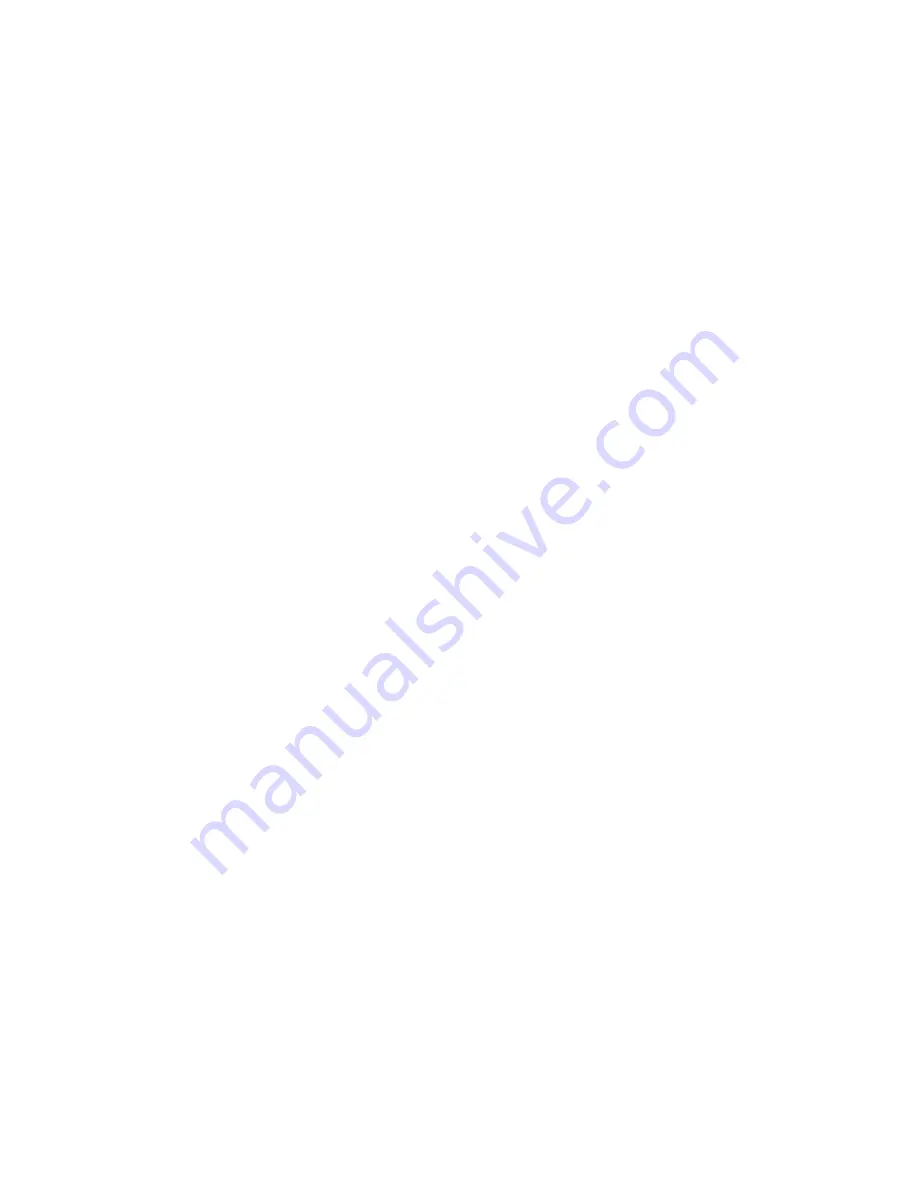
DRIVE SETUP
75
Stop Sequence
1. Select leveling or zero speed reference
– Will cause start of deceleration to new
target speed.
2. When speed becomes less than the
setting of #64, the Low Speed logic
indicator will become active to indicate a
door pre-opening speed. (Output
function ‘F’)
3. Select zero speed – Will cause drive to
decelerate to zero speed & hold car
position. When speed drops below the
setting of #63, the Zero Speed logic
indicator (Output function ‘J or K’) will
become active.
4. Set elevator brake – Wait the
appropriate amount of time for the brake
to drop, or use a brake limit switch to
confirm when the brake is physically
set.... Then
5. Open Hardware Run contact (or Run-Up
or Run-Down contact) – Will cause drive
to stop controlling speed, turn the Run
Engaged logic indicator (Output function
‘C’) off, and ramp armature current
down to zero in time set by function #85.
Drive will open LPR, contactor, & Loop
confirm when Ramp-down is complete.
If contactor confirm fails to open, F402
fault will result.
6. Open Safety Chain (if desired) – Must
remain closed for current ramp-down to
happen. If current ramp-down is not
desired, set #85 to minimum. Expect
some contactor barking. If Safety Chain
opens unexpectedly while drive is
running, F405 fault will result. Safety
chain may remain closed.
7. Open Drive & Field Enable (if desired) –
Will cause field current to go to stand-
by/idle value. May remain active if drive
will be restarted shortly. However, if
drive is not restarted within 5 minutes
with Drive & Field Enable active, F403
fault will result.
Preset Speed Logic Sequence
Binary - The internal pre-set-speed selector
in binary mode (fctn #150 ON) uses 3 input
lines to select 1 of 8 pre-set speeds
(including zero), see Table 11. Binary logic
reduces the number of control lines but the
logic inputs to select those independent
speeds may not be properly de-bounced at
the sending or receiving end. This may allow
an unintended speed to be momentarily
selected. To prevent this from happening,
the user should consider using 4 pre-set
speeds, including zero, selected in a gray
scale progressive manner (only one switch
changes at a time).
Progressive - An alternate method of one-at-
a-time control that has more pre-set speeds
and takes advantage different Ramp Rates
(R-R) during operation, set #150=Off for
Progressive input control, see Table 12.
Connect A1TB1-10 to A1TB1-54, and
A1TB1-51 to A1TB1-12 to automatically
activate R-R 2 with a 1 Floor Run and R-R 3
with Multi-Floor runs. R-R 1 will be activated
for leveling and inspection, speed #1. If
Decel Rate Latch #116 is ON, these rates
will be held active during deceleration.
Summary of Contents for DSD 412
Page 1: ...DSD 412 DC Elevator Drive Technical Manual CS00407 rev 06...
Page 6: ...6...
Page 102: ...MAINTENANCE 102 Figure 24 Connector and E prom Locations...
Page 103: ...MAINTENANCE 103 Figure 25 Test Point Locations...
Page 115: ...OUTLINE DRAWING 100A 115 Figure 26 Drive Chassis Outline DSD 412 100 Amp...
Page 116: ...OUTLINE DRAWING 190A 116 Figure 27 Drive Chassis Outline DSD 412 195 Amp...
Page 117: ...OUTLINE DRAWING 300A 117 Figure 28 Drive Chasis Outline DSD 412 300 Amp...
Page 118: ...LAYOUT DRAWING 100A 118 Figure 29 Layout DSD 412 100 Amp A3 A1 A2 A2 L1 NEG GND L2 L3 POS...
Page 119: ...LAYOUT DRAWING 195A 119 Figure 30 Layout DSD 412 195 Amp A3 A1 A2 A2...
Page 120: ...LAYOUT DRAWING 300A 120 Figure 31 Layout DSD 412 300 Amp A3 A1 A2 A2...
Page 121: ......