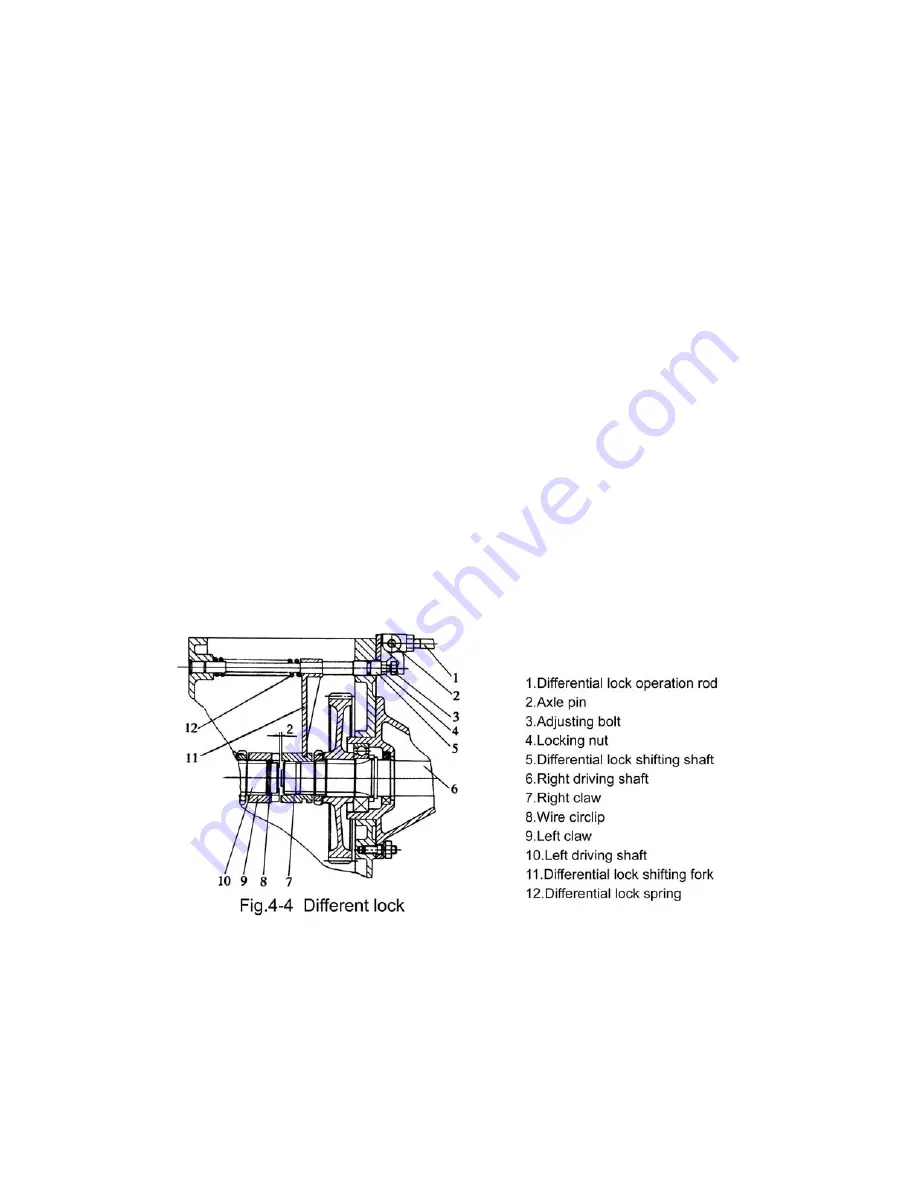
27
c. Adjustment of mesh backlash and mesh print
During adjustment, the bevel gear and pinion axially moving will change both mesh
backlash and mesh print. If the mesh print requirement is contradictory to mesh backlash,
correct mesh print should mainly be ensured, and the adjustment range of mesh backlash can
be enlarged (Especially when the gear and bearing wears and the readjustment is needed, the
backlash can be enlarged). But the mesh backlash should be not less than 0.1mm.
During normal operation of the tractor, the normal mesh backlash and mesh point will
both change, under this condition, so long as teeth faces contact is normal, only the mesh
backlash increases, and this increase of backlash due to gear wear need not be adjusted. But
after the overhaul of the tractor or when replacing a new pair of main drive gears or bevel
bearing, the mesh print and backlash should be ensured at the same time by careful
adjustment.
Note: As the bevel pinion and the bevel gear are a pair of matched gears, be sure not to
make pairs in disorder. The spiral bevel gears should be replaced together with the bearings,
if possible. Otherwise, it will affect their service life.
3. Adjustment of differential lock
The differential lock can be adjusted through bolt (3) and nut (4). During adjusting,
the gap between left claw (9) and right claw (7) should be about 2mm. Screw in or out the bolt
(3) to increase or reduce the gap. After the adjustment has been done, use nut (4) to tighten
bolt (3). (Fig.4-4)
Summary of Contents for JINMA-200
Page 14: ...9 Fig 2 1 Controls and Instruments ...
Page 41: ...36 ...
Page 47: ...42 ...
Page 66: ...61 3 Distribution diagram of rolling bearing and transmission system of Jm series tractors ...
Page 67: ...62 ...
Page 71: ...66 ...