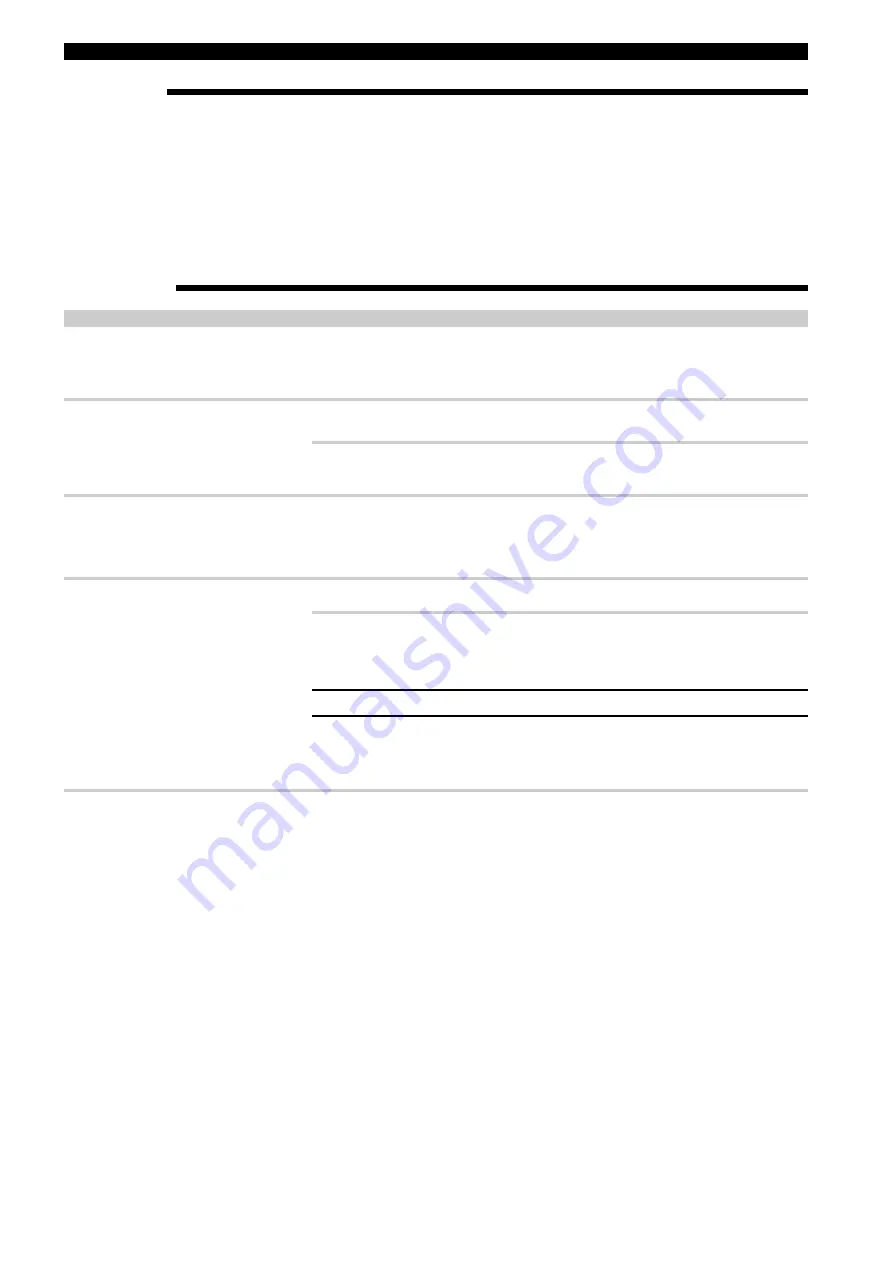
4
MAINTENANCE
Manual Testing
Level Test:
Pressing the “Level Test” pushbutton, will manually test the AS-i output. The level test forces the D2 output and corresponding
LED’s from “1” (wet gap) to “0” (dry gap) data bits or vice versa. The time delay setting is not active during testing.
Fault Test
Pressing the “Fault Test” pushbutton for min 2 s, will manually test the fault output. The fault test simulates a circuit failure and
forces the D3 output to “1” data bits. The time delay setting is not active during testing.
Troubleshooting
Problem
Action/Indication
Solution
No power
No LED’s are ON
Check wiring / input power
Check for malfunction. See below
No change in output between
wet gap / dry gap
Gap may be plugged by
solids / dense foam
Clean the transducer
Gap is out of reach of liquid
Check mounting section on page 2 and
relocate the unit or check blocking
valves.
Chattering output
Excessive aeration / Turbulence
Introduce a time delay
Check input power
Relocate the switch
Fault LED FLASHES
Diagnostic LED is OFF
A system fault has been detected
Check input power
Press «
Level Test
» pushbutton
to identify the problem:
*
--- *
: 1 flash (red LED)
Check wiring between transducer and
electronics or replace transducer.
** --- ** : 2 flashes (red LED)
Replace electronics
*** --- *** : 3 flashes (red LED)
The unit senses excessive noise
interference. Check shield connection or
eliminate interference from a walktie-
talkie, radio, mechanical vibration from a
nearby source
Summary of Contents for ECHOTEL 960
Page 11: ...11 ...