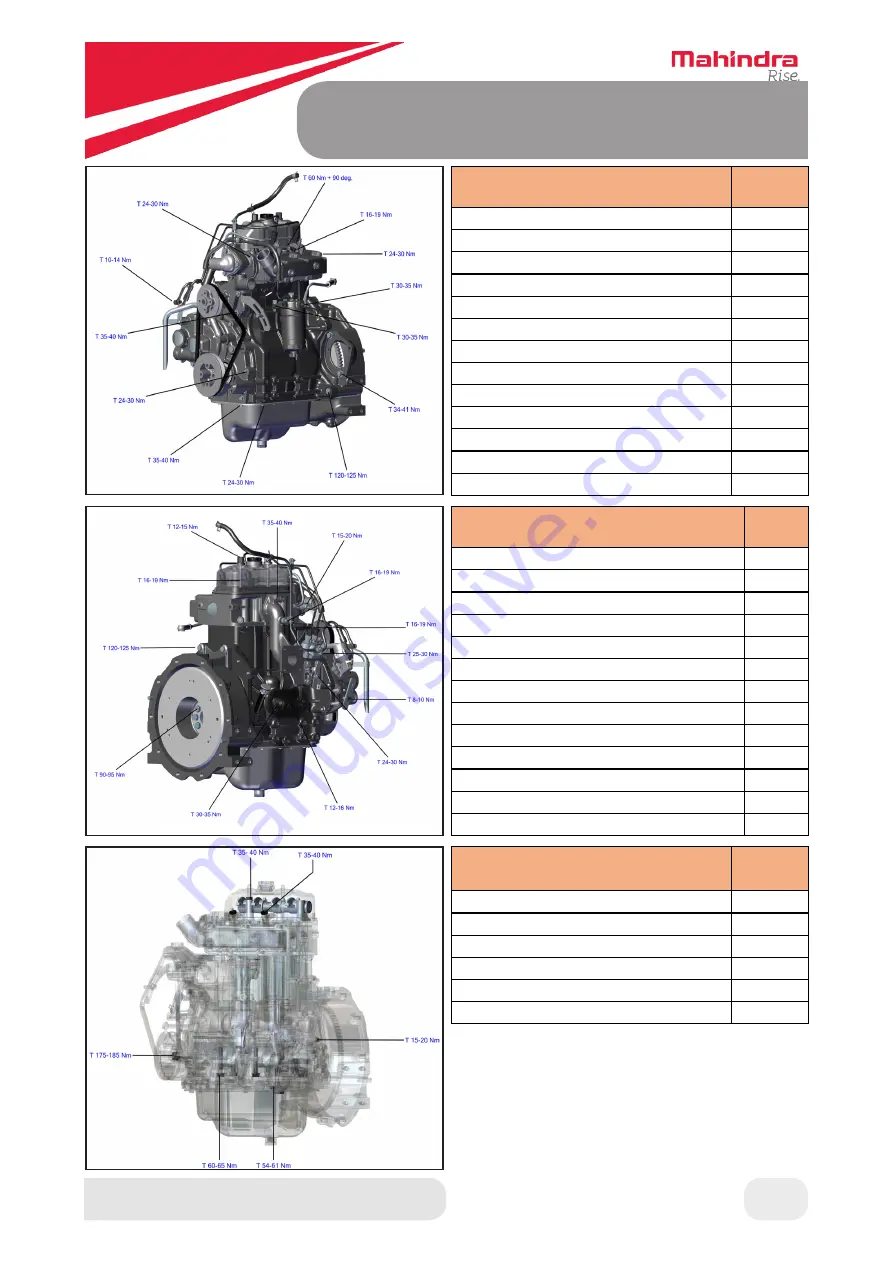
ENGINE TORQUE CHART
ENGINE ASSEMBLY
PART DESCRIPTON
Torque
(Nm)
NUT assembling con rod with crankshaft
54-61
BOLT main bearing cap M12 x1.75
60-65
BOLT mounting Crank pulley to Crank Shaft
175-185
BOLT mounting rocker arm with stud
35-40
NUT for Nozzle holder clamp
35-40
MOG Plug
15-20
71
PART DESCRIPTON
Torque
(Nm)
OIL FILTER
12-16
ADAPTOR oil filter
30-35
BOLT mounitng Flywheel to Crank Shaft
90-95
BOLT mounting from flywheel side
120-125
STUD for mounting Valve housing cover
16-19
CAP NUT for Valve housing cover
12-15
BOLT head to stub pipe mounting
35-40
STUD head to stub pipe mounting
16-19
ADAPTER water pump
15-20
STUD mounting FIP to crank Case
16-19
NUT mounting FIP to crank Case
25-30
BOLT mounting Pull to stop lever to pull to stop shaft
08-10
NUT nylock locking pull to stop lever
24-30
PART DESCRIPTON
Torque
(Nm)
BOLT assembling Crankcase to flywheel housing
120-125
BOLT mounting oil pan to crankcase
24-30
BOLT mounting oil pan to front cover
35-40
BOLT mounting FC to crank case
24-30
BOLT mounting Brace to water pump stud
35-40
BANJO BOLT conecting hose to feed pump
10-14
BOLT for thermostat housing
24-30
BOLR for mounting Cylinder head with crankcase
60 Nm+90
˚
STUDS for holding injector
16-19
BOLTS for mounting Intake manifold
24-30
BOLT for Fuel filter pipe outlet connection
30-35
BOLT for mounting fuel filter to bracket
30-35
BOLT for starter motor mounting
34-41
Summary of Contents for Jivo 245 DI
Page 1: ...SERVICE MANUAL...
Page 4: ...GENERAL...
Page 6: ...PRODUCT SPECIFICATION GENERAL 6...
Page 8: ...MAINTENANCE...
Page 23: ...FRONT WIRING HARNESS LAYOUT MAINTENANCE 23...
Page 24: ...REAR WIRING HARNESS LAYOUT MAINTENANCE 24...
Page 25: ...4WD FRONT AXLE ASSEMBLY...
Page 26: ...BEARING OIL SEAL POSITION 4WD FRONT AXLE TORQUE VALUES 4WD FRONT AXLE ASSEMBLY 26...
Page 28: ...4WD FRONT AXLE OIL GREASE SPECIFICATIONS MAINTENANCE 28...
Page 42: ...TRANSMISSION...
Page 43: ...BEARING OIL SEAL POSITIONS TRANSMISSION TORQUE VALUES TRANSMISSION MAIN LINE ASSEMBLY 43...
Page 44: ...TRANSMISSION OIL AND GREASE SPECIFICATIONS TRANSMISSION MAIN LINE ASSEMBLY 44...
Page 69: ...ENGINE...
Page 70: ...DETAILED ENGINE SPECIFICATIONS ENGINE ASSEMBLY 70...