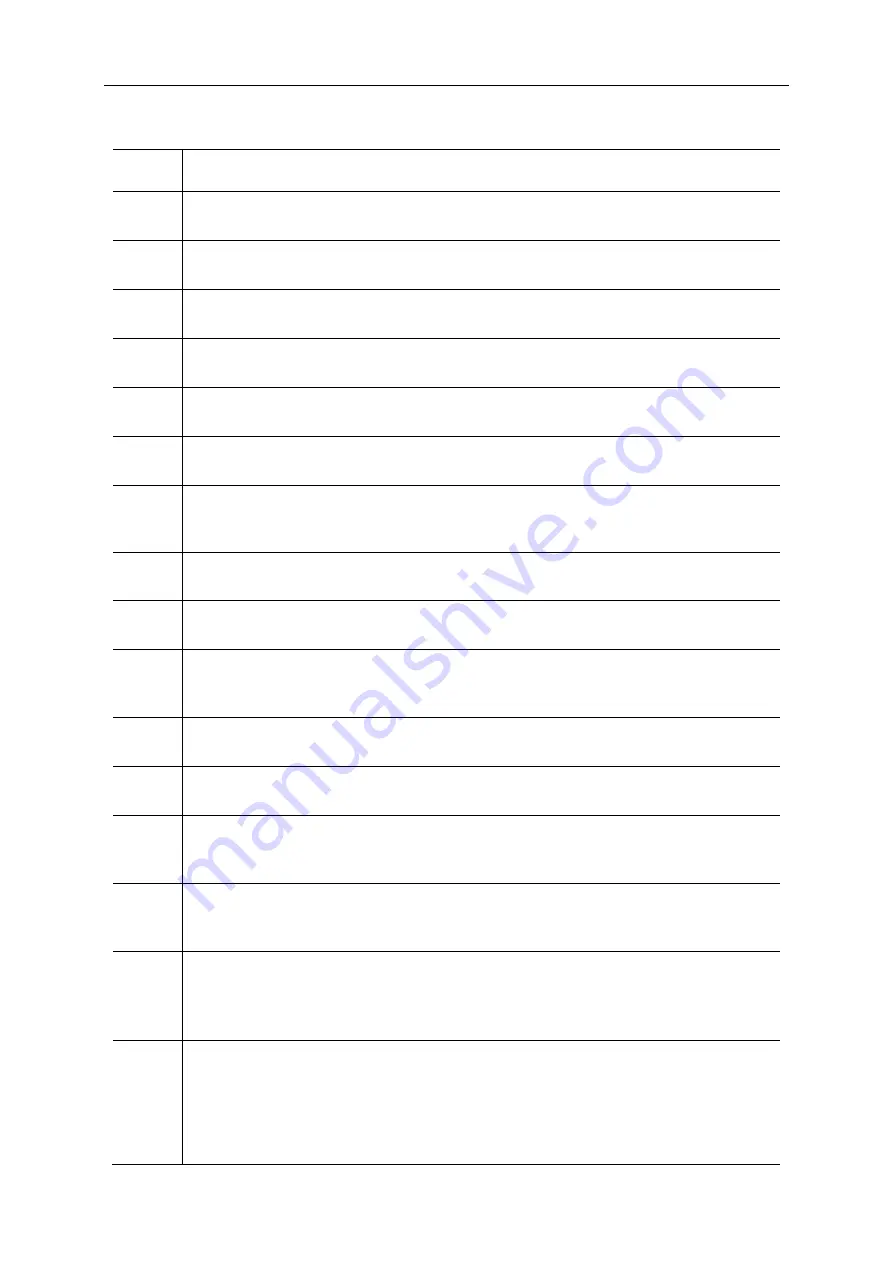
OPERATOR’S MANUAL
with Maintenance Information
Operating Instructions
52
Display Description
55
Lift Down Coil Fault: Check the connections to the Coil’s terminals and make sure
they are tight. If so, check the coil itself to see if it is open or shorted.
56
Right Turn Coil Fault: Check the connections to the Coil’s terminals and make sure
they are tight. If so, check the coil itself to see if it is open or shorted.
57
Left Turn Coil Fault: Check the connections to the Coil’s terminals and make sure
they are tight. If so, check the coil itself to see if it is open or shorted.
58
General Brake Coil Fault: Check the connections to the Coil’s terminals and make
sure they are tight. If so, check the coil itself to see if it is open or shorted.
59
Parallel Coil Fault: Check the connections to the Coil’s terminals and make sure
they are tight. If so, check the coil itself to see if it is open or shorted.
60
Motor Controller Fault: Cycle power. If still needed, try replacing the Motor
Controller.
61
Motor Controller Current Sensor Fault: Drive or Lift Motor may be overheating. Let
the lift cool down. If that does not help, cycle power to reset the Motor controller. If
the problem persists, check the wiring and if OK, try replacing the Motor Controller.
62
Motor Controller Hardware Failsafe Fault: Cycle power. If that does not resolve the
issue check for noise sources. If still needed, try replacing the Motor Controller.
63
Motor Controller Motor Output fault: Check wiring first then cycle power. If needed
replace controller.
64
Motor Controller SRO Fault: Look at motor enable delay with the Dingli Scissor
Programmer, it may be too short. Make sure other Motor Controller parameters are
properly selected.
65
Motor Controller Throttle Fault: Check wiring. Make sure the correct throttle type is
selected in the Motor Controller.
66
Motor Controller Emergency Reverse Fault: Ensure that the Emergency Reverse
Check Parameter is off in the Motor Controller.
67
Motor Controller HPD Fault: Look at motor enable delay with the Dingli Scissor
Programmer, it may be too short. Make sure other Motor Controller parameters are
properly selected.
68
Low Voltage Fault: Check battery voltage and charge batteries if necessary. Check
the battery connections and tighten or clean. Check the voltage to the ECU and
PCU.
69
High Neutral Current: The MC is sensing current in the motors when there should
not be. This could occur anytime the MC thinks the brakes are on and the motors
are still turning. This message sometimes comes just before other faults but should
be ignored in those cases.
70
Steering Input Out of Range: There is an inappropriate voltage at the steering input
of the ZAPI motor controller. The ZAPI may need to be “trained” for the three
steering voltages (on Differential Steered machines). Or the steering voltage from
the ECU was at some point outside of the range that was recorded during the
“training” session. Retrain the controller and/or check for fluctuating voltages due to
lose wires, etc.