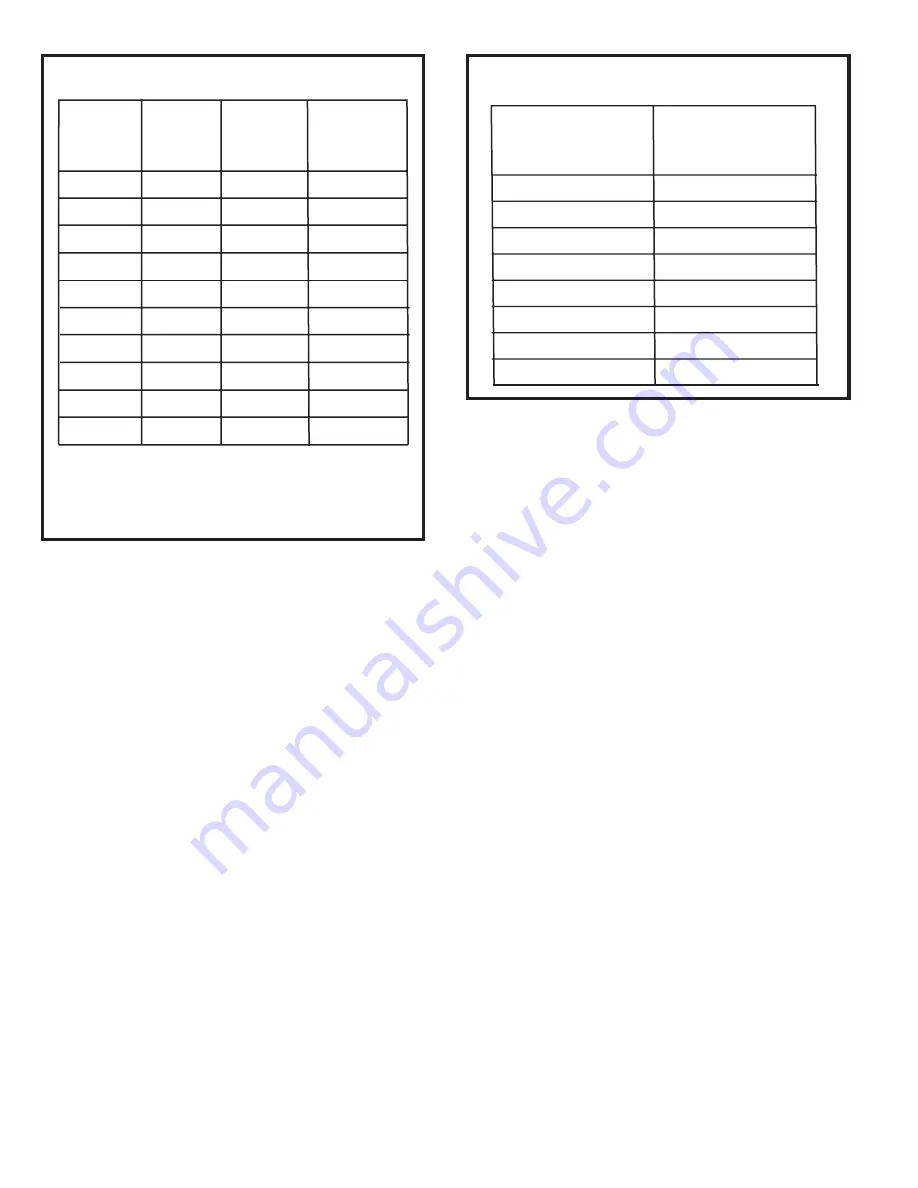
Page 14 of 20
506326-01
Issue 0941
For Propane Gas:
The only check for the furnace rate is to
properly adjust the manifold pressure using a manometer
and the information found in Table 5 on page 14. Typical
manifold set point for installations at altitudes from 0 to 4500'
above sea level is 10.0" W.C.
Adjustments – Cooling Section
No adjustments are required or should be attempted
regarding any of the components of the cooling system. The
system should be checked to see that none of the wiring is
loose or missing.
System Performance
For maximum performance of the cooling system, the
operating temperatures and pressures should be checked
and superheat determined at Standard ARI test conditions
of 82°F outdoor – 80°F indoor dry bulb/67°F wet bulb. If
superheat measured deviates from the values given in Table
6, refrigerant charge should be adjusted accordingly for
maximum performance.
Blower
The unit contains a direct-drive, multispeed blower. The
proper speeds have been preset at the factory for typical
heating and cooling operation. Refer to the wiring diagram
for recommended heating/cooling speeds for specific
models. Speeds may require adjustment due to duct design
and application. Direct-drive blower motors are permanently
lubricated and do not require oiling.
Blower Operation
Continuous operation of the air handling blower will be obtained
if the thermostat fan switch is set to “ON”. With the thermostat
fan switch set to “AUTO”, the air handling blower will cycle
corresponding with the thermostat cycling.
Fan Control
The blower will start approximately 30 seconds after the
burners ignite and will stop approximately 120 seconds after
the thermostat is satisfied. The time delay is preset at the
factory and timing cannot be adjusted.
When the thermostat system switch is set for “COOL”, the
blower will start 5 seconds after the thermostat calls for
cooling and will stop 90 seconds after the thermostat is
satisfied.
A fan switch is provided on the thermostat which will bring
the blower on for continuous operation when the switch is
set for “ON”.
Manifold Pressure vs. Altitude
* Consult local utility for actual heating value.
Furnace Input = Input Factor x Nameplate Input
Above 7500 feet, refer to the National Fuel Gas Code.
Table 5
Altitude
(ft.)
Heating
Value
(Btu/ft.)
Manifold
Pressure
(in. w.c.)
Input
Factor
2000
3000
4000
4500
5000
5500
6000
6500
7000
7500
948
914
881
865
849
833
818
802
787
771
3.50
3.50
3.50
3.50
3.29
3.27
3.25
3.23
3.21
3.19
0.9666
0.9499
0.9332
0.9249
0.8900
0.8790
0.8680
0.8570
0.8460
0.8350
Suction Superheat
Magic-Pak
Model
Suction Superheat
@ AHRI Conditions
82° OD
80° IDDB/67° IDWB
MGE4-09-12
MGE4-09-18
MGE4-09-24
MGE4-09-30
MGE4-10-18
MGE4-10-24
MGE4-10-30
MGE4-09-36
24 - 26° F
21 - 23° F
16 - 18° F
11 - 13° F
22 - 24° F
14 - 16° F
17 - 19° F
27 - 29° F
Table 6