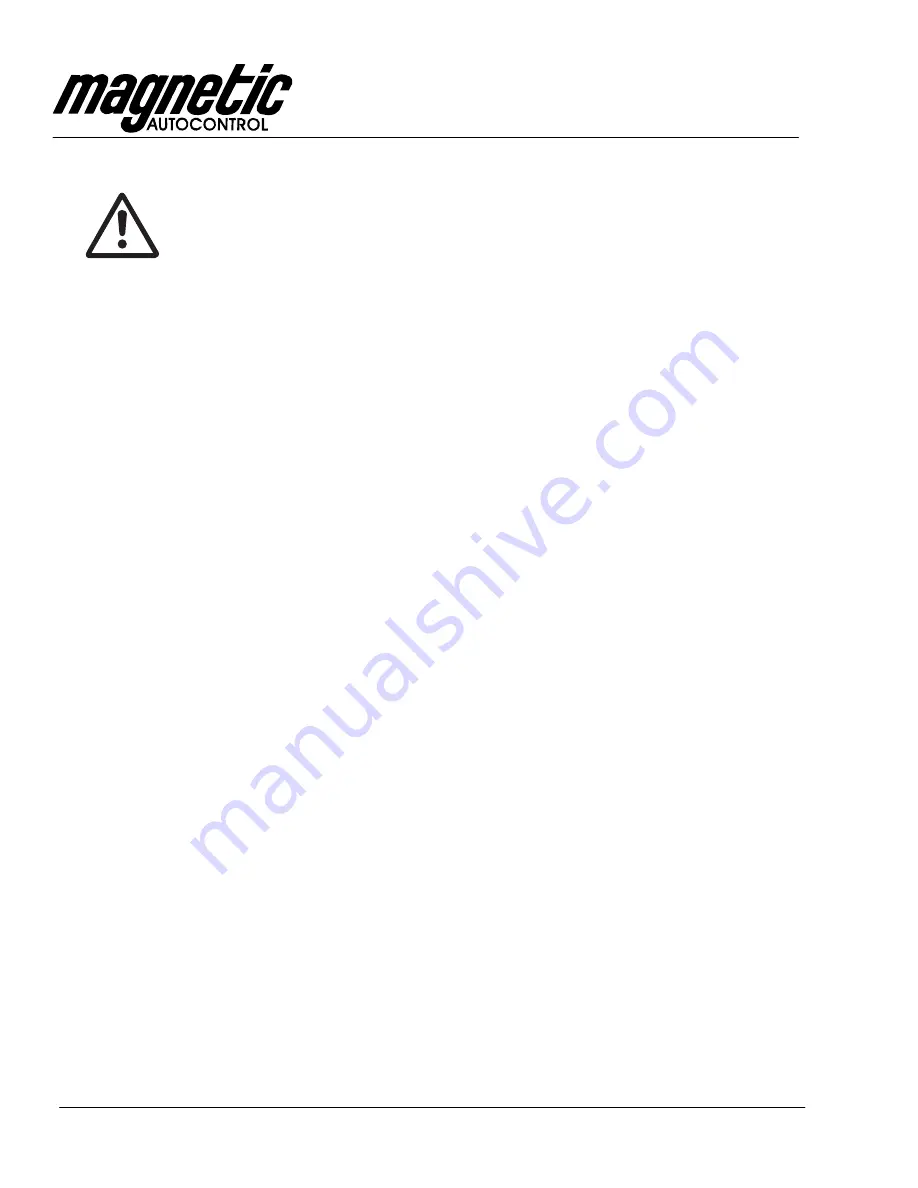
Operating Instructions
581E,5005/6.00
4
1.4 Operational safety
A safe clearance distance of at least 500 mm must be provided between the tip
of the gate arm and the closest solid obstacle (building, wall, fence etc.).
The gate operating elements must be installed at a position from which the gate
can be seen directly.
The motion of the gate arm must be directly observable by the person operating the
gate.
Whilst the gate arm is in motion nobody and no object must be in the immediate
vicinity of the gate.
If the gate and operating elements have been installed in a fixed manner, an all-pole
lockable master switch must be used.
The assembly and installation instructions must be complied with in their entirety.
Any alterations must have received prior confirmation from Magnetic. The gate arm
fixture is designed to withstand wind speeds of up to a maximum of 10 on the
Beaufort scale (= 500 N/m²). If higher wind speeds are expected, a modified gate
arm fixture must be agreed with Magnetic.
All electrical connections, wiring work and exchange of components may only be
performed by appropriately trained electrical technicians.
Before opening, the machines must be disconnected from the mains.
All technical modifications or changes to the barrier system are prohibited.
1.5 Technical developments
The manufacturer reserves the right to modify without prior notice the technical
specifications in order to accommodate the latest technical developments. Magnetic
is happy to provide information on the status of existing operating instructions and
on any alterations and extensions that may be relevant.
1.6 Warranty
Magnetic provides a warranty on its gates that covers all mechanical and electrical
components, but excludes parts subject to wear, for a period of two years from the
date of first use or for a maximum of three years from the date on which the system
was delivered provided that the operating instructions have been complied with, no
unauthorized servicing of machine components has taken place, and that no
mechanical damage to the machines is evident.